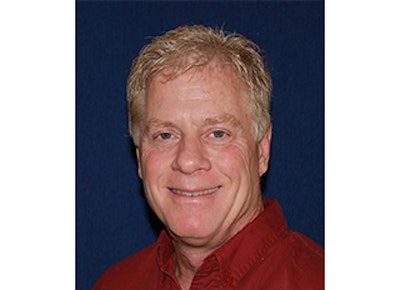
The rising cost of energy has forced many manufacturers to focus their sights on innovative ways to optimize energy consumption and improve operational efficiency in their manufacturing, product lines, distribution, and administrative operations. Switching to fluorescent or LED lighting, replacing HVAC to a more efficient system or upgrading to integrated process controls architecture to streamline production – these, and scores of other initiatives can be undertaken to make product manufacturers more energy efficient, productive, and sustainable. Energy management, process efficiency and incorporating more sustainable procedures are critical for maintaining a competitive edge in today’s markets. Indeed, the need for streamlining energy usage and providing creative solutions for sustainability issues has never been stronger.
In the manufacturing of material handling equipment, for example, almost any manufacturer of highly automated systems has incorporated some degree of improved energy efficiency into their product lines, such as conveyors and sortation units with highly-efficient PLCs and servo-drives, laser-guided vehicles with rechargeable batteries, and high-speed AS/RS (automated storage and retrieval systems) and picking systems utilizing ultra-capacitors that store energy electrostatically. These product improvements in energy reduction are significant. But despite the necessity for better energy management, too many companies that manufacture these highly energy-efficient material handling systems have made only nominal strides in energy optimization to their own facilities, and are still running their plants, warehouses and administrative offices from traditional energy sources that are non-renewable, and increasingly costly.
One equipment manufacturer that has made the move to renewable energy is OPEX Corporation (OPEX), known worldwide for its high-speed mail handling and document imaging systems and sorters, and automated goods-to-person picking systems for warehousing. OPEX has recently taken its sustainability initiatives to a new level by integrating a 2.77 megawatt (MW) solar array system capable of producing more than 100 percent of the electrical energy needed to operate its 250,000 square-foot manufacturing, distribution and administrative complex located in Moorestown, New Jersey. Not only is OPEX now effectively a net-zero user of electrical power from traditional energy sources, its conversion to sun power makes it the largest solar installation in the state of New Jersey operated by a privately-held company. In effect, power required to manufacture the company’s entire product line of automated material handling systems is now derived, 100 percent, from a sustainable source.
[Continue reading...]