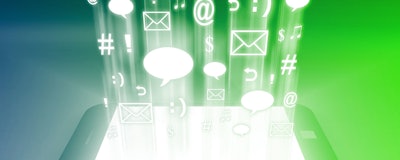
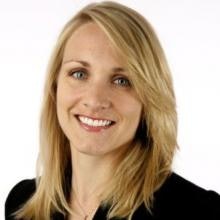
For manufacturers, finance and accounting processes are viewed as the cost of doing business. While there is a high priority to automate other areas of operation on the manufacturing floor, critical internal processes such as accounts payable (AP) and accounts receivable (AR) are ignored. This leaves far too many manufacturers at a disadvantage when it comes to meeting operational efficiency goals.
Often AP and AR professionals start automation strategies by implementing enterprise resource planning (ERP) solutions to track resources and the status of business commitments. But ERP systems alone leave information gaps that need to be filled.
In the past decade, more organizations have adopted additional AP and AR automation technologies, such as enterprise information platforms, and integrated them with their ERP solutions to fill data and process gaps. These enterprise information platforms connect transactional data with relevant content to support business activities, giving manufacturers quick access to the information they need and linking business transactions with the required documentation.
Revolutionizing AP and AR Automation
Digitize and Centralize
The first step to automation within AP and AR departments is capturing and centralizing both physical and electronic documents. This may seem like an easy concept, but you wouldn’t believe how many organizations still rely on paper for certain steps of their internal processes, or have PDF files scattered across computer desktops and file shares. Organizing these documents across the organization is an essential part of embracing automation because hard copies take up too much space, and loose files of any format are easily lost and hard to track when you need them most.
Digitizing files associated with AP and AR processes, such as invoices and sales orders, the moment they come into an organization is a great first step to automation. Not only does this reduce the risk of losing information, but it also makes it easier, and quicker, to share that information with other departments.
Enterprise information platforms, equipped with enterprise content management (ECM), case management, business process management (BPM), records management and capture, play a critical role here. As documents are captured electronically, whether from customer emails, mobile devices or scanned physical documents, the enterprise information system sorts and links that information with other relevant or related documents so that it can be quickly retrieved by staff.
Integration
Integrations are an essential part enterprise information platform’s functionality set. As documents are captured, the system lifts critical data from the documents then delivers that information to the ERP or order system, validating the extracted data against existing information within the ERP. For example, in order processing enterprise information platforms can intelligently recognize the manufacturer or product number on a purchase order and validate that number and price against the customer’s contract list.
The information captured from the enterprise information system includes PO numbers, vendor information, invoice amounts and line item details. Key benefits of these integrations include:
- Eliminates manual data entry and the risks associated with data entry errors
- Frees up staff’s time to focus on higher value tasks to improve relationships with vendors or customers
- Reduces the need to add ERP seats and additional licenses for users in each department, saving money in overhead costs
- Improves visibility, speed of dispute resolution and exception handling because people can access the documents they need to resolve disputes over payments or orders. Integrating enterprise information platforms with ERP systems allows staff to bring documents related to a particular transaction form with ERP interface they are most familiar.
Revolutionize
The final step to AP and AR automation and transformation is, in my opinion, the most fun. Once business-critical AP and AR information is electronic and central for all employees, it’s time to automate related processes to further increase productivity.
To do so you must evaluate how your AP and AR department functions. From past experience, we’ve seen many manufacturers target the following areas:
- Manual activity routing: I recommend using automated workflows generated from the enterprise information system to send documents and supporting information to staff who need to perform processing tasks based on that information. Staff then have the ability to quickly make decisions, such as approving or rejecting an invoice, which will trigger the next step in the process, without staff needing to track or manage the process on separate spreadsheets, notepads or email chains.
- Manual exception handling and dispute resolution: With workflow automation organizations can ensure that exceptions or issues about particular invoices and orders are routed and escalated to the appropriate reviewers in a timely fashion. Again, these integrations allow staff to access relevant documents related to specific transactions to resolve issues more quickly.
When it comes to business operations, the manufacturing floor isn’t the only place where automation is critical to gain optimal operational efficiency. Internal departments like AP and AR have too often been overlooked within industry. In the world of digitization, however, this is changing dramatically. Using technology — such as ERP systems and enterprise information platforms — connects content throughout departments for a holistic view of documentation, while facilitating data flow between all business functions to better manage internal operations.
Danielle Simer is a commercial marketing portfolio manager at Hyland.