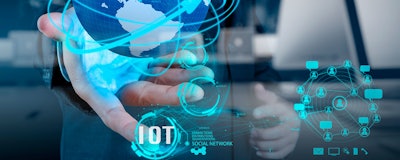
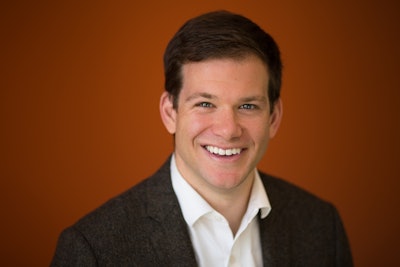
It is no longer a secret that adopting IoT technologies is critical to maintaining and optimizing industrial equipment and performance. We all know the benefits of using plant floor data to create valuable insights. The conversation is no longer why, but how. How do manufacturers begin the journey of connecting brownfield equipment to industrial IoT offerings? Plant managers and their teams should weigh all their options, do their homework and make sure they find the best fit for their needs now and in the future.
Connecting legacy assets
It’s always difficult to know where to start, but the process is easier for managers that understand the options available to them. When boiled down, there are really only three methods to consider for connecting legacy assets:
- Rip-and-replace,
- In-house solutions
- Best-of-breed, third-party solutions
As with everything, there are pros and cons to each option and managers should ensure they are not only capturing short-term ROI, but also setting up their organizations for success in the long run.
Anyone who has spent some portion of their career in manufacturing or IT is likely to roll their eyes when “rip-and-replace” is presented as an option. Of course, managers love the idea of starting fresh with all new and up-to-date equipment, but unless you’re involved in a greenfield project, this option is not realistic for most plant managers. Scrapping all existing legacy assets and buying new machinery comes with a hefty price tag. What’s more, the process of uninstalling and reinstalling is extremely lengthy—requiring downtime and lost revenue.
Option two, “in-house solutions” are infinitely customizable and can be created and executed according to business needs. However, once the implementation is complete or the engineer who created the system leaves, the internal team often runs into support and maintenance headaches that lead to significant lifecycle costs. Although this method may be attractive when considering up-front costs, it becomes increasingly problematic with troubleshooting, connectivity and upkeep as time goes on.
This one is “just right”
The final option, “best-of-breed, third-party solutions” has proved time and time again to be the most valuable. To start, installing best-of-breed solutions to connect legacy systems allows organizations to implement with little to no downtime and gain a return on investment almost instantly. Third-party solutions are customizable, and because they are competing to offer the latest and most valuable features, they generally offer the newest technology. If you choose the right companies, you will be working with the leaders of each solution component (e.g. connectivity, application development, analytics and so forth)—and you’ll also have access to their expert support throughout the life of the product.
Making everything connect in the real world
A notable example of a company implementing the third-party, best-of-breed method is a large paper product manufacturer. It worked with multiple IoT solution providers to collect valuable information from its machines.
First, the organization engaged with a sensor company that provided IoT-enabled sensors. These sensors were very easy to add to existing machines to begin streaming data—much easier than adding an I/O to a PLC or other gateway that they would need to program on their own. The sensor data was simply aggregated in a supported gateway via mesh networking, which then made the data available over MQTT.
Next, the company connected those sensors via a connectivity platform that supported MQTT, OPC UA and OPC DA in addition to a robust portfolio of device drivers. This enabled it to send the sensor data to traditional industrial automation applications (over OPC UA or DA) and to modern industrial IoT platforms (over MQTT). Working with a connectivity solution that supported a rich set of device drivers allowed the organization to easily integrate the new sensor data with data from PLCs and other systems already present on the plant floor.
Lastly, the organization selected a modern industrial IoT platform to augment the operational and asset intelligence capabilities of its existing systems. By utilizing a best-of-breed solution for sensors, connectivity and industrial IoT platform, the company was able to build an interoperable, customizable and well-supported system.
Setting up for success
Determining how to connect legacy equipment presents a challenge to plant managers. But, it is a challenge worth tackling: To leverage valuable integrated data, enhance functionality and ensure reliable performance down the road, you need to be connected. Manufacturers who don’t acknowledge the urgency of IoT-connected factories will fall behind those who do. Those manufacturers that choose a best-of-breed solution will be well positioned in the competitive global market.
Jeff Bates is a Product Manager at Kepware.