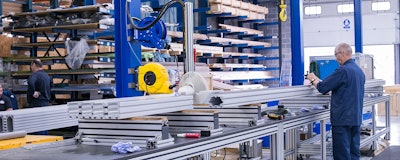
Human nature often drives people to resist change. That’s because adjusting requires facing the unknown, relinquishing some control, and moving out of comfort zones. But failing to change can mean that companies are stuck applying yesterday’s processes to today’s problems which is clearly not a winning strategy.
No matter the industry, change is inevitable. But manufacturers in particular are under pressure to adopt and implement new technologies that produce greater efficiency and productivity on the plant floor. CIOs and other leaders are especially feeling the stress to sell key stakeholders and employees on changes. McKinsey reported that 70 percent of all transformations fail, citing lack of employee engagement and inadequate management support as the top reasons. Yet, with worldwide spending on digital transformation technologies expected to grow 16.8 percent to $1.3 trillion in 2018, many companies are appraising implementation strategies. And if companies fail to consider how to manage the change before embarking on a project, they’re ignoring what could be their biggest obstacle.
Managing Change
There are various models for managing change, but the overarching principles all stress thorough planning and communication. As soon as you decide to implement a new technology, it is important to begin working on your plan.
At a high level, a holistic approach to change management has proven effective for manufacturers. This method looks beyond the immediate needs of the plant and addresses long-term strategic goals. The following change management tips can guide plant managers through the next technology implementation initiative.
Tip 1: Start With Why
Change for the sake of change is not strategic nor is it productive. Begin by asking some questions: Why change a process that already works? Why disturb a method for success that hasn’t encountered issues? Has a Manufacturing Change Request or Order been initiated on this issue?
Simply layering new technology over an old, ineffective process isn’t going to amount to increased value. To pinpoint where change is needed, take a broad look at the overall operations of the plant and determine where to cut costs and improve efficiency.
Moreover, each group of stakeholders has different reasons for why they need change. Engineers want an easier workflow, finance wants to keep costs low, and the IT team wants to spend less time fixing problems. Knowing why the change is needed can help determine how to effectively implement it.
Tip 2: Prepare To Manage Feelings
Keeping stakeholders in mind will also help leaders prepare for how each group will react to the change. As we know, the uncertainty and fear caused by shifting technologies often leads to reluctance and resistance. Connecting with employees most affected by the changes can help you identify which aspects might be met with the most opposition.
In particular, technologies that involve artificial intelligence (AI) and automation tend to create the belief that increased efficiency means a decreased workforce. For instance, employees might worry that a change could mean more work for them, as there may be unexpected glitches in the process they have to sort out. Being in touch with these people and their feelings helps leaders empower teams with information to understand the technology, making the change a more inclusive process.
Tip 3: Establish Clear Expectations
A Gallup poll found that only 33 percent of U.S. workers are engaged at work, due to poor communication and unclear expectations. Lack of employee engagement leads to lower productivity and lower profits for businesses overall.
Defining success for employees’ roles is not only important for employees’ day to day, but for the entire change management process. This means setting success metrics and establishing what change looks like for each role. Set meaningful milestones so employees know when to measure progress. And celebrate these milestones when they are reached so employees are encouraged to continue performing well. When employees see their peers praised, they are more motivated to continue that high level of performance and win the praise of their managers.
Tip 4: Prioritize Training... And More Training
Training is an essential part of a change management plan. For employees to feel comfortable with a new technology, it’s necessary to train them for proficiency it before it even goes live. And you should revisit training as the technology scales. These trainings uncover opportunities to troubleshoot problems and improve usage plans in ways that wouldn’t have necessarily been considered.
Aside from training, be sure to provide the right support tools so employees have ways to deal with issues as they occur.
Tip 5: Look Past The Finish Line
Change management is about achieving a long-term effect, so the process requires long-term effort. Follow up with all stakeholders involved and request feedback on how the change has fit into their routines. Solicit this feedback often and make adjustments as needed. Maintain a “change leadership” mindset—that is, continuing to communicate and refine the vision for transformation.
Change management requires strategic thinking and planning to ensure the greatest chance of success. Moving a sometimes reluctant workforce through a new technology implementation can prove challenging, but it can also be rewarding. Proactive planning and effective communication are key for ensuring your next technology initiative is successful at the employee level and achieves business goals.
Steve Smith is VP of Strategic Industries at ClickSoftware.