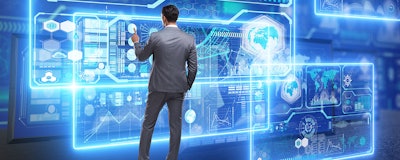
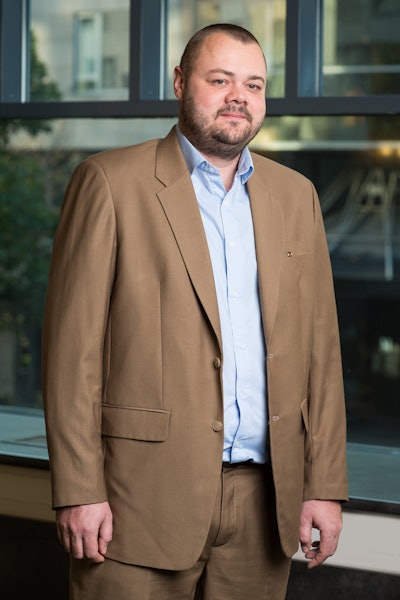
There are two rules of thumb about manufacturing failures. First, they happen. Second, they usually don’t happen by accident. Companies that produce electronics, comprised of hundreds of components, know these rules very well.
No matter what is being manufactured, failures pose a risk of lost credibility, a damaged reputation among customers and burdens the company with additional costs. For these reasons, it is in the manufacturer’s best interest to employ processes that can mitigate failures from occurring while contributing to the company’s business performance.
One such process involves data collection, analysis and monitoring during manufacturing. Data collection has several benefits including quicker and more accurate failure impact identification, continuous improvement on failures and increasing the value of quality manufacturing.
What does data collection look like? One such system uses barcode technology to capture the serial number, version number and batch information for each component. The manufacturing production line also collects information from the manufacturing equipment, such as temperature, physical clearances, other statistics and perhaps even pictures. The data from each manufacturing batch is fed back into a software system with integration into an ERP system that has vendor information for each component.
Using the manufacturing of a PC board as an example, below we discuss each of these data collection benefits.
Impact Identification
With a data collection system in place, the entire “genealogy” of each product can be tracked and monitored. Consider that a PC board may have 200 or more unique parts. The data collection system allows you to drill down for detailed information about each component. In this way, you are able to track the entire history of every PCB board that has left the manufacturing line.
When a failure is identified, often through customer returns, you will be able to pinpoint each PC board that has the failed component. Without this detailed data tracking, guess work is used to identify the PC boards manufactured during a time period when a batch of components were received. Or worse case, notifications are sent to customers that their product may be impacted. Usually a conservative approach is taken to ensure all customers that “may” be impacted are notified. The company must replace parts even if they are not actually part of the failed batch. In addition to the costs that represents, the quality reputation of the company is needlessly harmed.
At Y Soft, we use a 2D barcode which is laser-engraved directly onto each PC board. As the board progresses through the production line, information about each component used is added to the barcode. The finished board contains all the component information as well as information about the production machine (clearances, temperature etc.). The process continues to final assembly and shipping with the result being the entire process is captured before the product leaves the facility.
Should a component failure be identified, the database quickly and easily identifies the impacted boards, who supplied the components, in what conditions those components were assembled and most importantly which other product units have the same component and the customers impacted.
Continuously Improve Prevention and Manufacturing Quality
It is not uncommon for bad components to be identified during the manufacturing process, during quality testing or through visual inspections. As data is collected during the process, it may be discovered that a higher than normal failure rate is occurring. This information may help manufacturing proactively figure out the problem whether it be in the component itself or with some aspect of the production line.
During the quality testing process, it is not feasible to simulate testing for how long the customer will use it and the environmental conditions of its use.
However long you test a component or a PC board filled with components, the actual customer usage time and environmental conditions cannot be easily replicated. However, if you combine your quality test output with analysis of failure reports from customers, it is possible to start to track “failure trends” which can help you improve the manufacturing process in several ways. For example, over time you can optimize your supplier network to use components that are not prone to faults and which are compatible with other components. Or you can use the trend data to identify customer installations where a high probability of a failure exists and take steps to prevent the failure with timely service actions.
Raise the Business Value of Hardware
Implementing an automated data collection system is not without cost. In our experience, operational costs tied to our manufacturing line increased by 15 percent. One should also consider the capital costs for equipment purchases, such as the laser 2D barcode engraver in our case. But the key business value for a manufacturer lies in the lower number of manufacturing failures, the ability to prevent failures and the ability to quickly and precisely identify impacted customers.
For Y Soft, where 90% of our hardware products containing PC boards are shipped outside of our home country - Czech Republic, repair costs can be high and often are more than the price of the device. We are also able to use quality as a marketing differentiator. Overall, the initial and ongoing operating costs of the data collection system were recouped in a short time.
Lessons Learned
The implementation of our data collection system took six months and the time/effort needed should not be underestimated. The data collection itself was easy; the time consuming part was integration with existing systems such as stock management systems, ERP, ordering systems of suppliers and other integrations. It can be more complicated than it looks and planning will be required. The system also required an initial learning curve and training for manufacturing staff to learn new processes. Once the system is in place, don’t ignore the data. Doing so will only impact you down the road through higher costs and headaches.
Marcel Fejtek is Chief Operating Officer at Y Soft.