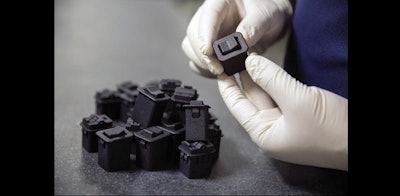
Multi Jet Fusion is the latest 3D printing process to hit the market with promises of taking 3D printing into production. The technology has gained attention for reducing manufacturing cycle time and material costs, and early adopters have had success, indicating a larger industry impact. But just like any other manufacturing process, Multi Jet Fusion has nuances that can only be discovered through working with the technology over an extended period of time and through a variety of projects and applications.
Stratasys Direct Manufacturing conducted a four-month study to see how Multi Jet Fusion would stack up in a production environment compared to powder bed fusion processes. This article will cover the results and insights from that study, including process controls and design considerations to ensure repeatability, cost effectiveness and quality of Multi Jet Fusion parts.
First, it’s important to have a general understanding of how the Multi Jet Fusion process works.
Multi Jet Fusion process overview
The process begins with a thin layer of powdered material being applied across the print area. The material is preheated before printing to provide consistent and accurate temperature control of each layer. The machine jets droplets of fusing, detailing and transforming agents along with thermal energy on top of the powdered material to define the part’s geometry and properties. Fusing agents absorb thermal energy and cause the powdered material to melt (or fuse) creating the current layer of parts. Detailing agent reflects heat, stopping the fusing which allows for printing features at the correct size. Transforming agents are combined with the fusing agent to add part properties like color. At the end of the jetting and fusing step, supply bins refill the material carriage with fresh material. Then, like other 3D printing processes, the print platform retracts and material application begins again. The process continues layer-by-layer until a complete set of parts are formed. After the print is finished, the build unit with the material and parts are rolled onto a processing station for cooling and un-fused powder excavation. Leftover powder is recycled for use in future print batches.
The fusing, detailing and transforming agents unique to the Multi Jet Fusion process are key to realizing its benefits, but they can also introduce variability and some design limitations, as Stratasys Direct Manufacturing discovered in its study.
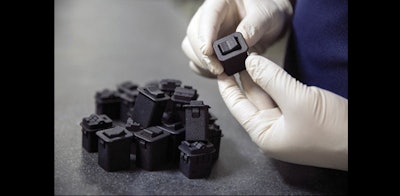
Multi Jet Fusion process evaluation
Stratasys Direct’s Multi Jet Fusion study aimed to 1) test and validate Multi Jet Fusion technology; 2) confirm performance capabilities within a production environment; 3) compare it to a similar, familiar process (laser sintering); and 4) ensure part quality and repeatability.
The team tested 86 total batches, using a variety of test specimens, including tensile bars, fine feature coupons, macro dimension coupons, density cubes and in-process warp bars. They also tested all specimens with the three Multi Jet Fusion print modes: fast, balanced and mechanical. The print modes affect the outputs. “Fast” is made for speed and making models that don’t require the strongest mechanical properties. “Mechanical” is for manufacturing functional parts with high requirements. And “Balanced” is right in the middle, balancing speed with mechanical properties.
The team concluded that Multi Jet Fusion is a viable solution for production applications with the right process controls and print parameters. The technology presents some challenges in nesting parts due to the active cooling effect of the detailing agent. Also, if irradiance is not properly adjusted before the print, an effect that makes the exterior of the part look like elephant skin can become an issue. Moreover, capillarity action on the top surface of parts also needs to be accounted for in the print set up. Lastly, they learned that Multi Jet Fusion is a viable competitor to laser sintering for production applications at higher volumes because:
- Although not as isotropic as claimed, Multi Jet Fusion has significantly higher isotropy than laser sintering.
- Nylon 12 PA has better properties with Multi Jet Fusion than when used with laser sintering, especially in terms of UTS and elongation.
- Dimensional accuracy with Multi Jet Fusion is somewhat more predictable.
- The production speed of Multi Jet Fusion affords much more throughput (especially for smaller parts).
- Multi Jet Fusion provides better aesthetics, allowing for more visually appealing parts and features right out of the machine.
The testing process also helped Stratasys Direct Manufacturing understand the necessary quality systems and material handling procedures, as well as verify mechanical properties and dimensional performance criteria to ensure repeatability and consistency.
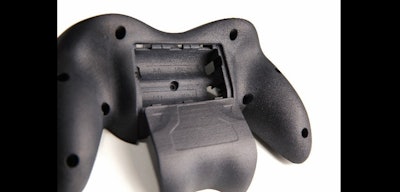
Design specifications
Properly designing for the Multi Jet Fusion process ensures parts will meet specifications. In many ways Multi Jet Fusion is similar to designing for powder bed fusion processes; however, it is unique in the following ways:
0.02” fine feature resolution and thickness – With a jetting resolution of 1,200 dpi, smaller will print but may not get enough thermal energy to be fully dense or meet material property specifications.
125 – 250 micro-inches RA surface finish – This is the average surface finish of Multi Jet Fusion parts as printed. Secondary processes, like tumbling can be added for a smoother finish.
14.96” x 11.25” x14.96” max part size – This is the maximum part size Stratasys Direct recommends in order to add a buffer around parts for the printing agents. This also allows room for shrink compensation and orienting parts at an angle to eliminate capillary and other detrimental effects.
Tolerances of ± 0.010 inches (0.25 mm) or ± 0.001 inch/inch (0.025 mm/25.4 mm), whichever is greater – Stratasys Direct has achieved higher tolerances, but the possibility depends on the overall dimensions and design.
Will there be a day when 3D printers line the production floor? Yes – granted improvements can be made to economics, quality, breadth of materials available and more but one thing is for sure – technologies, like Multi Jet Fusion, are enhancing manufacturing operations today with speed, flexibility and efficiency in a way that 3D printing never has before.
Chuck Alexander is director of product management at Stratasys Direct Manufacturing. He has been a key influencer in the 3D printing industry for 30 years.