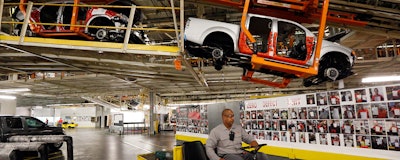
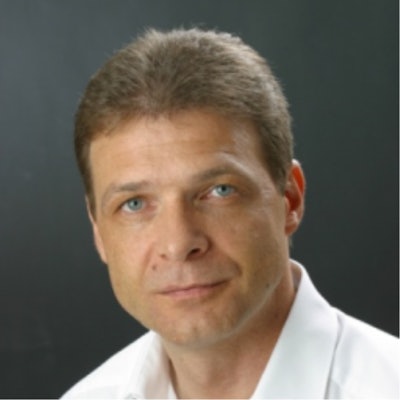
If you agree that Germany epitomizes automotive manufacturing excellence, then you may wish to be attentive to what’s happening now in that manufacturing juggernaut — namely, that improving software development processes has become a major theme in influential circles.
In fact, in a 2014 CeBIT speech, Chancellor Angela Merkel spoke about the need to embrace the challenge of becoming a leader in software development in order to stay on the leading edge of manufacturing. Major technology firms based in Germany have spoken about achieving a better balance between software and hardware to maintain their global leadership positions. One German automotive firm even made the comment that automobiles are simply becoming metal boxes that hold the software that makes them work. Another automotive firm noted that software development will become the single most important consideration in new product development engineering.
As a result, DevOps, Agile and Lean initiatives are taking off at many automotive manufacturers, which seek to improve their software development lifecycles. Some have even begun building “software manufacturing plants,” essentially IT research centers, to help maintain Germany’s position as a country that leads in engineering. One of the primary goals of these initiatives is to reduce the development time of getting a new car on the road from five to three years.
These developments are so dramatic that some have compared what’s happening today to the manufacturing revolution of 100 years ago. Is that a stretch? Perhaps. But just-in-time manufacturing, which revolutionized production 50 years ago in Japan and then spread globally, is no longer the Holy Grail. Today, German manufacturers have begun using “just-in-sequence” techniques to deliver the right software, the right parts and the right car at the right time. That’s because in Europe it’s increasingly common for consumers to visit a car dealership, design their own cars based upon various options, then wait as new cars are built to spec. With just-in-sequence techniques, suppliers deliver the components (wheels, engine, etc.) in the right sequence to auto manufacturers for assembling. Adding software to this hardware equation is necessary but incredibly challenging.
To achieve this, software quality must improve to new levels. But with cars increasingly use 100 million lines of software code per vehicle — and Germany experiencing a shortage of quality developers to write that code — many challenges stand in the way of achieving Lean Application Lifecycle Management (ALM), which seeks to involve automating communication processes and enhancing collaboration across the tool chain. This leads to the elimination of wasteful manual processes and complex maintenance among systems and across supply chains.
Challenges
One of the biggest problems is that because of the use of massive numbers of parts suppliers in locations across the globe, automotive suppliers don’t have real control throughout their supply chains. Add to that the fact that these suppliers have many divisions, using many different software tools, and you can see the monumental challenge. One prominent automotive parts supplier uses 26 different software tools, for example. Meanwhile, there are no real standards for tools, which adds to the complexity of the tool chain. And for auto manufacturers to be successful, they must get these tools to communicate with one another.
Beyond this, there is far too little visibility in the process. That makes traceability and compliance throughout the whole line very difficult. A major component of this problem is that the supply chain includes a variety of partners scattered across the globe. So it is very difficult to connect them all, make processes transparent and remain compliant with global regulations.
Then there is the issue of poor collaboration between hardware and software development teams, which impedes software development and delivery. Developers are still emailing spreadsheets to communicate, making efficient collaboration difficult. And hardware and software teams use different terminology, impeding understanding. For example, the terms “requirements” and “features” mean different things in hardware and software circles. This points to the need to establish a platform of communication, to reduce errors from an estimated 20 percent today to what should be less than one percent for truly lean manufacturing.
And finally, new suppliers like Apple, Google and Tesla have entered the arena. Automobile manufacturers are very concerned with third-parties like Google owning mapping, since navigation systems have increasingly become a strategic asset for automobile manufacturers.
Overcoming challenges
So if you are an OEM or a supplier in the automotive industry, how can you overcome these challenges — or at least manage them — and get to Lean ALM?
Some CEOs and general managers of leading German automotive manufactures have communicated radical changes to their businesses. In the near future they expect to generate their value by software and services. This means major changes to the whole industry.
Clearly, the lack of software integration is the biggest bottleneck in software delivery. To address this involves integrating everyone in the entire software lifecycle, including project managers, developers, architects, testers, business analysts, service desk members, etc. And it involves achieving all of the following:
- Insight across all projects & tools
- Compliance & traceability
- Automated processes and flow
- Real-time collaboration
- A single version of the truth
The benefits include achieving measurable Agile/DevOps ROI, an increased efficiency that leads to decreased cycle and resolution times; reduced total cost of ownership of lifecycle tools; a reduced risk of changes and upgrades; and the elimination of integration failures.
The first step of achieving this is for OEMs to begin integrating their software and hardware development teams so they work jointly on future car versions. The next step is for suppliers to implement this roadmap in their own companies. And finally, OEMs must expand collaboration across the entire supply chain, including a very tight collaboration on software and services.
A critical point in this massive change will be integration to increase collaboration not only with the ALM tool stack but also across the enterprise supply chain of each company.
With this integration, requirements from the auto manufacturer will flow to suppliers automatically. If a supplier finds a defect, it can automatically be tracked by the manufacturer. If the manufacturer finds a defect in the supplier's product, it can automatically send it to the supplier to fix. The result: the status of requirements and defects are always up-to-date on both sides!
Summary
While Lean manufacturing was the standard for automobile manufacturers in the past, the future points to Lean ALM throughout the software development lifecycle. German manufacturers have already begun on this path. As such, others seeking to remain competitive globally should also begin to establish Lean ALM management initiatives to oversee all projects across all lines of business for better transparency. Their future depends upon it.
Martin Kasbauer is European Business Development Manager at Tasktop.