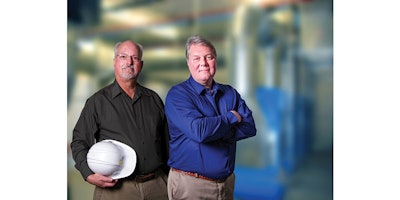
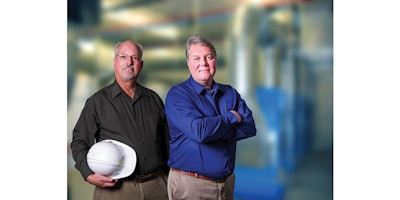
When considering optimum performance within a manufacturing environment, many focus on three obvious factors: people, process and product. Did you know that there are also three often-overlooked components that play a critical role in a successful outcome, and they all hinge on the facility’s HVAC architecture?
As the heart, mind and soul of a production facility’s airflow, the HVAC system should never be taken for granted, or be expected to “make do” or “work around” changes in the plant environment or process. In fact, a company’s HVAC structure should be seriously regarded as the responsible driving force that it is. To ensure HVAC efficiency, food manufacturers should pay close attention to measurement, control integration and customization. Together, they form the Food Manufacturing Trifecta, or three pieces you don’t want to overlook in daily operations.
#1: HVAC Measurement
One thing is certain: Change is inevitable. Food manufacturing is not exempt from this, requiring the plant environment to evolve along with new technology and market demands. Buildings grow in size to accommodate increased production, but subsequent additions to the physical plant may not be integrated effectively with the original layout.
HVAC equipment, intended to service a certain space, is expected to continue operating efficiently within a completely reconfigured area and different performance parameters. The result? What once worked actually ends up being counterproductive. This can then lead to detriments and inefficiencies such as temperature comfort issues or product contamination.
When dealing with original equipment and reconstruction, the only accurate method to determine existing conditions is field measurement during process operation. Blueprint and/or nameplate data analysis is simply not enough to determine true, real-time facility function with respect to airflow. Cataloging each piece of HVAC equipment and its performance, along with the physical size of each space, is the only way to understand how the air in the building is moving throughout the manufacturing process. Once good data has been collected and analyzed, it is then possible to make educated determinations for makeup air and/or exhaust needs. In some cases, equipment can be decommissioned to achieve the desired results from a food safety standpoint. The field measurement exercise may also uncover equipment that is not functioning properly or was installed incorrectly, allowing for equipment to be serviced accordingly.
#2: Control Integration
Without measurement, it is impossible to approach control integration. Analysis is where we begin to understand how supply air and exhaust fans are actually operating. They may be running independently, or simply on temperature set point and time clock functions for start/stop, but to really gain control over a building’s HVAC system the components need to operate together.
Used as a verb, integrate is defined as “to combine into one unified system.” When we talk about HVAC control, this should be applied to pairing equipment operation with an overall goal of positive pressurization. From where raw materials are received, to the manufacturing process itself and ultimately to the final, packaged product, an integrated control system can eliminate many possible conflicts when constant human intervention is necessary.
This integration of controls using standard PLC logic-based devices, pressure differential measurement, temperature and humidity set point, and variable speed frequency drives allows an HVAC system to operate virtually hands-free with the exception of routine maintenance. Having an airflow set to operate by design without continuous input from the plant engineering department shifts the focus where it should be: on the product manufacturing process.
As with many things, there is more than one way to approach HVAC control integration. The key is to select a method that is flexible – one that meets short-term needs, but can also respond in a user-friendly way to changes in plant, product or operations. A well-devised control system will automatically maintain differential pressure in food safety zones, operate HVAC equipment in concert with the manufacturing process and save energy in the long run.
#3: Customization
It has been said that good design is where form and function come together as one. Ventilation systems are no different when considering their role in the big picture of the complex world of food manufacturing environments. Using a “cookie cutter” approach will not produce the desired outcome in this setting; instead, acquiring real-time data and then incorporating the findings into the HVAC system design is the way to customize a solution that will be effective and efficient.
By using thermodynamics, mathematics and physics, we can begin to understand and assemble a system that operates inside a given set of established parameters. Special considerations must be given when addressing process-driven conditions in the facility, including moisture, heat, indoor air quality and VOCs. How these elements are controlled with respect to airflow needs in the plant will play a significant role in the ultimate design of an integrated HVAC system, which will then support the manufacturing process.
The most important thing to remember is that every environment is unique, and has its own set of considerations that should not be ignored. In this way, every HVAC system is a "special order," but combining accurate data with sound analysis will ensure that in the end, you will have it your way.
About Energy Recovery Partners
Partners Bob Nelson and Paul Ziehr are the founding members of Energy Recovery Partners (ERP), headquartered in Hubertus, Wisconsin. Predominantly focused on environmental solutions, ERP excels in system design and engineering, equipment recommendations, turnkey installations, and project management for food processing and other manufacturing-based companies. Visit www.engergyrecoverypartners.com to learn more about ERP’s approach for transforming waste heat energy and HVAC inefficiencies into manufacturing process improvements.