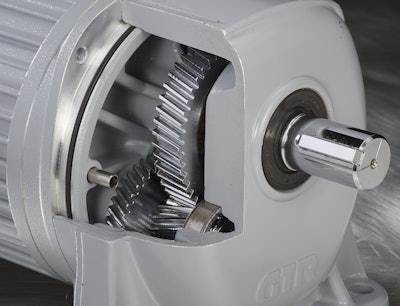
Of the myriad worries that fall under the scope of effective material handling management, determining how to improve operational efficiencies may not top the list. Its importance, however, should not be underestimated. One of the best ways to insure efficiency is to acquire the right combination of equipment to make your entire operation more productive, reliable and secure.
While selection of the best gearmotors for your operation may not seem an obvious place to start, it is, nonetheless, exceedingly important. Gearmotors designed for efficiency, installation flexibility and maintenance-free operation can help you achieve substantial cost-savings, avoid considerable downtime and boost productivity well beyond what initially seemed possible. This makes sense considering that each piece of heavily relied upon handling machinery — including packaging equipment, conveyors, dispensers and sorters — benefits greatly from a cost-effective, energy efficient motor or gearmotor which, over extended periods of time, lead to significant energy savings.
Features To Look For In A Gearmotor
There are many factors to consider when choosing the best gearmotor for your needs. Compatibility will revolve around whether its speed, torque and efficiency match the requirements of your particular application. Prior to purchase, you should evaluate the gearbox’s potential design limitations and thermal characteristics, full-load gearbox torque, gearbox input speed, gearbox yield strength and intermittent duty cycles. You may also want to look for quiet operation, speed and durability and consider additional premiums such as the use of top-grade grease and seals.
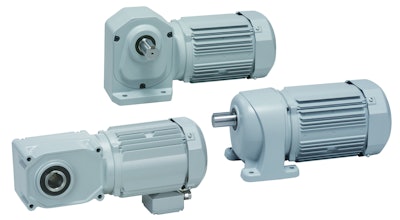
High-Performing Gearmotor Characteristics
High efficiency motors (IE3 or Nema Premium): High efficiency motors will positively impact downtime and enable you to quickly recoup your initial investment because, over time, less efficient gearmotors accrue tremendous costs. High efficiency motors will run cooler, leading to a longer life due to less mechanical stress on the system, and will keep windings in good shape because insulation won’t be exposed to unnecessarily high temperatures.
High efficiency motors also offer installation flexibility. AC (Alternating Current) motors are easy to use because they can be incorporated without an adjustable speed drive, which improves system efficiency by using only the current necessary to run the specific application. Additionally, AC Motors are fairly maintenance-free on most gearmotor applications. When it comes to safety, cooler running motors translate into lower risk of potential burns to employees working around the machines.
Energy Efficient Gearboxes: Unless a highly efficient gearbox is used, the efficiency of premium efficiency motors can be wasted. Although one of the main gear types used in material handling and conveyors is worm gearing, an oftentimes superior choice is hypoid gearing technology, which can maintain efficiency above 85 percent throughout the motor’s wide speed range. Typically, an inefficient worm gearmotor can be replaced with a hypoid gearmotor with smaller motor power and still produce the same amount of torque.
Worm gears also suffer from poor efficiency at reduced speeds — which are increasingly prevalent with the burgeoning popularity of variable frequency drives (VFDs). Worm gears can decrease in efficiency by as much as 10 percent based on the input RPMs. In contrast, hypoid gears actually increase in efficiency when reducing the input RPMs, making their use with VRDs more effective at transmitting power in low speed/high torque applications.
You’ll also want to maximize installation flexibility. Hollow bore gearboxes are often preferable, as they allow for direct machine mounting without using a chain and sprocket. This reduces maintenance since there is no chain to oil, and also helps reduce cleanup in washdown applications since it minimizes areas where dirt and bacteria can be harbored. Last but not least, hollow bore gearboxes improve safety because the lack of chain and sprockets in the units results in fewer potential pinch points for workers.
High-Grade Grease: Gearmotors that are filled with high-grade grease that lasts for the lifetime of the gearbox can greatly reduce downtime and maintenance costs. Grease-filled gearmotors also enhance installation flexibility as they do not typically require breathers, which means they can be mounted in any direction without designating a mounting position upon ordering.
Triple Lip Shaft Seals: Triple lip shaft seals can also help eliminate costly downtime, as they are preferable to dual lip seals for protection against lubricant loss and dust penetration into the gearbox. Keeping harmful dust out also prevents grease contamination, which often causes premature failures in bearings and seals. Additionally, keeping the lubricant sealed inside the gearbox helps avoid maintenance by prolonging the life of gears, seals and bearings. Safety also improves, since there is less chance for lubricant to spill from the gearbox, which can be a potential slippage risk for employees working near the machinery.
O-ring Sealing: Compared to gaskets, O-rings help lower maintenance costs by providing a better seal, which helps prevent lubricant leakage from the gearbox case. O-rings also have a longer life than gaskets, since they are usually placed on an internal connection between the gearbox case and cover and are therefore not exposed to the elements. Gaskets are typically at least somewhat exposed to outer elements.
Juan Avalos-Vasquez is an Applications Engineer for Brother Gearmotors, which offers a range of sub-fractional AC gearmotors and reducers in demanding industries such as food & beverage, packaging and material handling.