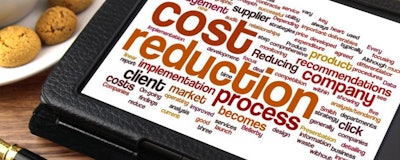
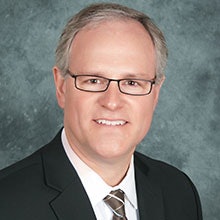
Manufacturers around the world have become increasingly aware of the impact of inefficient equipment on their facilities’ energy costs and, ultimately, their overall bottom line. For many plant maintenance managers, their first cost-cutting instinct is to focus on boosting the efficiency of their electric motors. However, compressed air systems represent roughly one-tenth of the total energy a manufacturing plant consumes. In fact, the operation of compressed air systems adds up to one-and-a-half billion dollars a year in energy costs, just in the United States. Inefficient compressed air systems waste far too much of that amount.For plant managers in existing facilities, the prospect of tearing out an aging, inefficient compressed air system and replacing it with a new one, while nice to dream about, is usually impractical from both facility downtime and capital expenditure perspectives. However, they can pursue several strategies for improving compressed air system efficiency without resorting to an overall system replacement.
1: Select the right component sizes
Oversized valves waste energy and the limited real estate in machine and system designs. Choosing valves with solenoid air pilot and low watt coil designs can also reduce electrical costs. Wherever possible, use straight fittings instead of 45° or 90° elbow fittings to minimize pressure drops. When system components require replacement, make sure the maintenance team understands how important strict adherence to the practice of applying thread sealant is in preventing air leaks and discouraging the intrusion of contaminants like oil, water, dirt, rust, etc.
2: Choose more serviceable actuators.
Actuators designed to allow for repair last longer, leak less and reduce long-term maintenance costs over non-repairable ones. Typically, cylinders can be sized at 60 pounds/square inch gauge (psig) to provide a safety margin. Reverse flow regulators, which are piped between the valve and the cylinder, provide independent pressure control for extend and retract. These regulators’ non-relieving design saves air and reduces wear on components and mechanical devices.
3: Install an air preparation system.
Clogged filters reduce airflow, increasing both air and maintenance costs. Visual and electrical sensors detect pressure drops as filters clog. The use of drip leg assemblies that protect equipment from water and contamination, both primary and coalescing filters, and pressure drop sensors and indicators should be part of any maintenance program. The use of a “smart” air preparation system can help ensure sufficient airflow by servicing filtration and pressure controls. These systems are often a good choice for facilities without proactive maintenance programs or resources.
4: Select the right pressure.
High-pressure air should only be specified where it’s essential. Reducing pressure when possible provides huge air costs and maintenance savings and improves the performance of most compressed air systems. Rather than running actuators at 80 psig (pounds per square inch gage) extend and retract, why not operate them at 60 psig extend and 40 psig retract instead? Those lower pressures will still get the job done but make it possible to save several thousand dollars per actuator per year.
5: Try vacuuming less.
All too often, systems apply pressures up to 100 psig for vacuum cups that only require 70 psig. Fixing this offers a prime savings opportunity. Look for air economizing/emergency stop vacuum solutions that allow turning the vacuum off when parts aren’t present, which enhances safety and reduces noise in the workplace.
6: Stop leaks sooner.
Fluctuating system pressure due to leaks makes equipment function less effectively and decreases its service life due to extra cycling and run time. In many plants, as much as 30 percent of a compressor's output ends up leaking away through loose or faulty couplings, joints, quick disconnects, hoses or tubes, fittings, filter/regulator/lubricators (FRLs), and valves. An ultrasonic acoustic detector can help track down these leaks.
7: Re-evaluate your compressors.
Regular system audits and corresponding adjustments often lead to reduced demand, which can, in turn, reduce compressor run times. Although such audits require some upfront expenditures, they easily pay for themselves through lower operating costs, greater efficiency, and improved quality.
Bill Service, Parker Hannifin Pneumatics Division