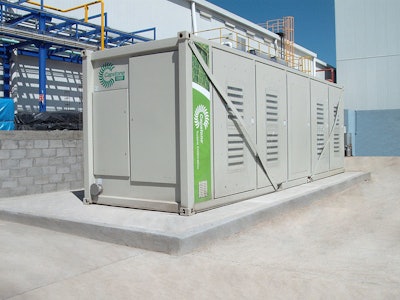
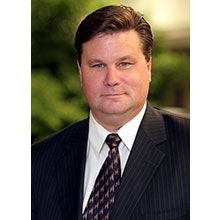
In an ongoing effort to improve efficiency, reduce costs and lower dependence on local utilities, a growing number of food manufacturing plants have been seeking to implement cutting-edge energy solutions. Prominent among these are microturbine technology.
In simple terms, microturbines are small combustion turbines approximately the size of a refrigerator. They are comprised of a compressor, combustor, turbine, recuperator (a device that captures waste heat to improve the efficiency of the compressor stage) and a generator. They work as follows: Fuel enters a combustion chamber; the turbine can run on natural gas, propane, biogas, diesel, kerosene and associated gas, to name a few. The hot combustion gases expand and spin a turbine wheel, which is connected to the shaft of an electrical generator. The exhaust transfers heat to incoming air via a recuperator. Air passes through a compressor and is warmed by the exhaust gases before entering the combustion chamber, pre-heating the combustion process and increasing simple cycle efficiency.
For food manufacturing plants, microturbines offer a wide range of benefits. Critical to the design of turbines are the bearings inside that lubricate the turbine shaft. Traditionally, oil-cooled ball bearings, or thrust bearings, have been used in this way. However, with advances in airfoil technology, air bearings have become the cleaner and more reliable alternative as there are no lubricants or coolants needed to operate. With far fewer moving parts than a reciprocating engine, microturbines require far less maintenance. A microturbine with one moving part translates to the least amount of service needed over the life of the unit. Microturbine systems operate on a wide range of fuels, offer ultralow emissions and provide highly reliable and flexible onsite energy generation. And thanks to advanced combustion controls, they can achieve these low emissions without a need for exhaust aftertreatment.
What follows are just a few examples of actual microturbine installations and how they have been helping food manufacturing plants worldwide achieve the energy efficiency and reduction in operating costs that they are striving for.
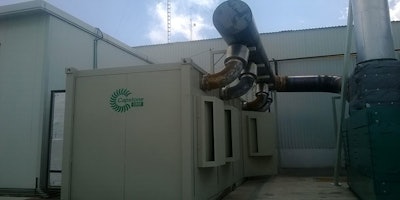
A bread factory in Pskov, Russia installed five microturbines in a combined heat and power (CHP) configuration along with five gas boosters and two gas boilers. The thermal energy from the microturbine exhaust is captured to heat the building and provide hot water to all of the facilities. The microturbines are achieving efficiency of up to 90 percent, with 2kW of thermal energy created for every kW of electricity provided. The microturbine CHP plant is able to reduce the cost of electricity generated at the factory to three times less than the cost of utility power. The quiet operation, reduced weight and compact footprint allows the microturbines to be easily installed on the roof of an existing structure at the factory, keeping capital costs low and ensuring a rapid payback.
Fueled by biogas produced onsite, a microturbine was installed at a leading pork producer in Lithuania in a CHP application along with an anaerobic digester, fuel compressor and heat exchanger. With energy efficiency levels approaching 80 percent, the “green waste” energy system converts organic solid waste into clean, renewable energy for the meat production facility. In addition, the exhaust from the microturbine is captured to produce thermal heat at a high level of efficiency.
A large food manufacturer in Mexico commissioned and installed a microturbine to lower carbon emissions from its 50,000-square-foot food plant, which for years had relied solely on utility power. At the plant, the microturbine, coupled with a waste heat recovery generator, serves as baseload power connected to the grid, with the remaining power supplied by the grid.
In Italy, two food manufacturers turned to microturbines in a quest to upgrade the power generation at their respective facilities, requiring not only clean and reliable electricity but also steam for their manufacturing processes. The microturbines, coupled with a post-combuster burner and steam boiler, allow both manufacturing sites to significantly improve their overall energy efficiency. The exhaust from the steam generator is captured to make hot water for the building via a heat exchanger, further boosting the overall system efficiency to more than 90 percent. Traditional reciprocating engines struggle in this type of CHP application. At a separate site in Italy, a pasta factory installed a natural gas-powered microturbine to power and heat its facility as well as to produce hot water for pasta production.
And in Austria, a packaging plant for prepared fruits and vegetables, seeking to upgrade its outdated equipment, installed a microturbine in a CHP application to generate electricity as well as exhaust heat used as combustion air for an onsite steam boiler. Using the hot, oxygen-rich microturbine exhaust as a boiler combustion feed reduces the energy required by the boiler for steam production. During periods where there is excess heat, an absorption chiller can also be used to produce cold water. The presence of the microturbine also gives the plant the option to operate in standalone mode in the case of a grid failure. Previously, and due to the local weather in the summer and location of the plant on the grid, the facility had been experiencing up to two grid failures per week; if a grid failure occurred during production, the food could not be tinned, incurring considerable expense. By offering a layer of fault protection, the microturbine allows the packaging plant to complete production, all while reducing waste. High fuel efficiency is achieved while maintaining a high turndown ratio. At 40 percent or greater system utilization, the plant is able to operate at efficiencies of 90 to 96 percent.
The advantages of implementing microturbine solutions in these applications help to make them attractive options for owners and operators within the food manufacturing industry.
Darren Jamison is president and CEO of Capstone Turbine Corporation, the world's leading clean technology manufacturer of microturbine energy systems.