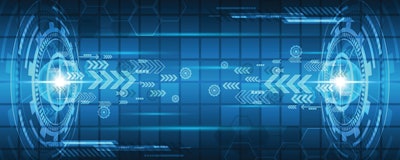
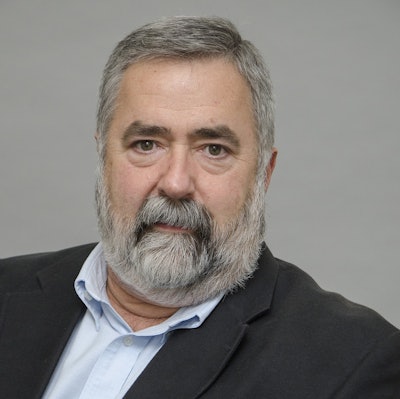
A Digital Twin (DT) is a software model of a process and/or product. Though we don’t often think of it as such, a 3D CAD model with semantic tolerances (a Model-Based Definition) is a digital twin of a to-be manufactured part.
Essential in discrete part manufacturing, Computer Numerical Controlled (CNC) Coordinate Measurements Machines (CMMs) are type of automatic machine designed to verify a part’s dimensional compliance to a 3D CAD model, validate the associated manufacturing process, and provide actionable data for process correction and design optimization.
CNC CMMs are very effective in executing programs for these dimensional metrology tasks, but have an incomplete awareness of itself and of the overall context of the manufacturing process in which it resides.
Completing a Digital Twin for a CNC CMM first requires that a 3D-software model of the physical machine is created by the CMM’s manufacturer and made available to the owner of the CMM. Functional capabilities (speed, accuracy, working volume for any configured CMM are then associated with the 3D software model. To further complete the Digital Twin, the machine’s kinematic capabilities are also integrated into the 3D software model.
At this point, when synchronized to its real counterpart on the shop floor, the CMM’s Digital Twin is driven by the actual CMM’s operation and can include real-time measured results and process data. This driven Digital Twin can be displayed locally or at a multi-machine monitoring station, or on a tablet while the responsible operator or owner is elsewhere.
To enable a CMM’s Digital Twin to support driving a physical CMM, it is necessary to add another layer of awareness to the Digital Twin’s 3D software model. Humans are quite adept at task-based planning, and a CMM Digital Twin should have complementary capabilities in the highly technical topic of dimensional measurement process planning.
The complex task of measurement planning first requires the CMM’s Digital Twin be able to import and process the 3D model of the part and its precise nominal boundaries and tolerances.
The CMM’s Digital Twin then applies, based upon a company’s measurement best practices (a set of editable rules) and the Digital Twin’s associated capabilities to determine what can be automatically measured and what cannot. The final steps in this Digital Twin workflow are collision avoidance calculations, graphical 3D simulation, and the automatic generation of a CNC CMM part program. The person overseeing the measurement process plan generation has the final option to approve or override the Digital Twin’s recommended program.
In this extended use case, the smarter and more complete CMM Digital Twin can now drive its physical counterpart. The CMM Digital Twin can be locally connected to the physical CMM, or disconnected and operating independently on another software platform or at another location.
When disconnected, this now smart CMM Digital Twin operates in a software-based manufacturing process planning ‘what if’ system. As the CMM manufacturer’s library of Digital Twins can encompass hundreds of available models and configurations, narrowing the selected CMM in this larger context becomes practical, if not required. The selected Digital Twin can furthermore operate in simulation in a Smart Manufacturing planning process system to optimize the overall manufacturing process before actual execution on the shop floor.
Another emerging, but not yet widely implemented use case for Digital Twins includes not just CMMs but also Machining Centers, Material Handling Robots, and other Smart Machines connected peer-to-peer (machine to machine). Human mediated communication between CNC machines is the gold standard but can be tedious for a person. Programmable Logic Controllers (PLCs) are reliable for low level machine to machine communications, but are generally considered to be much less adaptable than people or a machine’s Digital Twin.
Heterogeneous Smart Digital Twins communicating peer-to-peer can be reliable as well adaptable (to a certain extent) to changing manufacturing requirements. This allows people to attend to exceptions and more effectively orchestrate these capable and smart engines of manufacturing.
The National Institute of Standards and Technology (NIST) in particular has taken the lead in the digital transformation of U.S. manufacturing by developing a working reference implementation with their Smart Manufacturing Systems (SMS) Test Bed project.
It’s contemplated that ‘Factory Intelligence’, whatever that may be, will emerge from the interactions from skilled staff and cyberphysical systems, with Digital Twins for metrology playing a key role.
Larry Maggiano is a Senior Systems Analyst at Mitutoyo America Corporation.