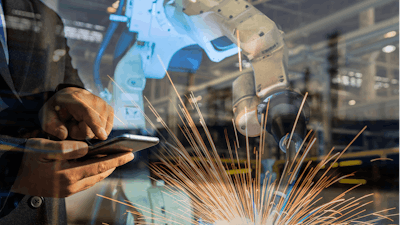
Though it sounds decidedly futuristic, the concept of a digital twin has been around for nearly two decades. It’s only because of the rise in Internet of Things (IoT) devices, however, that it’s now at the forefront of our collective conscious. As manufacturers continue to push smarter, and more importantly, cheaper, IoT devices into both consumer markets and industrial applications, it’s clear that the trend of building a digital double of a product, process, or even an entire assembly line, is going nowhere.
A digital twin is a digital representation, a clone, of a physical product or system. This could be something as small as a desktop speaker, or as large as an industrial plant that builds cars, manufactures clothing, or produces rockets for missions to space. Digital twins are even being deployed to study the design and deployment of tomorrow’s smart cities. The point is, if you can build a physical object, chances are you can build a digital twin for it.
As complexity grows, or the “things” we connect to the internet increase in number, the amount of data we produce grows with it. This data gives data scientists and information technology professionals all they need to build better, deploy faster, and iterate without shipping thousands of units, or spending millions of dollars on testing and repairs.
For a digital twin to be beneficial, it needs the data to drive decisions, decisions like when to make crucial repairs, how a system will react to small (or large) changes, and when (and how) we can expect parts within the system to fail.
In essence, a digital twin, when properly optimized, provides a digital version for testing and development. This saves time and money over designing, testing, and iterating on physical representations of the same product. From concept to launch, a digital twin could help get a product out the door in days or weeks, as opposed to months or years.
And once a company ships the product, digital twins allow them to use captured data to run simulations on everything from future improvements to likely points of failure. These points of failure could even be prevented, in some cases, with software updates, a preemptive warning made possible only through data collection and the use of digital twins.
Digital Twins at Work
According to a survey by Gocious, a software development firm that creates product planning solutions, more than 62 percent of manufacturers have preexisting initiatives to reduce product launch cycle times. For manufacturers, whether those making mobile phones, or smart cars, cutting the time of production even a few days could save tens of millions of dollars. But what about digital twin initiatives where measuring these changes in days is unacceptable, those where minutes matter, and not just in terms of dollars spent?
Healthcare, for example, is one of the most exciting places we’re seeing digital twin technology. If we think of the human body as an assembly line, you’ll immediately see the parallels between complex internal systems and the machinery we’d associate with the common factory. And much like a factory, scientists are using sensors to monitor patients, producing digital models that can be monitored by both doctors and AI to predict the best care options for patients. We’ve even seen digital replicas of organs, complete with data collected from real-world patients, that allow surgeons to practice complex procedures in a simulated environment, rather than on living, breathing patients.
Stara, a manufacturer of precision agricultural machinery, uses digital twins to analyze data that allows farmers to make accurate decisions and react quicker to elemental conditions, like storms, or environmental ones, like crop disease. The company has developed the sort of precision insights that let farmers react in moments to real world data by utilizing sensors in machinery that feed into a digital twin.
Singapore has even built a digital twin to study complex social structures and services throughout an entire city-state. Thanks to a mountain of real-time data, city planners can now test solutions without the time, expense, or risk of real world rollouts. In essence, Singapore has become a digital model of itself, an on-going test case and laboratory for innovation through use of data as a means to discover and implement large scale solutions.
Digital twins offer a peek at what’s happening in both physical assets and developmental or iterative processes. It’s a future where efficiency and planning are the focus, and one that everyone from Microsoft, to Chevron, and even NASA has fully embraced.
Digital twins not only reduce wasted time in product development, they save hours and dollars — millions of them, perhaps — in making manufacturing systems run as they were intended, with the efficiency and reliability of a well-oiled machine. Though it may not be well understood by the masses, at least not yet, it’s applicable across a variety of businesses, from healthcare and product design, to entertainment and manufacturing.
Digital twins are here to stay.
Maziar Adl is the Co-Founder and CTO of product decision analytics platform Gocious.