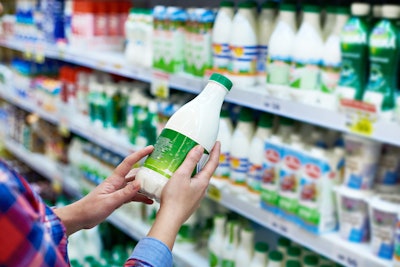
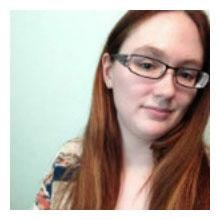
Companies that know manufacturing know lean is the way to go. But even lean operations might have some work to do if they’re not using the right tools.
As far as advanced technology goes in the manufacturing sector, RFID is actually pretty simple. For just pennies each, radio frequency identification tags, or chips, can enhance your top-down understanding of everything happening in your manufacturing outfit and make your lean operation even leaner still.
RFID Facilitates an Organization-Wide Culture of Improvement
We shouldn’t have to explain the benefits of lean manufacturing. Suffice it to say, reducing waste and redundancy benefits profitability one company at a time, but it also helps reduce the cumulative “footprint” of the entire industry. But doing any of this well requires companies to make continuous process improvements a matter of their culture. And making improvements means gathering information you can act upon.
RFID can improve the fundamentals of your operation by helping you gather information far more quickly than you could using conventional means. What information? Things like:
- The location of raw materials and finished products within one facility, whether on the assembly line or stowed away in your racks for retrieval.
- The level of available inventory at each of several facilities.
- The speed at which parts and unfinished products move from one phase of to the next, and the time required for each step along the way.
Lean manufacturers already know that their “front-line” workers are in a great position to identify sources of waste and to tag opportunities for improvement. But adding RFID technology to your operation can put even more tools into the hands of these workers.
You might be worried about data overload, but RFID adopters have already logged positive results after making RFID technology a part of new employee training from the very beginning. Empowering employees with this type of data-gathering technology, in an environment that values continual positive change, results in real worker empowerment. This, in turn, makes them more likely to spot bottlenecks and areas that could stand to be reevaluated.
RFID Makes Inventory Maintenance Practically Painless
Inventory maintenance is a time-consuming task for almost any outfit. In times now happily behind us, “doing inventory” by hand could take hundreds of hours or more. But with RFID technology, you can accomplish the same task, and come away with the same information, in just two hours in many cases.
There are several specific use cases that might be of interest here. An RFID-powered inventory system also gives you a tool for tracking the age and expiration of products across one facility or several. Perishable goods like foods and beverages are an obvious fit, but so is any portion of the supply chain that touches the medical fields. Hospitals rely on the steady movement of a dizzying variety of disposable products such as splints, bandages, pads for EKG machines and even bedpans, some of which have finite shelf lives.
By tagging sensitive inventory like this with RFID chips, you can more easily move slower-moving items from one location to another to ensure they’re used before their shelf life expires. It’s another way to make sure nothing’s being manufactured that doesn’t strictly need to be.
RFID Delivers More Actionable Data for Quality Control and Efficiency Checks
The technology that powers RFID is the heir apparent to the barcode, which let manufacturers perform a lot of the tasks we’re talking about here today, but required far more time and handling. Whereas barcodes need to be scanned one at a time, and usually by hand, RFID tags can be read by the corresponding receiver in bulk, meaning it’s easier than ever to see at a glance which products, and how many, arrived on your dock. It also means you can tell right away whether it’s actually what you ordered.
This part of quality control is made vastly easier with RFID tech on your side. So is the swapping-out of merchandise that was damaged in transit. The benefits here are twofold — customers get to expect faster turnaround times and resolution, while employers get to spend less labor and money on taking corrective actions. Each process can be performed by smaller teams of employees and with fewer “touches” on the products, which means fewer opportunities for you to introduce errors of your own into the mix.
It’s worth mentioning industrial certifications in this context, too. Obtaining certification in accordance with ISO and other international quality standards means building a deliberate, repeatable and scalable process to ensure consistent results throughout your operation. Since RFID technology provides abundant insights precisely along these lines, it could prove invaluable if the work you do requires specific credentials or accreditations from governing bodies.
RFID Provides Immediate Insights From Retail and Point-of-Sale
We’ve talked mostly about the production side of things, but the hugely important other side of the lean manufacturing “coin” is getting insight from the consumer’s side of things. That means retail.
RFID tags reduce friction in your operations while delivering data more reliably and quickly. But they can accomplish the same thing in a retail setting, too, by delivering information immediately about which products are leaving stores quickly and which locations have a surplus that another location could use.
This has implications beyond inventory tracking — it’s really an up-to-the-minute-accurate glimpse into the shopping habits and locations of the audiences you’re ultimately targeting. Lean manufacturing answers “demand” with an ever-more-efficiently-delivered “supply.” RFID delivers huge efficiency boosts on both sides of that equation.
That’s the key takeaway here: introducing RFID into a lean manufacturing operation is a win for all involved. From supply all the way to demand, it’s easier than ever to know what’s happening under your roof — and how it all fits into the bigger picture.