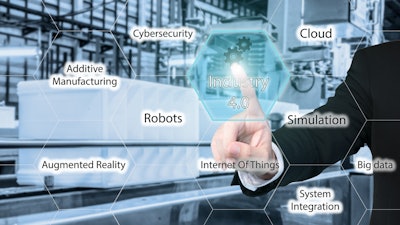
Change is never easy, especially in manufacturing, where tried-and-true business processes have run well for many years. But change is a necessity, now more than ever before. Technology has reached a transition point, one where powerful transformation sits at manufacturers’ fingertips. Companies need to understand the benefits, gain top management approval, set lofty goals, and execute to seize the opportunity.
Burned by such project experiences as massive ERP updates and migrations, manufacturers have been conditioned to focus on incremental technology improvements. And who wouldn’t after spending 12 months to deploy an enterprise planning tool, hating its latency, always questioning its accuracy and hoping that it’s going to get better tomorrow.
It never does.
This mindset is so acute, manufacturers are fearful of changing anything that might upset the delicate flow of information on-to and off-of the factory floor. This “we just live with it” model is broken when compared to the advances that technology offers them today. Companies are on the cusp of dramatic changes, ones that will transform their organization dramatically -- and for the better.
Vantage Point and Expectations
Any change obviously requires top executive team support. However, the reality is that the daily grind often requires so much attention that these executives have trouble finding time to poke their heads out to look at the big picture. Today’s possibilities are much different than they were even a few years ago. Technology improvements have come fast, furious, and are remarkably easy to implement.
Leadership need not concern themselves with the bits and bytes. They must realize that there are more efficient ways of creating and delivering their products, and it behooves them to give these non-disruptive approaches an opportunity to help their business.
In many cases, managers sift through Excel spreadsheets or sticky notes to understand how well a production run is performing. In some instances, employees spend large portions of their day on the floor gathering that data in order to have substantive discussions. Given the simplicity and accuracy of automated data collection, this is not only a misuse of high quality talent, but also a cultural burden that biases towards doing things the “hard way”.
Technology has evolved so that it can take on a lot of that work. To streamline operations, manufacturers must embrace digital technology, a catch-all term for modern solutions, like modular software, data analytics and automation. How it works is not important; it enables suppliers to get work done faster, more efficiently, and at a lower cost.
The “All or Nothing” game is a thing of the past.
For years, decision makers have been presented with technology proposals that require an entire upheaval of the factory in order to get the benefits. In 2020, software is modular and designed so that it can be additive and consumed in smaller increments to be successful. If it delivers value on say, five machines, it will deliver value on 500 machines.
The 4-5 digit economics of such an architecture are superior to the seven-figure ones of years ago. Today, this modularity requirement makes it to the top of everyone’s must have list. You control the pace of change within your four walls. You can consume new technology in bite-sized modular chunks. You make purchases that do not impact cash flow. As your margins increase, you buy more.
Manufacturers typically gather and leverage less information than they have at their disposal. Why? Often, devices have been added in an ad hoc fashion through the years.
Randomly connected sensors that automatically collect information that illustrates how well they perform, but that data is examined in a binary, superficial manner -- if at all. Technology advances have created an opportunity to holistically examine the entire dataset and correlate the information. Hence, a manufacturer flips the process and becomes proactive rather than reactive in overseeing its production runs.
Prove the Internal Skeptics Wrong
Top management support is vital because maximizing a company’s potential often means changing operations significantly. The first step is getting better visibility into your existing processes.
When implementing new technology, fear may arise. In some cases, employees feel that their livelihood is threatened. In some cases, employees feel a lack of trust. They view data collection as Big Brother watching their every move. The use of these tools empowers manufacturers, so the business expands and more work – and workers –are needed.
If communicated correctly, it can have a positive effect on building stronger bonds between people. The management team needs to emphasize how the advances ease rather than detract from workers’ workday. Proof may be required to convince skeptics, so you need to start the transformation process somewhere. Initially, avoid the most complicated parts of your operations, the ones involving multiple inputs from different devices overseen by various groups.
There is no need to boil the ocean on the first day. Instead, go for quick, easy wins. Pick a piece of a simple process with clear metrics. Think differently. Rather than try to squeeze a few more cycles out of something, focus on rewriting existing manufacturing processes.
Relax. The technology piece is simple. If a manufacturer creates a strong corporate culture, then employees will embrace the new processes. They will gladly trade in tedious tasks for stimulating ones. Once the pieces are in place, your organization operates in a more cohesive, fluid manner. Many potential benefits await:
- Gain real-time performance metrics, so you make necessary adjustments.
- Automate data collection and consolidation.
- Focus on increasing productivity.
- Improve quality.
- Ease the tedium burden on your employees.
- Improve communication, teamwork, and responsiveness
Manufacturing is undergoing a fundamental shift. A growing number of organizations are struggling to use technology for competitive gain. Companies need to adjust to realize the potential benefits. The process involves getting management approval, communicating effectively, starting small, and then thinking big.
Ultimately, if technology doesn’t give the organization the leverage to do more without the heavy lift of manual data collection, it likely isn’t worth the investment.