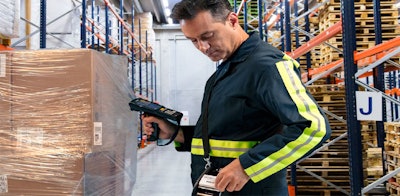
4 TIPS TO STAY COMPETITIVE
IN MANUFACTURING
www.vantageid.com
2Vantage ID • 866-234-8468 • [email protected] • www.vantageid.com
In today’s rapidly evolving manufacturing landscape, many companies
are turning to technology to gain a competitive advantage. Smart
manufacturers are leveraging technology to increase efficiency, reduce/
mitigate human error, and optimize their supply chain in order to increase
their profitability. Manufacturing in the future will require investing in
technology in order to be more connected and provide more visibility for
all stakeholders, both internally and across the supply chain.
This e-book highlights four technologies many manufacturers are utilizing
right now to future-proof their business. Four must-have technologies for
improved efficiency and operational visibility are:
FOUR
CRITICAL
TECHNOLOGIES
BARCODE SCANNING
Even some of the largest, most technically advanced companies are still
using archaic manual processes in key cost areas. If your company is still
on pen and paper, you are not alone.
Inventory accuracy errors can lead to over/under-purchasing, incorrect
orders, costly chargebacks, and lost business. As order complexity
increases in the era of e-commerce (larger volumes of smaller orders),
manual or paper-based workflows won’t be able to keep up. Fortunately,
3Vantage ID • 866-234-8468 • [email protected] • www.vantageid.com
there’s a proven solution for inventory errors that is both reliable and relatively inexpensive – barcode
labeling and scanning.
To remain competitive, small and medium-sized businesses (SMBs) must move from manual
processes using paper checklists and Excel spreadsheets to software solutions designed to
automate their facility. Barcoding is an important foundation on which manufacturers can build
multiple automated processes and workflows that can improve efficiency and operational visibility
across every facet of the organization.
A basic barcode system includes barcode printers, correct label stock for the products and
environment, barcode labeling and design software, inventory management/warehouse management
software, barcode scanners, and (in most cases) a wireless LAN. In addition, these solutions require
a facility layout plan for implementation.
Barcode scanning eliminates manual data entry and helps reduce human error—employees don’t
have to write down or type in ID numbers or product information as they move inventory. This
improves accuracy as well as productivity.
Barcodes also enable companies to monitor and track both inventory and assets. By integrating
barcode scanning into regular inventory and asset management processes, companies can achieve
a near real-time view of these items as they move through the facility or across the supply chain.
In addition, barcode makes it easier to stay in compliance with vendor partner shipment
requirements and industry regulations.
4Vantage ID • 866-234-8468 • [email protected] • www.vantageid.com
The modern worker is mobile, whether they are inside a facility or based in the field. In the
manufacturing plant or warehouse, employees are constantly moving through the facility on a regular
basis to complete tasks that keep operations humming. Smart manufacturers are turning to mobility
solutions to empower workers to be more efficient at the point of activity.
With rugged mobile computers and integrated barcode scanning, employees can automate
receiving and putaway processes—they will know immediately if they’ve put the right goods in the
right place, and can access information from enterprise applications directly on their mobile devices.
These same devices help streamline picking and shipping operations by eliminating paper pick/ship
forms and providing real-time confirmation that the order is correct.
Using a mix of vehicle- or forklift-mounted computers, mobile computers or tablets, and wearable
scanners, manufacturers can provide direct access to inventory and other enterprise information to
employees on the warehouse floor, and enable them to make inventory moves, initiate orders, and
perform other value-added tasks anywhere in the facility.
For more advanced applications, mobile/wireless carts can provide access to industrial-grade
barcode printers, desktop computers, and other technology. This reduces the need to walk back
and forth on the warehouse or shop floor, (which can save hours per day for each employee),
and improves labeling accuracy by providing on-demand labels at the point of use. These mobile
solutions not only improve efficiency, but also boost morale and improve employee safety.
MOBILITY
5Vantage ID • 866-234-8468 • [email protected] • www.vantageid.com
Radio frequency identification (RFID) tags are the next generation of automatic identification,
providing a way to further automate processes as tagged goods and assets can report their own
status or location via fixed-position readers. Some manufacturers are utilizing RFID technology to
track inventory and assets for applications where:
For companies with existing but outdated mobile solutions in place, there has never been a better
time to upgrade to new technology. Microsoft is sunsetting support for its legacy mobile platforms,
and a new generation of employees is entering the workforce, with years of experience using
advanced touchscreen technology on their personal phones and devices.
