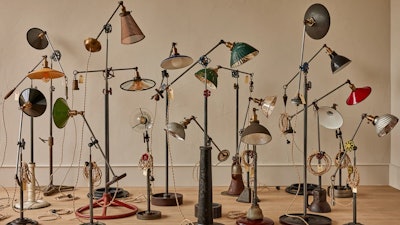
RTO Lighting is a custom high-end lighting company from Philadelphia. The company was founded in 2002 by Robert Ogden as a side project. Since its humble start at his garage, RTO Lighting has grown into a sizeable operation.
In 2008, Robert and his wife acquired Lostine, a home furnishing company where the couple had previously worked as designers. Much like RTO Lighting, Lostine has become a well-known brand in the premium home furnishings market. While separate entities, the two companies often collaborate and manufacture products for each other.
Driven by the owners’ vision of producing high-quality products proudly crafted in the USA, the businesses grew from a small team of seven to a combined workforce of nearly 60 employees across both companies.
Growing businesses require scalable solutions
Operating two distinct yet interconnected businesses presented Robert and his wife with unique challenges. For years, they used a host of spreadsheets for costing and production planning. As the companies grew, this patchwork solution started showing its limits, making the companies realize that a more robust solution was needed.
“We had started using a stock management system but realized that it doesn’t track time in manufacturing or labor. As a manufacturer, we needed to capture time as an expense, to quote lead times, and to know our costs more accurately,” Robert explains.
Robert Ogden and Natalie Page, Co-Owners of RTO Lighting and LostineMRPeasy
The need for a unified system that would provide efficient inventory management, labor and cost tracking, and production scheduling became increasingly urgent.
Discovering MRP systems and the decision to implement
Robert first heard about MRP (Manufacturing Resource Planning) software in general and MRPeasy specifically from a helpful salesperson at a CRM software company who provided a list of packages to look through.
MRPeasy’s user-friendliness and production scheduling capabilities immediately impressed him. “When I looked at how easily you could manipulate the production calendar in MRPeasy, I thought it was perfect. I showed it to my team, and everyone agreed once they saw the ease of use,” Robert recalls.
Other key factors in the decision were MRPeasy’s effortless labor tracking and accurate cost and lead time estimating functionalities, which would enable Robert to analyze margins per product and built-in support for RTO Lighting’s accounting platform QuickBooks.
“MRPeasy seemed capable of solving all of our needs for material planning and offered functionalities that we didn’t even know we needed at the time of implementation, yet are using daily now,” Robert shares.
The challenge of double implementation
Robert quickly realized that it would be beneficial to implement MRPeasy in both companies simultaneously. This collaboration quickly proved instrumental in easing the learning curve and ensuring a smooth transition for both teams.
The process took around eight months, four of which were parallel testing with the old systems. Implementation involved two part-time employees. Reflecting on the experience, Robert notes: “I wish I had put two people on it full-time from the start. It was a bigger task than we anticipated, but the benefits far outweighed the challenges.”
Robert also engaged an authorized MRPeasy consulting company to speed up the process and provide further guidance.
Transforming operations with MRPeasy
Since successfully implementing MRPeasy in spring 2023, RTO Lighting and Lostine have reached new levels of operational efficiency due to much more accurate labor tracking, real-time inventory management, and precise cost calculations.
MRPeasy is allowing both companies to not only accurately predict lead times but also shorten them thanks to time saved on managerial tasks. Labor utilization has also seen a significant boost, as has material tracking accuracy.
Robert describes the impact: “MRPeasy is a powerful and necessary tool for manufacturing. It’s like a forklift – when you finally buy your first one, you quickly wonder how you ever lived without it!”
Lessons learned: advice for manufacturers looking to scale
Reflecting on the implementation process, Robert points out that underestimating the resources needed for implementing an MRP system is one of the biggest mistakes a company can make. He also highlights the value of external consultants in accelerating implementation and providing insights into best practices.
Roberts's final piece of advice to other manufacturers is to always keep the bigger picture in mind when contemplating manufacturing software: “Accurate data leads to better decision-making. Understanding profit per square foot, per hour of labor, and material usage has allowed us to optimize capacity utilization and efficiency. Investing in the right system—and the right people to implement it—has been a game changer for us.”
For more information, visit https://www.mrpeasy.com/.