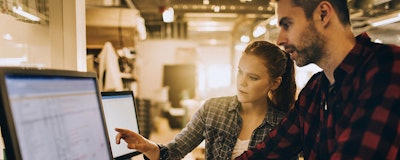
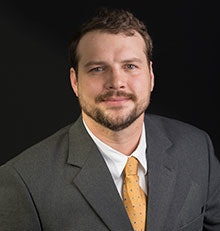
Successfully guiding a project during the late phases of design and construction is no small task. It is the result of considerable planning among the stakeholders from the outset of design. Through this process, the trust established early on significantly supports collaboration in evaluating the opportunities and risks of unavoidable change requests that are common in the 11th hour of a project, especially in manufacturing.
Here’s what to consider when hurdling the last-minute challenges.
Key Initial Considerations
Several questions are foundational at the outset: Is the ultimate objective quality, schedule or cost? If it is cost, is it first cost only or does it cover long-term costs over the lifetime of the facility? The team is naturally eager to break ground and get rolling, but if it has not agreed to a process of communication and approval of change requests, the delays caused by uncertainties, over assessment and authorization can wreck the most sophisticated schedule.
There is always a driver behind any change request, but that motivation may not be clear to the project team because it involves proprietary information. Will the changes require unexpected modifications that will have a trickle-down effect on cost? Only if clear business objectives have been defined for the project can changes be evaluated with respect to the impact they will have on those objectives.
The methodologies of Design Assist and Design-Build are often driven only by first cost or a Guaranteed Maximum Price, GMP. Architects and engineers will always focus on preserving quality. When assessing the impact of a change at any phase of the project, the team needs to know the implications of the change for the remaining phases of construction as well as for the long-term viability of the facility. When considering an 11th hour change, look for savings from a VE (Value Engineering) analysis. Slight modifications may yield cost savings and protect the schedule while providing almost the same outcome as the original contracted order.
Also, make sure that the project team has clearly delineated the scope of the project and determined which resources are responsible for each process or package in the schedule.
Obviously safety is non-negotiable. A structural change may introduce more weight than the design allowed for in the foundation or for elements such as structural members can bear. Will changes to electrical equipment — such as brace rating/ short circuit ratings — require a wider safety approach boundary? If so, the change may entail additional cost and schedule slippage.
Safety requires more logic than getting 100,000 pounds of gear up through a small access hole into a substation room on the roof. Falls pose a liability risk without proper railing or harness. Does the design include guard rails and spill containment? Is the hoist rated for the largest pieces it will lift? Does it have to be vault construction with three-hour concrete? Does the equipment use silicone or vegetable oil instead of less flammable mineral oil? Is the area sprinkled? Is there emergency egress and emergency lighting in place? Are there two methods of escape? These are typical Basic Building codes.
Any change that raises a question of code compliance is critical. Haste is no defense against code deviations or standard violations. An unpredictable outcome is the opposite of quality. That is why it is essential to develop and stay with a process to think changes through. Here are examples on how.
Three Examples
The following cases typify the challenges that can arise late in a project and the risks that they can pose.
- A manufacturer substituted a new piece of equipment late in the planning. This equipment had different characteristics — such as footprint, characteristic, electrical rating — than what had been planned for. This resulted in late-phase redesign and added time to the schedule. Decisive early planning factoring code compliance, as well as organization including clearly defined roles, responsibilities, and intermediate project milestones are opportunities for project teams to anticipate such challenges.
- A change calls for using equipment from overseas that is not UL rated for North America. For example, it may have a different short circuit rating lower than anticipated. It requires several software iterations to run a calculation on the short circuit current of equipment to determine how to coordinate the feeder lengths, fuses, or isolation transformers to decrease the short circuit or arc flash category. This computation adds time to the schedule if project planners don’t factor in third-party testing to meet UL requirements. Thorough vetting of the equipment as an integral part of the planning process as well as creating buffers in the project schedule to account for such testing enables project teams to avoid such challenges. In some cases, the only solution is a workaround, such as isolating internal electronics within the panel, but the manufacturer has to be consulted, which can cause further scheduling challenges.
- A sub room was built with a pad-mounted substation that was 40 feet long and 7-8 feet deep. For plant maintenance personnel to access the room they had to walk around one department by going outside the plant along the safety lines. Then they had to put earplugs on to walk through another department and finally walk around a truck area — all this just to get to the sub room. The design didn’t include a door into the room directly from an adjoining department because of the silo effect. No department wanted to cede square footage to accommodate the passage of maintenance personnel through its facility. One way to discourage this compartmentalization is to share the cost savings of design collaboration so that adjacent departments are rewarded for cooperating in the design to benefit the entire project. Collaborative meetings and cross-departmental cooperation that integrate efforts versus team members working in silos can offer opportunities to achieve collective solutions.
Insight
At the beginning of the project, create a project action matrix and keep it updated. The matrix tracks each item in the scoped project and shows the discipline that owns the item, the originator, date, and when additional information is needed. Doing this clarifies what point each phase of design or construction has reached, and it reveals whether any issue is holding it up. The largest risk of a breakdown occurs when parties resort to talking in sidebars and nobody copies decisions to the job folder or to the project managers.
Keep documentation in a meeting minutes folder. Move older documents to an archive folder and keep only current versions. Minutes must be accurate and updated. Record keeping is not done with an eye to dispute resolution; it is for done for other people to consult if the project manager is away.
As a predesign exercise, show materials on drawings. The specs should be visible for plan review so that the inspector can compare the plans to the as-built facility.
To check the completeness of a proposed change, include the following assignments. Digest all the information concerning the scope of the change. Calculate how many, if any, extra resources will need to be added to the team. Have the project team perform a risk assessment. What could go wrong? For example, what if there were not enough power in the service to handle the change? The first person who sees an issue must communicate it to all the disciplines or departments, as well as to the owner's team, so that the issue can be assessed from every angle as well the accompanying changes to cost, time schedule and effort.
And finally, make sure your entire team understands what is driving this project. If it is a product launch, then perhaps speed is more important than cost. If it is a product with a razor thin margin, perhaps cost is a critical metric.
Maybe the last minute change is driven by a critical retail customer with a lot of buying power. Understanding the business drivers for a project will help the entire team make better decisions on how to deal with potential last minute changes.
Trust
Keeping a project's wheels on the tracks during the late phase of construction is the result of careful planning and comprehensive communication among the stakeholders from the beginning of the design phase, so that the trust established in the early months will serve collaboration in evaluating the opportunities and risks of unavoidable change requests later during construction.
Corey Zachel, PE, LEED AP BD+C, is a Section Manager and Senior Associate at SSOE Group, a global project delivery firm for architecture, engineering, and construction management. With 17 years of experience, Corey produces and reviews electrical documents.