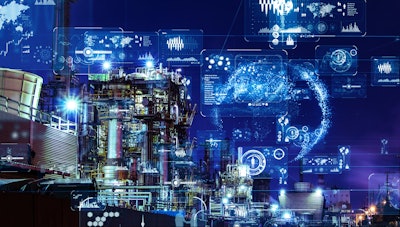
In August 2023, Briggs of Burton, a mid-sized equipment manufacturer whose U.K. roots date back to before the American Revolution, officially opened a U.S. office in Louisville, KY to support a growing customer base of spirit producers in the heart of America’s Bourbon country.
Briggs, which makes hygienic equipment for beverage, food and pharmaceutical companies, also has been aggressively cultivating new customers in North America, China, Europe and elsewhere as part of an ambitious — and to this point, highly successful — international growth strategy that has resulted in the company doubling its revenue in the last two years.
The key to unlocking that growth and enabling a company that was once little-known outside its home country to build a global footprint and reputation? A modernized digital backbone.
Briggs realized it couldn’t fulfill its ambitions without first overhauling its digital infrastructure and moving most of its business systems to the cloud. That overhaul has been instrumental in turning the company into an operationally streamlined, data-intelligent juggernaut.
Its systems are highly automated. Data-derived insights from embedded AI and machine learning are supporting timelier, better decision-making and planning. And as a result, the company has hit its growth targets sooner than expected.
Companies like Briggs are proving that what an industrial manufacturer may lack in brand recognition and deep pockets, it can make up for with more intelligent, agile strategic decision-making, faster development cycles, closer customer relationships and more efficient operations. Opportunities to cultivate new markets, diversify revenue streams and capture new operational efficiencies are abundant for mid-market manufacturers.
Capitalizing on them starts with modernizing the digital backbone, with a focus on these four areas:
1. Connecting Disparate Systems in the Cloud
The lack of a single, integrated digital system of record can be highly problematic for a manufacturer, as relying on a patchwork of legacy software and spreadsheets can cause widespread inefficiencies. By unifying those systems in the cloud, companies can gain much-needed visibility into critical aspects of their business so they can capture new efficiencies on the shop floor, across the supply chains, and in how they manage resources across the organization.
A move to the cloud enabled German wind turbine company ENERCON to simplify a complex IT environment with close to 60 systems into a single environment across 145 subsidiaries in 32 countries. Among the benefits of that shift: a 75 percent reduction in month-end closing time with resource-related intercompany billing. Similarly, Komax Group, a Swiss wiring system manufacturer that relies on a sprawling network of subsidiaries and partners across 60 countries to support its customers, simplified its complex legacy IT landscape into a single environment. The resulting efficiencies have positioned the company to keep growing organically and via additional acquisitions.
Efficiency gains like these are particularly important for companies in acquisition mode, and for midmarket manufacturers with private equity investors, for whom reducing operational costs is often a high priority.
Housing digital infrastructure in the cloud also positions companies to easily scale that infrastructure to the needs of the business. With software-as-a-service, a growing company won’t necessarily require a major capital outlay to expand digital infrastructure.
2. Visibility Means Better Decision-Making, Planning
Production at a new plant in Germany developed by automotive component manufacturer Smart Press Shop, a joint venture between Porsche and Schuler, is digitized end to end using a cloud-based infrastructure. The result is fully paperless production powered by automated processes that enable the company to configure production line machinery to cost-effectively press automotive body parts for small-batch orders.
Along the way, the company has unfettered visibility into the entire production process. In real time, it knows exactly where a given material is and where it will be used so it can make any necessary adjustments to a specific machine based on the quality of a specific batch. It also knows which order is processing, and it can optimize order sequence to improve plant efficiency.
With AI- and machine learning-powered tools, data from the manufacturing operation and across the organization, as well as the supply chain, can be analyzed in real time to make better-informed decisions. With insight into operational, financial and sustainability-related data and KPIs, decision-makers can better understand the interplay and tradeoffs involved in different decisions, such as their sourcing or resource deployment. This level of understanding also makes for more accurate and flexible planning and forecasting, bolstering a company’s ability to adjust on the fly to changing market conditions and shifting priorities to avoid supply bottlenecks.
3. Relieve Talent Pressures
Quality IT talent doesn’t come easily or cheaply these days. By relying on standardized, cloud-based business systems and processes embedded with intelligent automation, companies can operate without depending as much on specialized, expensive IT talent.
Using that approach, Smart Press Shop has minimized the need for in-house IT resources. There’s no IT hardware at the manufacturing site, simplifying maintenance and operation. What’s more, it can configure the production line for new products quickly, without manual intervention. This enables it to produce small batches of components much more efficiently than a traditional production plant can.
4. Rapid Development and Deployment
Nowadays, more mid-market manufacturers are exploring service-based business models that bundle a product with different services, such as packaging a piece of factory equipment with benchmarking performance services and predictive maintenance. With a digital backbone that can support the unique sales, service and billing processes associated with many of these offerings, midmarket manufacturers stand a better chance of making them sustainably profitable. And that, ultimately, is how they are going to stay a step ahead of their larger, deeper-pocketed competition.