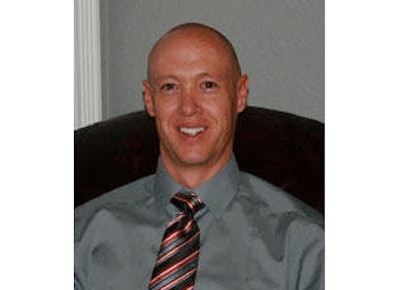
I do not have a collection of data over decades from which to produce a trend. I have only my perceptions. So I offer up the following as food for thought and comment. I observe a change in our judgment concerning the limits of our capabilities and good enough versus poor. I think often that industry in general struggles to maintain control of processes tightly enough to ensure performance so close to the limits we set. As a result we create quality and performance problems in spite of ourselves.
At the risk of dating myself, when I went through engineering school the accepted practice to ensure that a design would measure up to the unpredicted possibilities of stress or abuse or challenge was to engineer with a safety factor. Depending upon the criticality or risk to safety of a design, a safety factor from 0.5 to 2 was generally selected.
As I became more experienced, more precise methods came into play. Six Sigma, specifically the discipline Design for Six Sigma, introduced statistical methods of predicting variation, errors, and testing design limits. It enabled us to utilize statistical tolerance methods to effectively optimize designs that would not be acceptable according to traditional methods. It also enabled us to be more precise than assumptions and guesswork in terms of setting our design parameters with regard to performance limits.
The science of mapping performance distributions told us exactly where we could set our process controls in order to ensure virtually 100% defect-free results. It is a better method than assuming or guessing at an appropriate safety factor.
Similarly, the Lean methodology with its directive to eliminate waste and variation taught us how to incrementally improve processes, and the designs that went into those processes, by carefully observing the performance constraints of those processes and setting our design parameters according to what was easiest or most powerfully controlled. Likewise the practice of Statistical Process Control ensures that we not only maintain our performance levels, but also anticipate changes or problems before they turn into quality or performance issues.
In short, a wide variety of practices and methodologies enable us to pursue optimization with greater sophistication than designing to arbitrary safety factors or setting controls well within limits. Progress is good.
[Continue reading...]