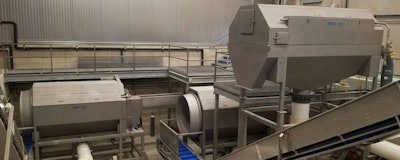
For designers of industrial wastewater systems asking the right questions upfront can make the difference between a selecting a rotary drum screening solution that is a resounding success and one that becomes a burden on the plant. To determine the right screening for specific industrial applications, first area to focus on is the source — the wastewater — and asking some very important questions. Looking closely at the wastewater and gathering information from it will dictate what approach is the best.
While those who work at the industrial plant can certainly offer insight into their wastewater, the big picture doesn’t always become automatically clear. A total understanding of an industrial plant’s wastewater can sometimes be a bit of a mystery at first. Here are 5 questions you should answer to solve that mystery and ultimately choose the right drum screening technology for your plant.
1) What Contaminants Are In The Wastewater?
Higher levels of fats, oils, and grease (FOG) are common in many industrial operations. Screening should be designed to accommodate the maximum FOG load possible in these operations. Other wastewater contaminants in the water should also be considered when selecting screening, including corrosive matter, salt content, and surface active agents like the chemicals used in plant cleaning processes.
2) What Is The Flow Rate?
How quickly or slowly the wastewater will pass through the screen is also an important point to consider during the selection process. Screening decisions should be made based on the maximum flow rate possible for optimal effectiveness. Low flow rates must also be considered.
A screen designed for a high flow installed in a plant with a low flow will lead to solids settling and create other operational issues.
3) How Important Are Byproducts?
To determine the type of screen necessary for an industrial application it is also necessary to determine what the screen should and should not capture. In many industrial applications there is a need for certain sized particles to be screened out of the effluent and reused for another purpose. The screened byproduct can be a revenue generator for the company and cannot be ignored. After determining the target size of the particles to be captured, a screen with appropriately sized opening can be selected.
4) What Solids Are In The Wastewater?
Screen “blinding” can occur if the type and shape of the solids in the wastewater are not considered when selecting screening. Items like hair, fiber, or other stringy materials may wind around the openings in a screen and cause clogs. Feathers, which are thin on one end but larger on the other, can also easily slip into screen openings and get stuck, blocking the flow. But if you clearly understand what solids are in the wastewater there are types of screens and design features that can prevent blinding from happening.
Self-cleaning screens or screens that include a mechanism to keep solids brushed off may be required for some industrial applications. Technology can also be added to a screening scheme that diverts solids away from the screen openings. There are also variety of different wastewater delivery systems that introduce the flow to the drum screen so that solids are bouncing and moving and being washed away from the openings. Keeping the flow paths open allows the fluids to easily drain out. Bottom line is you need a drum screen design such that if your unique solids did get into the screen, they will also be washed out.
5) What Is The Full Wastewater Treatment Scheme?
Many industrial plants require multiple screens, designed to target different wastewater streams throughout the plant. Understanding what other screens and treatment methods are being utilized at the plant is important to determine which style screens should be installed.
If the drum screens are the sole treatment method, screens capable of getting as much as possible out of the wastewater need to be selected. If there are other downstream processes involved, and screening is just part of the process, that knowledge will impact the type of screen that is needed.
When installing screens at industrial plants, it is important to screen as close to the wastewater source as possible. This prevents natural breakdown and makes it easier to separate the maximum number of solids out of the wastewater.
Questions Worth The Effort
These are the standard questions that JWC Environmental is looking to answer for all of its IPEC industrial drum screen installations. Taking the time to understand the wastewater completely before selecting and installing a drum screen solution can be a lot of work, but it will pay off for you, the plant and the success of the project.
Kevin Bates is the Director, Global Marketing at JWC Environmental. Bates brings more than 20 years of experience leading marketing, product management, operations and engineering teams in a variety of global companies. His strong background industrial products have been developed in multiple industries including oil and gas, automotive, construction and mining.