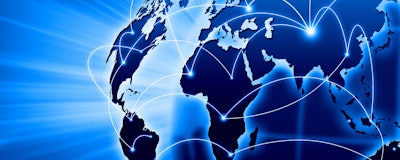
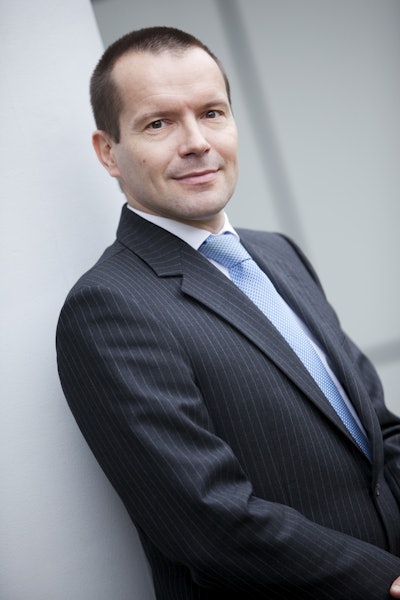
Many businesses suffer from a significant disconnect between strategy and operations: Ineffective communication between the executive suite and the shop floor. When asked what constitutes a good decision, those responsible for execution typically apply criteria far removed from the business goals or key performance indicators defined during the long-term planning process. In other words, the decisions made about your business in the moment β when many of the most critical decisions have to be made β may not drive your business in the direction you intended. Those which do, perhaps only by chance.
As the pace of change increases, the lines between strategy and execution blur. Supply chains and the decisions that build them are now driven by big data β a real-time stream of structured and unstructured data. Organizations are gathering data that could enable them to make far better decisions. But data alone wonβt generate profits. Itβs what you do with it that counts.
Mobile technology can provide that connection, putting business-goal-oriented intelligence into the hands of your entire workforce. Here are three ways in which mobile technology, connected in real time to powerful centralized optimization and analytics software, can empower your decision makers, whether they be sales people, CEOs, warehouse managers or VPs, to make better business decisions.
No. 1 - Intelligence
The most effective way to mitigate the risk of supply chain disruptions is to share data and strengthen relationships first between departments and then with partners and suppliers. But whatβs often missing from mobile-tech shopping lists is the one item that makes effective collaboration possible: The overarching technology that integrates the planning of all processes, equipment and personnel. This central intelligence is what I call the Self-Learning Supply Chain.
Ultimately, the Self-Learning Supply Chainβs reason for being is to answer one question: Given everything thatβs happening along the supply chain, which decisions will support the organizational goals of maximizing customer satisfaction and minimizing operational cost? In order to do so, it combines its insight into all the consequences of hundreds of disturbances with its knowledge of the KPIs that need to be optimized such as waiting times, turnaround times, operational cost, etc., with real-time data about personnel, equipment, relevant regulations and business rules.
Imagine a logistics network where data streams in in real time via various mobile applications and connected devices. The Self-Learning Supply Chain calculates the effect of disturbances throughout the network, alerting planners to their consequences and offering suggestions on how to deal with them. It might determine that unusual traffic patterns will result in late or missed deliveries, and then suggest how best to reduce the impact of the delays. Any changes in the plan will be immediately communicated to the affected parties via their mobile devices. That might include the customer service manager who has to inform a customer of a delay, or a driver who has to adjust her route to do an additional pickup.
An interesting application of this technology can be seen in some of the worldβs busiest airports. Just like a supply chain, an airport is made up of complex, interconnected systems. Interdependencies mean that a relatively small disturbance, such as a 30-minute flight delay, can have a large knock-on effect. The reality is that there is never just one small delay. There are many disturbances throughout the day and night, and each of them ripples through the system to create waves of chaos: Peaks and troughs that are difficult to predict and plan for.
