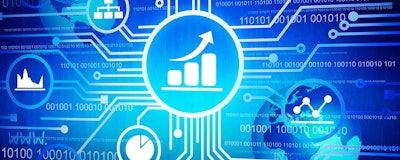
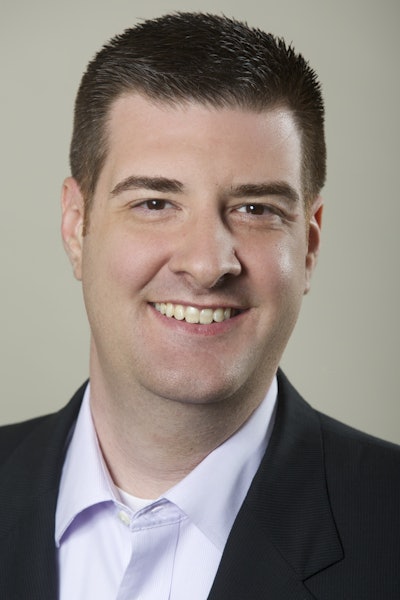
The need for manufacturers to become “digital” has been a well-covered concept and for good reason. Whether it’s referred to as Manufacturing 4.0, Industry 4.0, Smart Manufacturing or Connected Manufacturing, it’s an intriguing topic worthy of in-depth examination for most manufacturers. As we get deeper into the year, a digital transformation shift will be seen across the entire manufacturing industry, along with new initiatives and ramifications stemming from this shift.
Here are a few examples of the changes still to come:
Digital Transformations Driving Growth and Profit
Manufacturers are starting to adopt technologies that transform their operating models and digitally connect processes, events, actions, internal associates and external partners. As a result, global standards that are flexible enough to accommodate regional, customer or product requirements have become a focus. Let’s look at the classic example of field servicing. Currently, manufacturers sell a piece of equipment and a corresponding service contract. Alternatively, the service contract could be held by a distributor. When a service call is placed, by the customer, field technicians arrive — typically with limited knowledge of the issue. Diagnosing a problem opens another set of obstacles, as the technician may not have the correct skills, tools or parts on hand to resolve the issue. The end result of this limited visibility for the manufacturer is not knowing exactly how a product is being utilized, what is required of the supply chain or even how much inventory is needed in stock. And, most importantly, the customer serves as the first notification point of an issue. All this leads to the manufacturer being unable to capitalize on a potential profitable revenue stream.
Let’s examine this scenario from a digital manufacturer’s point of view. This company has the ability to obtain data directly from the equipment, continuously analyze the data, predict outcomes and act immediately. The deployed field service technician is armed with knowledge about the issue in advance, is selected because of his or her ability to repair the most probable issue and — most importantly — replacement components are automatically ordered as needed and replacement stock is minimized. As a result, first call repair rates and customer satisfaction increases, which translates into a higher propensity of repeat purchases. Costs are low and the customer isn’t initiating a request and then waiting for service. The digital manufacturer can now capitalize on a new revenue stream by converting its make-and-service model to an outcome-based model where customers purchase outcomes, such as uptime, availability, quality output and yield, rather than the piece of equipment and the corresponding service contract.
Collaborative Innovation
This shift is the “Connected” portion of the term “Connected Manufacturing” and is the true alignment of people, equipment and technology relying on collaboration throughout the enterprise and the extended supply chain. Collaborative innovation requires a deeper strategic understanding of unique and standalone capabilities, as well as a comprehension of the outcomes that can be delivered by partners and the enterprise. While manufacturers have historically been willing to share objectives, they must now also be willing to share vital information that has typically been held close to the chest, such as specific product development and deprecation plans.
Utilizing the same field service example as above, suppliers will now be required to provide components in a consistent time frame and to ensure optimal costs, suppliers must maintain a manageable inventory quantity which requires automated, consistent updates of short and long-term demand. Accomplishing this requires the sharing of trusted and closely guarded knowledge — a trend that is just starting in the industry. The result of this transformation is that manufacturers will transition their supply chains to supply webs, where partners become interdependent, co-innovative and collaborative with each other on both a tactical and strategic level in order to create shared and distributed value.
Property Protection
Information sharing is critical to successful collaboration but the cost of losing intellectual property can be devastating. According to analysis by Netnames, counterfeiting increases by 15% annually and already costs manufacturers a staggering $1.8 trillion dollars in lost annual revenues. Considering that collaboration at this new digital level involves trust, and that manufacturers need to be hyper-vigilant about piracy, counterfeiting and intellectual property theft, protecting schematics and technology advances from piracy or theft from suppliers will force many manufacturers to make some very difficult decisions.
When collaboration is done with shared objectives top of mind, a manufacturer becomes critically important to the success of a supplier and vice versa. This dynamic causes the supplier to become more diligent in aiding the identification of counterfeit or pirated products and manufacturers to make a concerted effort to track certified products to quickly identify the root causes of found counterfeit goods.
The industry shift toward enterprises becoming digital will continue to be a central element to any manufacturing strategy in the months to come. It will prove to be the lynch pin for all major initiatives as the success of this adoption will be directly measured by the impact on the bottom line. This digital transformation will enable enterprise and the extended enterprise to become aligned on common objectives: collaboration and increased revenue.
Sean Riley is Global Industry Director of Manufacturing, Supply Chain & Logistics at Software AG.