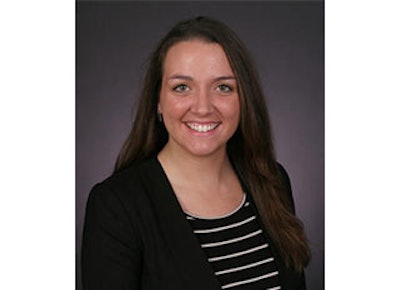
Manufacturing is a giant puzzle. The pieces are constantly moving, the regulations are constantly changing, and the challenges are constantly coming.
Every day, plant planners are expected to solve extremely complex puzzles — which operation will run on which line, how many of each part needs to be produced, how will each step happen at the right time — and they often lack the proper tools to do the job.
Quintiq is a company that was founded to help solve manufacturing, logistics, and workforce problems. The Quintiq supply chain planning and optimization software operates on a unique algorithm which was created under the vision and direction of CEO Victor Allis. “At the heart of what we do is single planning platform that allows us to solve real life planning puzzles for our customers,” he says.
Allis wanted to prove that their product was world-class, so they set out to break some world records. And they did – 98 world records to be exact.
The Flexible Job Shop Scheduling Project
As described by Quintiq, the Flexible Job Shop Scheduling Problem (FJSSP) is an extension of the classical Job Shop Scheduling Problem (JSSP). The JSSP is based on the assumption that only one machine is able to run a particular operation. The FJSSP, as its name suggests, assumes a more flexible setup. It reflects a production environment where it’s possible to run an operation on more than one machine. Though the specifications vary, the essence of the problem remains the same – you must assign all operations to machines in sequence (respecting the sequence of operations in each job) so that the total completion time (aka makespan) is minimized. Over the years, academics have published hundreds of iterations of this thought experiment.
“What academics have found many years ago is that these problems can get very complex very quickly because, for example, one of the machines may be a bottleneck, but all of them need to go through it,” explains Allis. Planners and academics started to make manual planning boards and Excel sheets to determine the optimal solution, but even with a small number of operations, the problem became too complex. So algorithms were created that took into account bottleneck theory, optimization techniques, and mathematical optimization to speed up the puzzle solving.
[Continue reading...]