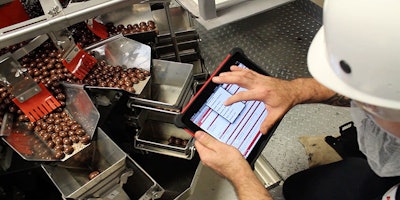
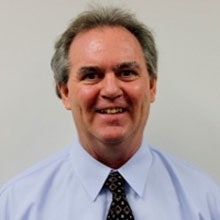
Equipment maintenance has been cited as the food manufacturing industry’s secret ingredient. Food Manufacturing recently had the opportunity to correspond with Advanced Technology Systems Director of Technical Training and Advanced Systems Mark Cox about the topic of predictive maintenance in manufacturing.
Q: What is predictive maintenance, and what are the primary benefits that come with it in regard to manufacturing?
Synonymous with condition-based maintenance, Predictive Maintenance (PdM) relies on an assessment of in-service equipment "health" or condition, based on non-intrusive testing that uncovers trending parameters that can be related to known failure mechanisms and how they develop and/or deteriorate. The PdM concept is based on the assumption that the deterioration of components can be measured over time. The goal of using predictive maintenance within a manufacturing environment is to extend the maintenance interval period to reduce intervention activity and cost, and to extend service intervals to prevent a shutdown of equipment for intrusive overhaul. The approach promises cost savings over routine, time-based Preventive Maintenance (PM), and is obviously superior in efficiency and cost effectiveness to Reactive Maintenance, or waiting until equipment failure to act.
Q: Can you describe the technologies behind the process(es)?
There are four primary technologies behind PdM: vibration analysis, ultrasound, oil analysis and infrared thermography.
Vibration analysis is the most commonly used method for analyzing the health of rotating machines. Measurements can be taken on bearing housings with piezo-electric transducers to measure the vibrations; the level of vibration can be compared with historical trends and alarm values. Ultrasound monitoring is widely used within condition monitoring, energy conservation and quality assurance programs. It aids in locating a variety of potential problems in a wide range of equipment types; the primary goals include leak detection, mechanical inspection/trending and electrical inspection. Oil analysis is a key component of PdM and includes analysis of lubricating and hydraulic oils, spectrochemicals and water particles to determine the condition of the lubricant, and thereby assess their ability to perform as expected. Finally, infrared thermography, one of the key components of PdM, captures thermal radiation images of equipment and components, and can be successfully utilized to find potential issues on a wide variety of equipment types. The images can be used to discover hot areas of components (due to excessive friction, worn or loose parts, poorly connected or deteriorating wiring, overcurrent conditions, lack of cooling and unbalanced loading, for example) that are indicators of potential failures.
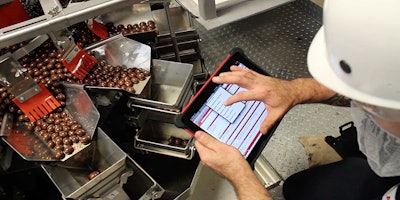
Q: What are the most current best practices in CPG equipment maintenance?
As businesses become more mature in their approach to maintenance, there is a drive toward bespoke strategies that are based on overall business goals, as well as asset criticality rather than asset type. This approach ensures that valuable resources are focused not only on best practices that will accelerate performance but also those that will fit culturally within an organization. Improved performance can be achieved by a mixture of any of the following strategies:
- A robust approach to knowledge transfer of intelligence on equipment issues
- A data-driven approach to identification and elimination of losses whether through short stops, breakdowns, changeover or component/raw material issues
- Increased use of operator maintainers for first line maintenance, lubrication and changeovers
- A cross-functional approach to driving improvement between maintenance and operations
- An integrated approach to planning and scheduling of work with Operations
- A structured approach to understanding asset condition and constraints, and development of long-term asset plans that extend life or replace assets proactively with a focus on early equipment management and life cycle costing
- Development of technicians that can free organizations from the dependency on OEM’s
- Deployment of a structured methodology to determine maintenance strategy for critical assets using techniques such as failure mode analysis of Reliability Centered Maintenance (RCM) where improvement in reliability performance is required
Q: How does maintenance for food and CPG differ from other industries like automotive, heavy equipment, etc?
Maintenance of assets in the food industry or CPG may be constrained by requirements for routine changeover and clean-downs for hygiene or regulatory reasons, or, in some cases, working per a very short delivery cycle for perishable products. In the pharmaceutical industry, as another example, there are also constraints due to validation of equipment, which requires robust documentation to verify that an asset is designed, installed, maintained and operated as intended without risk to patients.
Q: How has CPG equipment advanced over the last few years? What is next in maintenance technology for CPG?
Current trends include increased automation for changeovers, improved safety controls and devices, enhanced sensors and detection systems for product quality control, and increased use of 3D printing to support the supply chain with readily available parts.
As the collection and analysis of big data continues to be more cost effective and connectivity technology increases, predictive analytics will be more commonplace. These analytics will drive a scenario where equipment will increasingly make automated adjustments to out-of-tolerance situations, and address potential stoppages or failures before deviations occur to a point where they have a negative impact on business. This, in turn, will have a consequential impact on the skill set of technicians who will be required to interrogate data as part of their everyday routine.