Only intelligent technology can cope with complexity on this scale at this pace. And only mobile apps in the hands of decision makers can put that intelligence to use across the many discrete parts of an airport. It can give planners full visibility into all the consequences of any disturbance as it happens. The central intelligence is constantly calculating all those ripple effects, alerting planners to their consequences and offering suggestions on how to deal with them. It might calculate that in 30 to 40 minutes, disturbances in various parts of the airport will result in bottlenecks at immigration, and suggest how best to respond.
Weβre not talking about a situation where an all-knowing black box spits out decisions. Instead, itβs an intelligent planning and optimization platform where planners and decision makers interact with each other and the system via mobile and desktop applications to respond flexibly and intelligently to new developments.
No. 2 - Analysis
The standard workplace application of mobile technology delivers limited visibility of whatβs happening in the present. This information can be helpful, but it certainly isnβt enough. Whatβs needed is insight: Hereβs why this is happening (diagnostic analytics), hereβs what might happen next (predictive analytics), and hereβs what you need to do to limit its impact on the supply chain (prescriptive analytics). And even, hereβs what will happen if you do that (what-if analysis).
When role-specific mobile applications are integrated with an intelligent centralized planning and optimization platform, the power of optimal decisions is extended to a wider group of users than ever before. When these mobile applications are connected to the supply chain in real time, even the remotest of workers has access to up-to-the-minute insights and decision support. At their best, they provide two-way insights in real time. Differences between plans and current data values can be assessed and acted upon. Issues can be flagged to planners, who can then address them before they have a negative impact on customer service.
Imagine that your production manager is off site when a critical piece of machinery in the line breaks down. Heβll receive an instant alert, allowing him to intervene to prevent an important order from being delivered late. He can use the system to do a what-if analysis in order to plan the best response. And he can also ask the system for recommendations on how to respond. Once your production manager has made a decision that satisfies your business objectives, as measured by the system, he can quickly reoptimize the plan to minimize the impact on other orders and communicate the revised plan to everyone involved in executing it.
No. 3 - Responsiveness
Itβs critical that your technology has the intelligence and speed to cope with rapid change. One seemingly small decision can have a ripple effect along the entire chain. Change one piece of data and all other dependent variables must automatically be recalculated to accommodate that change. This then leads to subsequent calculations and deductions in real time in response to events and planning decisions. This goes far beyond the speed and capacity of a human planner.
I recently worked with a well-known public transport provider, Transport for London, which you may know as the London Underground. The London Underground has a workforce as large and complex as its network of trains and buses. Our role was to implement mobile technology that would not only to increase efficiency and productivity rates, but also boost customer satisfaction. The system would alert planners to unusual patterns in the network, signaling an expected surge in demand or a disruption. The plan is optimized in real time, workers are reassigned as needed and critical updates about routes, requirements or new jobs are relayed directly to the workersβ mobile devices. Workers are then far more likely to respond in time, fully prepared and equipped for their tasks; the impact of disruptions on customers is reduced. Workers can also use mobile devices to access online resources, support manuals, and even real-time virtual assistance for problems they encounter on-site. Ramping up response speeds in this way has a direct positive impact on customer service and productivity.
Good Decisions Canβt Wait
When your decision makers are presented with new information at the moment of execution β whether thatβs a potential deal or a disruption β do they know how best to respond? Under pressure to make rapid decisions, facing an overwhelming volume of data, they have no choice but to rely on instinct and rules of thumb. There is simply no way to assess the merits of all the options and outcomes in time. But snap decisions arenβt always good decisions, because the most profitable choice often isnβt the most obvious. You can empower everyone in your organization to make the right decisions by giving them access to insights into the past, present and future, and the ability to re-plan and re-optimize as needed. The key word is insight, rather than information. And those insights must be available in real time to be of real use. Only by putting it in the hands of the workforce β the new decision makers β all along the supply chain, will mobile technology truly transform the supply chain.
Rob van Egmond is CEO of Quintiq.