Rugged computer manufacturers are migrating users to Android-based devices with consumer-style
touchscreens. By moving away from old green screen terminal emulation solutions, manufacturers
can make employee training easier (workers are already familiar with the interface), streamline the
hiring process, and make their company more attractive to younger workers. This is especially
important for seasonal operations that require hiring large numbers of short-term employees during
peak periods—these new hires can be up and running on mobile devices much more quickly.
RFID
• Labor can be reduced and inventory can be more accurate if no line of sight is needed.
• Each asset needs to be individually identified.
• They are interested in mitigating human error in the scanning process.
Many companies are seeing significant cost benefits of passive scanning in the warehouse,
especially as it can further simplify training new employees. Common applications for RFID in
manufacturing include:
Inventory management: Tagging work-in-process components and finished products with
RFID tags provides real-time visibility into manufacturing operations. With strategically placed
RFID readers, companies can keep close track of production progress, identify bottlenecks,
and even automate inventory replenishment processes as parts are consumed. Customers can
even receive real-time updates and alerts based on manufacturing status.
6Vantage ID • 866-234-8468 • [email protected] • www.vantageid.com
Monitoring shrinkage/reorder levels: With a real-time view of where inventory is at all times,
companies can reduce product loss because they can see exactly when items have left the
facility. Inventory accuracy also makes it easier to set automatic replenishment orders as
inventory is consumed. In turn, this enables a just-in-time inventory approach that can reduce
overall inventory carrying costs.
Asset management: RFID helps move manufacturers into the era of the internet of things
(IoT) by connecting existing tools, equipment, machines and other assets to the network. This
makes it easier to locate lost assets, monitor equipment usage, and (when combined with
sensors and other technology), identify equipment that requires maintenance or repair. RFID
helps manufacturers take a more proactive approach to asset management and maintenance
that can help save money and avoid costly downtime.
Implementing mobility and barcode technology requires more than just hardware. Manufacturers
also need the right labeling and printing supplies to ensure the success of the deployment. Using
substandard label supplies or consumables that aren’t designed for the environment (indoor vs.
outdoor, freezer environments, exposure to chemicals) can lead to critical label failures.
There are several costly consequences for not selecting the right supplies to the application or
environment. First, low-cost supplies can jam the printers, leading to unnecessary downtime, while
also reducing the life expectancy of the printer. Further, the wrong supplies can lead to higher
levels of waste or scrap, which increases costs. Finally, if the label supplies are not designed to
withstand your operating environment, they may become damaged, faded or even fall off, which
will undermine the effectiveness of the real-time tracking initiative.
SUPPLIES
ABOUT ZEBRA TECHNOLOGIES
With the unparalleled visibility Zebra provides, enterprises become as smart and connected as the world we live in. Real-time
information – gleaned from visionary solutions including hardware, software and services – gives organizations the competitive
edge they need to simplify operations, know more about their businesses and customers, and empower their mobile workers to
succeed in today’s data-centric world. For more information, visit www.zebra.com.
CONCLUSION
Not only is buying the right technology important, but who you buy it from is even more critical. Select
a value-added reseller (VAR) partner who is not only adept at identifying pain points, challenges and
bottlenecks in your operation, but can also deliver workflow solutions to streamline your supply chain.
This is especially critical for small and medium-sized businesses that are moving from manual operations
to automated processes.
With the right mix of mobility, automatic identification technology and supplies, combined with the
consulting expertise of a trusted VAR, manufacturers can meet the needs of today’s demanding
e-commerce environment while preparing for future demands and challenges.
ABOUT VANTAGE ID
VantageID provides the level of expertise and the technology components required to make the transition to this new level of
automation and visibility: custom data collection projects, knowledge of the entire labeling process including software, printing
hardware, consumables to last the life of the label, and scanning software/hardware. We integrate every component for
maximum success.
Vantage is also an Advanced Supplies Specialist, and our team has the skill set needed to create the right combination of
consumables, hardware and software to get the best results—particularly in harsh environments where labels are exposed to
temperature extremes, moisture, abrasion, and conditions.
With Vantage ID, you don’t just buy a box, you get a true consultative approach that understands manufacturing, warehouse
operations, and distribution center needs. Ready to get started? Let’s talk.