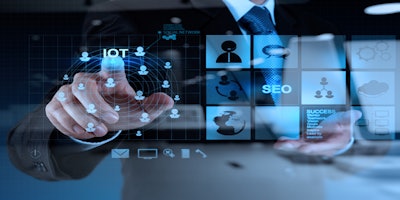
New year, new budget, big plans. In manufacturing, we develop our workforce, systems, and technology to ensure that forward progress never stops. The year ahead holds myriad opportunities to transform manufacturing operations. Investments in digital platforms, automation, and IoT-enabled data analytics continue apace. Leading manufacturers are folding the lessons learned in recent years back into their transformative mix of smart manufacturing practices and components. It’s time to smooth out the hype cycle rollercoaster by focusing on IT evolution and integration on the shop floor, clarity around technology use cases, and how to apply data and analytics to reach higher levels of orchestration.
With evolution, clarity, and optimization in mind, here are a few trends to track and learn about throughout 2018.
1. The re-emergence of MES as a central component of smart manufacturing implementations: There’s been a lot of buzz around new manufacturing platforms and apps. It’s not hard to see why — easy workforce and equipment management, mobile monitoring of processes, and ready access to real-time metrics are central digital manufacturing goals. The apps promise enticing gains in efficiency and productivity, but serious concerns about their security and reliability abound. Building your own apps sounds great until lack of strategic planning, integration, and control leaves you with you a mishmash of tools and apps that don’t play well together, need to be updated separately, and cannot be efficiently sustained in the long term. Shadow IT is not a game you want to play in the high stakes arena of industrial control systems, manufacturing equipment, or highly regulated industries.
The need for MES is greater than ever for coordination, governance and data management required behind these manufacturing apps. Analyst firms like Gartner and LNS Research have predicted the potential demise of MES, but it is no coincidence that recent surveys from the same firms, indicate that MES is still on top of manufacturers’ implementation lists for 2018. Why is there momentum behind MES/MOM software? Because the benefits are abundant and well documented; every manufacturer wants a piece of that success. Plants that get their act together and organize their manufacturing systems will see a payoff – often tenfold.
MES technology and integration tools aren’t frozen in time; they are being continuously improved and reshaped with new coordinating functions, industry-specific features, and more adaptive interfaces. As the app hype (which is fed in part by IoT vendors) subsides, many smart manufacturers are rediscovering why MES capabilities are critical and new apps can be a good complementary strategy.
When PCs hit the shop floor, everyone went crazy creating spreadsheets. We ended up with silos of data all over the shop floor. In the digital transformation era, we will know better. Smart manufacturing is about architecting systems and processes around a single version of the truth (e.g., the digital thread and digital twin). Even if the use of apps continues to be prevalent, IT will insist on using MES systems and experts to create, manage, and integrate them.
2. Clarity around IIoT use cases will begin to crystallize. IIoT platforms are not a replacement for functions in ERP, PLM, or MES — they are supplementary and complementary. These IIoT platforms provide new ways to bridge data from sensors, equipment, and hardware to enterprise IT systems.
IIoT platforms can also provide great analytics tools, but many have made exaggerated claims. There’s a lot of focus on the big data generated by IIoT-enabled manufacturing systems, but there’s no magic platform that simply taps into unstructured data and produces operational insights. Manufacturing data is not trivial; making meaningful, efficient use of it requires manufacturing intelligence experience and specific data science skills. Once the dust settles, those who have struggled through early adoption will help clear the hype and document the practical use cases of real benefit to manufacturers.
Lessons that digital transformation leaders have learned will be more widely understood. Namely, that the biggest value in connecting equipment and processes digitally is not the resulting analytics and intelligence — those are a beneficial side effect, in a way. The main goal is leveraging connectivity to reach higher levels of orchestration and process optimization. Easily obtained metrics are great, but getting product out the door faster, more consistently, and at higher quality — that’s the real value, and should be the primary driver for investment and implementation.
3. Addressing security and governance concerns will fuel innovation and integration. These concerns are necessary obstacles but will lead to improved smart manufacturing practices and standards.
To deliver on the promise of IoT and real-time data monitoring, we need data sharing, digital handovers, and common connectivity architecture and semantics. As the demand for integration and interoperability grows, standard approaches to bridging operational tech on the shop floor to IT and enterprise systems will mature. Security concerns have made some manufacturers reluctant to connect machines to the IT network, but everyone wants to do it, and they want it to be as easy as activating a smartphone. The demand and momentum are strong enough to drive the development of secure standards over the course of this year.
4. Adaptive UIs, including Augmented Reality (AR) interfaces and guidance systems, will continue to improve. Smart glasses, head-up displays, and voice-activated apps will become more prevalent on the shop floor, and more closely integrated with physical equipment. Improved digital interfaces can more readily adapt to multiple configurations and process changes. The ability to work hands-free (no need to carry a tablet) will increase productivity and reduce errors. As AR technology progresses, more use cases will be identified, driving a demand for more AR authors and experts. AR promises to support a more flexible workforce; instead of relying on memory or written instructions, these systems will provide prompts as technicians and production workers move through steps.
Smart manufacturing is about bringing digital and physical systems together, and providing more streamlined ways for people to interact with both. Connectivity and real-time data are quickly becoming standard in manufacturing — paper-based systems, end-of-day reports, and manual troubleshooting are simply insufficient. We may not know yet how all the pieces fit together, or what we will call the tiers of innovative systems we develop as we puzzle it out, but we know what we are aiming for — operational excellence, a single version of the truth, and IT maturity around security and standards — all leading to a fully digital manufacturing enterprise.
As Gartner’s MES analyst Rick Franzosa puts it, “It doesn’t matter what the tool is called, as long as it does the job for you.” Keeping MES in your toolbox will position you for smart manufacturing success in 2018.
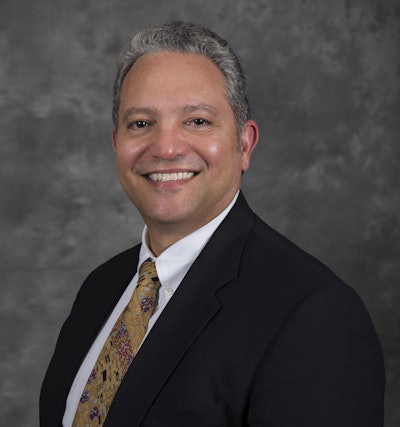
Conrad Leiva is VP Product Strategy and Alliances at iBASEt, a provider of software solutions to complex, highly regulated industries.