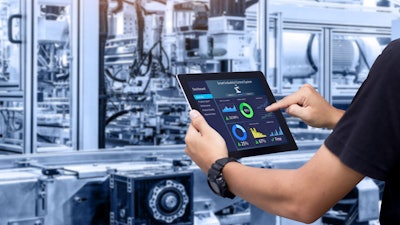
The concept of a "smart factory" has gone from an interesting concept to a common, but critical element of modern manufacturing in only about a decade. The rapid rise in sensor technology has enabled factories across the world to turn existing facilities into smart factories or build them smart from the ground up. But what precisely is a smart factory? And given how much they've advanced in just the past decade, what does the near future hold for them?
We chatted with an expert on smart factories to get some answers on this. Below, check out our recent conversation with Stephen Laaper, principal and Smart Factory Leader at Deloitte Consulting LL, where we got his insights the current state of smart factories and what the outlook for them is.
Manufacturing.net: How would you define "smart factory," and what is your vision for manufacturing over the next five years?
Laaper
- Connected processes, materials, and equipment
- Optimized for minimal manual intervention and high reliability
- Transparent network to enable greater visibility across the facility
- Proactive approach for issue identification and troubleshooting
- Agile operations to self-configure equipment and material flows with staffing, schedule, and product changes
In Deloitte’s 2019 Deloitte and MAPI Smart Factory Study, “Capturing value through the digital journey,” we found that in the United States alone, 86 percent of manufacturers believe that smart factories will be the main driver of competition by 2025. Furthermore, 83 percent believe that smart factories will transform the way products are made.
Over the next five years, agility will be key to how manufacturers manage disruption. Investing in digital transformation across production and the supply network can help manufacturers respond to disruption and build resilience to help them thrive.
Mnet: What technologies will be most impactful over the next year (ie: virtual reality, vision systems)?
Laaper: Deloitte’s 2021 Manufacturing Industry Outlook identified that 24 percent executives who plan to invest in digital technologies believe digital twin technology will be the most important technology in which their company will invest in 2021 (tied for first with augmented workforce efficiencies). Digital twin technology can help prepare manufacturers for the next disruptive event.
Mnet: How can smart factory technologies help address supply chain delays and issues?
Laaper: You can only manage what you can see. Visibility is likely to become the most critical capability for manufacturers both now and in the future. Meeting surges in demand requires visibility across the supply network as production ramps up. Not having a single part can derail the flow of assembly and manufacturers need nimble ways to multisource. The same holds true when managing materials and talent during a slowdown in demand. Trustworthy data with multitier visibility will allow supply chain leaders to identify risk exposure and proactively and strategically respond to emerging threats in a resilient and agile manner.
Similarly, with the manufacturing processes contained in a smart factory, organizations can have a holistic view across all processes, resulting in faster reaction time, more robust decision making capability, and less delays. Manufacturers can produce less scrap, more throughput, faster turnover and predict machine downtime well before it impacts production resulting in an overall increase in efficiency. We often see improvements in efficiency between 8-22% through a variety of digitalization efforts that compliment how humans and machines work together.
Mnet: How can companies use smart factories to test and learn before deploying large-scale technology changes?
Laaper: Smart factories provide a physical space to bring technologies together on a real shop floor and test them to solve specific business problems. Whether an organization needs to extend smart factory technologies across a network or pilot a single use case, they can see, test, and realize value before they make investments. Successful digital transformations also point to a need to consider user-oriented perspectives. Smart technology experiences can be highly customized to individual roles and how those roles may change.
Deloitte is convening a set of world-renowned solutions providers and technology innovators at The Smart Factory @ Wichita, to showcase smart manufacturing use cases in a real manufacturing environment. Organizations like Infor, ServiceNow, SAP, HPE, Tenable and many more are coming together with Deloitte to showcase the power of an Industry 4.0 ecosystem in a single, physical environment.
Mnet: How are companies of all sizes are implementing smart factory technologies today?
Laaper: Smart factory technologies are helping reduce manual tasks and improve the way humans and machines work together to drive down costs, increase supply chain efficiencies and better position their organization for success. The Smart Factory @ Wichita focuses on eight foundational use cases for companies of all sizes to leverage:
- Optimize the factory floor: IoT, AR and sensor-enabled monitoring predicts equipment issues before they happen to help reduce unplanned downtime and identify underutilized capacity.
- Smart warehouse: Smart warehousing solutions (AR, automated conveyance, cognitive dispatching) improve storage, accelerate shipping and right-size inventory levels.
- Boost warehouse mobility and availability: Autonomously guided vehicles and mobile equipment routing ensures the right material make it to the right place at the right time, while providing traceability throughout the process.
- Improve design, engineering and production: Digital twin simulations can show the impact of real-world variables to help perfect designs, production processes and forecasts/
- Make energy sustainable and affordable: Environmental monitoring, motion sensors, microclimate controllers, AI and ML pattern detection optimize energy levels in real time and reduce overhead costs
- Automate quality inspections: Vision systems, smart sensors and real-time analytic to accelerate inspections.
- Make operations agile and actionable: Leverage the power of cloud computing, AI and IoT to generate responsive and actionable build plans
- Reimagine the workforce: Employ an augmented workforce that integrates collaborative robotics, computer vision, intelligent automation, RPA and IoT devices to drive better outcomes and increase safety
Stephen Laaper is a principal at Deloitte Consulting LLP and a manufacturing strategy and smart operations leader in Deloitte’s Supply Chain & Network Operations practice. He helped build Deloitte’s Digital Supply Networks (DSN) methodology that uses existing and “next gen” technologies to drive efficiencies in operations and across the supply chain. Stephen is leading the firm’s Smart Factory services, including the 2021 opening of The Smart Factory @ Wichita, a groundbreaking, immersive learning environment for business leaders to experience smart manufacturing solutions.