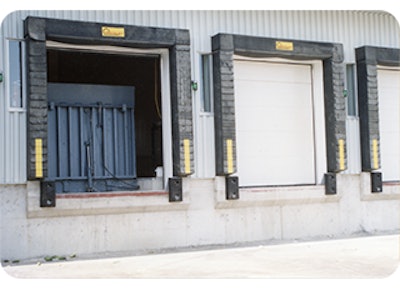
You do not want to lose production time due to an inefficient loading dock. You also cannot sacrifice safety for speed. Follow these loading dock safety tips to keep your dock safe and your products moving efficiently.
1. Keep your dock well maintained
A crumbling dock could give way at any time. The structure and the pit must be kept in good repair. Sections of the dock area with chunks of concrete missing will not provide the solid surface that lifts need to properly balance and place loads. If your dock includes a mechanical lift it must be serviced at the manufacturer’s established intervals. Dock boards must also be maintained and rated for the weight placed on them.
Check the loading dock door. It should hold firmly in place in a raised position. Having a dock door suddenly fall can cause extreme injuries to anyone in its path. Any overhead obstacles must be clearly marked. Pipes or wires over the loading areas present a hazard.
Maintaining your dock area also means keeping it clear of debris. Materials and packages that are not being loaded do not belong in the loading area. If a forklift or hand truck has to maneuver around obstacles, the work can become dangerous. Any spills must be cleaned up quickly as well. Oil or grease on the dock is a slip hazard for workers and vehicles.
2. Provide strong lighting
Bright lighting, both inside your dock area and outside, will reduce the potential for accidents. Truck drivers need to see where they are backing up. Lift operators must have full visibility of obstacles in the way. Lighting should clearly illuminate any danger areas and the edge of the loading dock. Do not solely depend on the lights on a vehicle to provide adequate illumination for workers.
3. Add bumpers, mirrors and chocks
Using bumpers at the end of docks and mirrors set appropriately will help drivers when they are backing up for loading or unloading. Even the most experienced driver will appreciate the extra assistance.
Chocks need to be available for drivers to use when parking the vehicle. However, drivers should also use a trailer lock to prevent any movement while the truck is parked. This is critical if the loading dock has any grade. A truck moving away from the dock during loading will create a bad situation.
4. Use a spotter for forklifts
A forklift operator cannot easily see the end of a loading dock, or where the truck meets the dock. Using a spotter allows the driver to know exactly where to direct the load. It will also eliminate the potential for driving the forklift off the dock if the truck is not fully backed in for loading. Spotters also act as guides by letting the operator know how high the load must be lifted to clear obstacles while avoiding overhead obstructions.
A well-trained assistant can improve the speed at a loading dock and ensure the safety of everyone involved in the process. Remember that spotters need to stand far enough away to not become trapped by the load if it falls.
5. Keep everyone clear while loading and unloading
Only the driver and a spotter should be anywhere near the load while it is being moved onto or off a truck. Dock operations are not a spectator sport. Both observers and a spotter face injury from distractions. Onlookers can become trapped between lifts and walls. When too many people are trying to help, the chances of someone having a hand or foot crushed during loading multiplies.
6. Lift operators must be trained and certified
Operating a forklift safely requires training and experience. This equipment is not designed to race through warehouses or turn corners at high speeds. Untrained operators can cause accidents by backing into other individuals and trapping them. Accidents also occur if operators are unable to steer correctly and knock over shelving or other avoidable objects.
Operators also need to know how to inspect loads before they begin to transport them. A damaged or unbalanced pallet and poorly wrapped boxes can fall once lifted. Extreme imbalances can cause a forklift to tip over.
Follow the safety requirements for operating forklifts and loading docks and your operations should be accident free. Many of OSHA’s regulations for loading dock safety can be found in Standards - 29 CFR 1910.176.
Author Bio:
Brad Poulter is the Executive Vice President of Operations at Best Transportation Services, Inc.. Best Transportation Services is a Chicago-based delivery company that provides courier solutions for the warehouse industry.