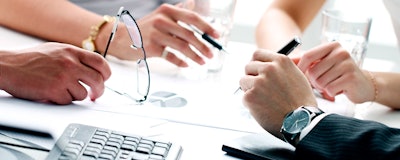
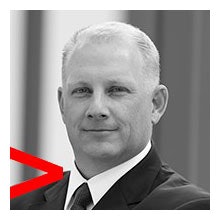
Meeting rapidly rising customer expectations is no longer just a priority issue for consumer-facing industries. These days, B2B customers are demanding more than ever — and their requests are just as complex and unpredictable as their consumer counterparts. Many customers expect the companies they do business with to do a lot more than just sell them a product. Customers are looking to suppliers for greater personalization, more frequent product launches and improved customer experiences. And today’s manufacturers are struggling to keep up.
That’s why the future of manufacturing will be dependent upon manufacturers’ ability to delegate the workload. Manufacturers must respond to the needs of high-demanding customers by building flexible “ecosystems” that leverage strategic partners and digital technologies to build a cohesive network of services, talent and ideas. Through manufacturing ecosystems, contractors and partners can play a greater role in innovation, production and distribution — improving efficiencies and optimizing product and service levels from start to finish.
Partnership networks have a proven track record of helping manufacturers meet customer needs and seize competitive advantage. Third-party partners bring an increasingly diverse set of capabilities to the table that can help manufacturers enhance their flexibility, responsiveness, and overall performance in an increasingly competitive landscape. According to Accenture Strategy research, manufacturers that use a higher percentage of third parties are more likely to have higher productivity, revenue, and margin than those that try to build and own the entire network
So what’s stopping manufacturers from adopting this partnership mindset? Most manufacturers’ production networks are rigid, financially constrained and disconnected geographically – making the transition to an ecosystem more challenging. In fact, recent research found that only about one in four manufacturers globally have an agile operating model that helps enable them to shift resources and activities around their manufacturing network in response to market developments or changes in demand, the situation is even more problematic for manufacturers that primarily operate their own facilities. These challenges make it difficult for manufacturers to prioritize the customer experience and differentiate themselves from the competition.
Compounding these challenges, most manufacturers have been slow, or unwilling, to adopt digital factory technologies that could help them be more responsive to their customers. We found that only about three in 10 manufacturers have implemented key digital technologies, such as IoT and design digitization, to create the agile structure necessary for an ecosystem to thrive. Second, with customer demands becoming more and more complex, manufacturers are choosing to bear the brunt of the work alone.
Research also revealed that, while more than half of global manufacturers do plan to increase their use of third parties, too many are using them to solve short-term issues — rather than to create long-term advantages. This marks a crucial missed opportunity for manufacturers to build more strategic and permanent partner networks that strengthen day-to-day operations while best positioning them to seize new value opportunities in the future.
In an increasingly inter-connected industry, manufacturers who fail to embrace a partnership mentality will find themselves increasingly marginalized. They’ll get elbowed to the sidelines by competitors that recognize the future of manufacturing is built on new partnerships, talent and ideas.
The future of manufacturing is ecosystem-driven. It’s time for manufacturers to start thinking about how to use existing partners in unique ways, introduce new partners with new capabilities, and apply new concepts to spruce up stale processes. Here’s how:
Old Partners in New Roles
- Try contracting your go-to partners for a variety of services outside the norm, such as product design or redesign services, product management, direct order shipment to customers and customer requested customizations or bundling.
- Utilize third- and fourth-party logistics providers for location flexibility, last-mile delivery for logistics and digital customer information services for status and tracking.
- Take advantage of postponement centers in order to customize or finalize products. They can be useful for packaging products late in the order cycle to meet specific customer requirements. For example, you can bundle consumer products around last-minute promotions.
New Players with New Capabilities
- Work with third-party product and manufacturing design services to strategically complement your own capabilities. Manufacturers can use them for faster innovation cycles than they can achieve in-house, or in a design capacity for products undergoing revisions.
- Bring in third-party labor. Third-party pools offer services from advisory to full operational control in manufacturing functions such as quality, engineering, safety, and maintenance.
New Concepts and New Directions
- Utilize maintenance, repair and operations (MRO) centers for common parts or assets within an industry or process type. For example, in the oil and gas industry, refineries in high-density U.S. production regions could share a common MRO parts center.
- Join the digital marketplace. Manufacturers are now able to buy digital representations of products through emerging digital marketplaces. Once designs are completed, products can be produced in-house, via a contract manufacturer, or through an ad-hoc 3D printing service.
Once manufacturers have identified the right partners and outlined the new roles they will play, they can then deploy emerging digital technologies to enhance collaboration and flexibility within the ecosystem.
For example, a manufacturing control tower can provide critical visibility across the network — from the manufacturer’s requirements to the production status at any contract manufacturer. Meanwhile, on the product side, engineering collaboration tools can entirely digitize product designs. This speeds design and prototyping, makes incorporating changes easier, and introduces the products into manufacturing more seamlessly.
Also helpful are advanced technologies, through which a manufacturer can create a digital representation — or a “digital twin” — of a physical asset. Using this twin, product designers, manufacturing engineers, and production operators across the ecosystem can simulate critical and complicated decisions prior to acting.
In the coming years, manufacturers across industries will undergo a steady evolution toward a new manufacturing model: one in which third parties, supported by digital technologies, assume increasingly greater responsibility for various facets of innovation, production and distribution. In some cases, manufacturers may own no facilities at all — or may never even touch the product itself. We already see evidence of this movement today, especially in the rapid development and short-product lifecycle of consumer electronics and computing segments. It’s here that companies have boldly embraced hybrid ecosystems in which they heavily leverage third parties.
It’s time for manufacturers in other industries to start planning for this future and begin creating the ecosystem they’ll need to dominate their markets. If they don’t, someone else will.
Russ Rasmus is the Global Practice Lead for Accenture Strategy's Manufacturing Practice.