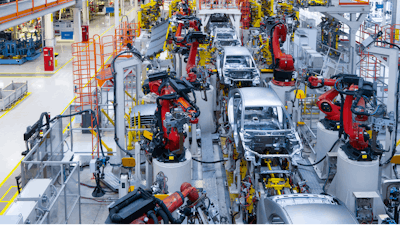
While overall sales for automobiles took a big hit in 2020, the electric vehicle (EV) has proven to be a silver lining—increasing in market share from 2.5 percent in March 2020 to four percent by the end of the year. The crisis also represents major strides in the automotive supply chain, most notably: the pandemic’s impact has expedited the utilization of technology for automation and supply chain communication.
Unfortunately, COVID-19 also revealed that many organizations were unprepared for such a crisis. When the lockdowns occurred, many executives in the automotive industry found themselves without the ability to repair on-premise systems and processes. Organizations with hefty requirements for support and error correction spent too much time firefighting and remaining reactive.
In contrast, organizations that reinvested and re-evaluated their systems to prepare for such a disruption, faired far better than their counterparts that did not. With the exponential amount of data being exchanged today, these organizations chose to improve their infrastructure and transition from outdated practices, such as FTP, functioning at nearly dial-up speeds.
Manual processes opened the door for many errors, supply deviations, and failures. Since there was no access to on-premise systems or in-person coordination between employees, significant gaps in the supply chain process were exposed.
The traditional process of manual uploading of Advanced Shipping Notices (ASN)s and invoices showed just how much the automotive industry hinged on complex and inefficient data analysis. Outdated manual invoice processes cause payment delays and have highlighted stark inefficiencies, such as restricted cash flow. Furthermore, there are many organizations with zero visibility and a lack of access to reports and KPIs. It had become glaringly obvious how poorly processes had been adopted (i.e., no supply chain synchronization).
When ASNs and invoices are processed in a cloud-based platform with full visibility across the lifecycle of each transaction, constituents across the organization are notified of potential errors and can quickly and easily rectify the issue with minimal manual intervention.
It is vital to implement the correct processes as early as possible. An integrated supply chain solution enables a more seamless operation at the earliest point of the design. In this scenario, a customer has full visibility into incoming shipments and the supplier knows exactly which and when items are received. Supply chain exception management tools enable the supplier to respond to anomalies across the supply chain transactional process.
By relying on advancements in integration adapters and cloud technology, the supplier’s core systems can communicate to any system across its network and trading partner community. This integration also provides the purchaser with visibility into knowing exactly when their vehicle is coming. All these processes are consolidated to improve the financial cycle.
Moving forward with an automated and integrated automotive supply chain is not just about prototyping and manufacturing a vehicle. It is about demonstrating the robustness of the supply chain. The entire digital supply chain goes through the same volume ramp-up as the production line that streamlines the digital transformation from the first engagement with the trading community.
For example, it’s an opportunity for the EV vehicle sector to fix the legacy supply chain issues of the traditional automotive supply chain process. With the sector bringing in a large percentage of new suppliers (technology providers that have never worked in the automotive industry), they have an opportunity to create a “right the first time” supply chain process that provides a two-way stream of traceability and inventory management – ensuring that the OEM has maximum visibility of their incoming supplier demand as well as clear traceability of supplier products from the point of receipt.
There are several key issues in the traditional automotive sector where suppliers are struggling to match parts delivered with parts invoiced. The inconsistency is directly linked to a lack of visibility of the supplier part journey from the moment it leaves a supplier’s facility through to the point the part becomes owned by the OEM. This process leans heavily in favor of the OEM where any losses associated with inventory discrepancies are financially covered by the supplier.
Using integrated systems and a wider adoption of RFID would allow suppliers to accurately monitor, manage and account for their parts and result in a more accurate and timelier invoice. Allowing greater visibility of a specific component’s journey through the production line will also allow suppliers to react more quickly and more effectively to any inventory deviations caused by quality failures, damage and or loss – thereby reducing production delays at the OEM.
With so many new suppliers entering the EV sector, now is the time to introduce suppliers to cloud-based approaches and integrated supply chain management at the start of product/vehicle development rather than the end of the design phase.
Creating an integrated supply chain process at the earliest point of a supplier’s engagement with an OEM allows the supplier and OEM to prove out their supply chain management and production capabilities, resulting in a greater success rate when a new vehicle program moves from concept/design to mass production. The automotive supply chain — like almost everything else — has little choice but to turn to the cloud to improve efficiencies.
Thuy Mai is CEO of Texas-based DiCentral.