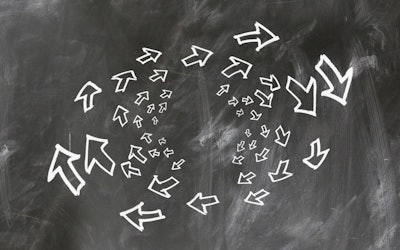
The Institute for Advanced Composites Manufacturing Innovation (IACMI) has teamed up with carbon fiber recycling start-up Vartega and other industry and research partners on a two-year project to improve the recyclability of automotive carbon fiber prepreg manufacturing scrap.
IACMI is a consortium devoted to advanced composites, driven by the support of the University of Tennessee and the U.S. Department of Energy. It operates development space in five locations throughout the United States and coordinates a network of industry partners and laboratories.
“Carbon fiber recycling technology has matured significantly over the past decade, but several challenges still exist in producing materials at automotive scale. We recognized that a holistic approach needed to be taken to create supply chain solutions for recycled carbon fiber,” said Andrew Maxey, Vartega CEO. “In our work with the project team we’ll be able to demonstrate the viability of a circular economy for recycled carbon fiber combined with optimized chemistries and commercial scale thermoplastic processing for automotive applications.”
That includes both the initial chemical treatment of the carbon fiber and ways it might be recycled at the end of a car’s life.
“Prepreg carbon fiber scrap has historically not been recycled,” said Maxey in an interview with Manufacturing.net on Tuesday, Oct. 24. “It’s a composite material, so it has both a fiber and a resin component, and those two components are difficult to separate. There are alternative recycling technologies that do exist, primarily pyrolysis, but the adoption of that technology has been a little slow just because composite recycling is difficult to do. The difference is this is chemical based recycling by taking the resin and essentially washing it off the carbon fiber, which allows us to keep the properties of the carbon fiber and reuse it in applications where strength and stiffness are very important.”
As part of creating a functional supply chain of automotive carbon fiber prepreg manufacturing scrap, Ford and BASF in particular will be working on scaling the project’s findings to a commercial scale. BASF is Ford’s major supplier of thermoplastics. Scrap from Plasan Carbon Composites will make up some of the primary feed stocks.
“The overarching goal of the project is actually to reduce variability in the material supply chain and actually create consistency of the product in terms of quality and capacity so that [someone like Ford or BASF] can reply on that supply chain,” Maxey said.
“…Being able to recover the value through techniques such as Vartega is offering is critical in terms of the overall economics,” said Ray Boeman, IACMI.
Other project partners include Michelman, Oak Ridge National Laboratory, Colorado School of Mines, Michigan State University, the University of Dayton Research Laboratory, and the University of Tennessee, Knoxville.