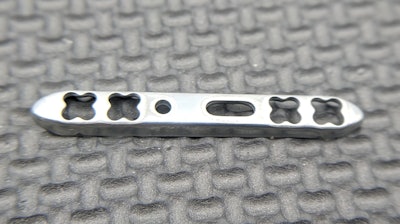
A divide is growing in advanced manufacturing. Engineers are successfully designing new, advanced components for critical industries with tougher materials, tighter tolerances and improved surface quality, all enhancing the parts’ capabilities and lifespan. However, these advancements are stifled by the inherent limitations of conventional material removal processes, including heat-affected zones, recast layers, and tool wear.
In short, advancements in part materials or designs can only go so far as the manufacturing processes needed to produce them. These limitations are further exacerbated when increased demand warrants higher production volumes.
Rather than going back to the drawing board to re-design parts with more machinable materials or looser tolerances to accommodate existing machining methods, manufacturers should consider alternative machining processes instead. One such technology is pulsed electrochemical machining, a non-contact, non-thermal material removal method capable of machining tough alloys, small features such as small-diameter, high aspect-ratio holes, and superfinished surfaces for components in a variety of critical industries with a high level of efficiency that may meet growing demand for advanced components.
Before we explain its utility in closing this ‘gap’ for critical industries, We can best explain PECM technology by learning its four key components:
- The Cathode, also called the electrode, is the tooling in ECM that is designed as the inverse of the desired geometry on the workpiece. The cathode is custom-designed for each project. It is lowered onto the workpiece during machining, separated by a microscopic gap called the inter-electrode gap (IEG), but never actually comes into contact with the workpiece.
- The Anode, or the workpiece, can theoretically be any conductive material, but the process is particularly effective on tough-to-machine metals. ECM can be used on bar stock or raw plates to form the desired geometry, but is generally used on near-net shape parts that are stamped, rough machined, etc.
- The electrolytic fluid serves two critical purposes simultaneously. While it is flushed through the inter-electrode gap, the fluid works as the catalyst for the electrochemical reaction to occur, removing the anode material atom-by-atom. Additionally, the fluid works as a flushing agent that removes both heat and waste products from the workpiece area, helping leave a smooth surface finish.
- The power supply supplies the electrolytic fluid with the necessary current to conduct the electrochemical reaction; this current is correlated with PECM’s material removal rate.
(This is only a brief summary of the technology—for a more in-depth analysis on how PECM removes materials atom-by-atom using an electrochemical reaction, consider reading this article.)
Industries and Applications
Aerospace manufacturers are encouraged to miniaturize critical components to help lightweight aircrafts for increased fuel efficiency, and a prominent example of this can be found within microchannel heat exchangers. A heat exchanger’s efficiency is correlated to the quantity of surface area, as well as the length of the path that the fluid travels throughout the system; therefore, aerospace engineers are designing new heat exchangers with improved heat transfer abilities including thinner walls, tighter spacing and higher aspect ratios.
However, these smaller features make the heat exchangers susceptible to thermal distortion or tool vibration, commonly found in conventional machining processes. Furthermore, aerospace manufacturers are increasingly utilizing advanced materials in critical components that have higher tensile strength, corrosion resistance, and extreme temperature-flux resistance, such as nickel superalloys and bulk metallic glasses. These materials, however, are known to wear down tools quickly.
Some of these feasibility hurdles can be avoided with PECM due to its unique abilities. For example, its non-contact and non-thermal properties allow PECM to machine features sensitive to heat or tool vibration, such as thin walls—down to <0.075mm or <0.003” thick walls with a 20:1 aspect ratio. Additionally, these properties help it avoid surface irregularities found in heat-based processes, such as burrs or recast layers.
Furthermore, PECM is capable of processing multiple features in parallel with a single custom-designed tool, allowing it to machine tens or even hundreds of heat exchanger features simultaneously, down to <10um repeatability. Finally, since PECM is concerned with the conductivity of a given material, rather than its material hardness—it can machine tough materials such as refractory metals or cobalt alloys at a similar speed to copper, without concern for toughness.
PECM, however, has limitations; it will not work on any non-conductive materials such as plastics or polymers. Additionally, designing the tooling is an iterative and complex engineering process that can take several months and require high NRE costs-- making PECM nonideal for projects that are low-volume, prototyping, or with short-term deadlines.
Medical device manufacturers are designing increasingly smaller, more geometrically complex components to allow minimally invasive surgical procedures, minimizing risks and reducing patient discomfort. Additionally, implantable medical devices often require the use of tough, biocompatible, corrosion-resistant metals such as grade 2 titanium or nitinol.
Furthermore, implantable medical devices may require superfinished surfaces on high-contact areas to limit friction, of which can cause patient discomfort, the release of cytotoxic materials or part failure. Implants may also require differing degrees of surface finish on specific areas. For instance, hip replacement devices may require superfinished surfaces in the acetabulum area to minimize friction with the hip joint, but may also require a rough, porous surface on the stem to promote osseointegration with the patient’s femur.
PECM is well-suited to adapt to the need for both improved and more selective surface finishes on a single component. As PECM removes the workpiece material atom-by-atom, it therefore machines and finishes a part simultaneously—allowing surface qualities down to .005-.4um Ra. Additionally, the usage of a custom-designed cathode can allow PECM to selectively finish certain areas of a part to differing degrees of surface quality—or not machine at all.
Instead of adhering to the constraints of the machining processes, it may sometimes be best for manufacturers to upgrade existing machining technology to “catch up” by adapting to new market demands and engineering challenges, and unconventional processes like PECM may be the ideal candidates to allow this growth.