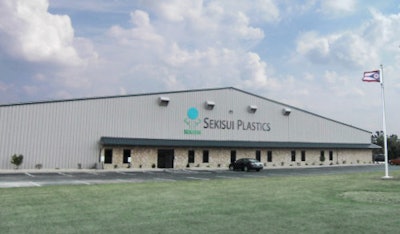
MOUNT PLEASANT, TN — Sekisui Plastics USA (SPUS) on Wednesday announced the opening of its new $5.2 million manufacturing facility in Kenton, Ohio. The plant will initially produce foam products molded mainly from Piocelan hybrid moldable foam resin for use in automotive parts, baby seat core parts, and other industrial markets such as protective packaging. The new facility will increase the company’s molding capacity by about 40 percent with room for future growth.
“Since opening our first U.S. manufacturing plant in Tennessee in 2007, we have experienced tremendous growth in the South/Central region of the U.S.,” said Thomas Pontiff, President of SPUS. “This new manufacturing plant in Kenton gives us the molding capacity we need for our expanding customer base in the North/Central region of the country. And, it puts us in closer proximity to both our current and targeted OEM customers who require just-in-time delivery. In addition, it gives us the benefits of multiple location supply in case of emergency.”
The 80,000 square foot facility includes both manufacturing and office space. “It houses our tooling development and machining operation, which includes part and tool design, tooling manufacturing, modification and repair,” said Pontiff. “The new facility has CAD design capability, which enables our designers to put on paper the part designs and easily have tooling made from them. With the addition of CAD and CAE capabilities in our Michigan sales office and tech center, we are moving towards full capability for product and part design, testing and verification from initial concept to production. We expect to add material property testing capabilities in the near future.”
The facility’s initial molding capacity for 20-40 metric tons per month is expected to increase to 100 metric tons in the near future. “We will initially mold products designed for automotive energy absorption and safety, automotive light-weighting, and automotive sound absorption,” said Pontiff. “We will also produce packaging products for complex automotive parts for transport, as well as consumer and industrial protective packaging.”
Future plans for the Kenton facility include producing the actual raw material used to mold its various products, and for other manufacturing capabilities to support new markets. “Depending upon future requirements and business development efforts, this location could house Piocelan foamable resin production and extrusion capabilities for various foamed and unfoamed products,” said Pontiff