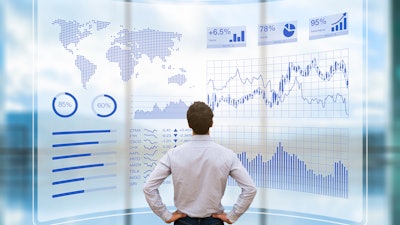
Manufacturing companies have reached an inflection point, a time where traditional business processes and metrics need to be overhauled in order to remain competitive. They rely on decades-old, analog building blocks not because they are efficient – they are not – but because they thought they had no other option. Well nowadays, they do: digital technology has reached a stage where it can eliminate manual data collection and provide real time insights into factory floor operations, paving the way for suppliers to shed inefficiency and burdensome practices that are holding them back.
Technology projects in factories are traditionally expensive and time-consuming endeavors. Many manufacturing business processes were forged decades ago, and are often just “lived with” in spite of their obvious shortcomings...
Given the typical complexity and limitations of technology, manufacturers have historically been slow to adopt new solutions. Their focus is always on creating and delivering goods on time and within budget, so tinkering with new technology introduces unknowns that could potentially have a significant negative impact. But the manufacturing paradigm changed dramatically since the turn of the millennium. Plants sprung up across the globe. Technology (cloud, mobile, digital) emerged, and the emphasis shifted from preserving existing investments to responding faster to market needs.
Moving forward, a change in mindset and a revamping of business processes are needed for suppliers to thrive. Manufacturers must acknowledge an obvious truth: their current systems are outdated and do not support the business as well as they must. They cannot wait until the end of the day or tomorrow to know whether the business is performing to plan.
They need that information as manufacturing runs are happening, so they can make necessary accommodations.
This desire for better information is not new. Manufacturers have been searching for solutions that provide such data for years. What is different today is that recent technological advances make this kind of information easily accessible and taking advantage of that change does not require a massive investment in personnel, an overhaul of existing systems, or a complex software consulting project. The building blocks are already in place; they just need to be tied together. Nowadays with the right vendor, the process can take days, perhaps a few weeks, and the investment is less than a new factory floor robot.
The Building Blocks
In the past, running applications meant that manufacturers needed to become technology experts. They had to buy, install, manage, update, and maintain their own infrastructure: servers, storage, and network hardware as well as software applications. No more. With cloud-based applications, software vendors absorb all of this complexity, and run the infrastructure securely for their clients.
In addition, software has improved tremendously, becoming simpler and more intuitive to deploy and use. With the right vendor, solutions can be as simple as point-and-click with no complex configuration, data input, or SQL queries.
Not only has it become easier, but it is also more functional. A big breakthrough has come in data collection. Factory machines have been instrumented to generate information and output it in a standard form. MTConnect creates a standard vocabulary for manufacturing equipment that provides structured performance data. Standard communication mechanisms, such as Wi-Fi networks, move that data from devices to a central location for consolidation and deeper analysis.
In sum, systems can be instrumented to generate, consume, and consolidate data. As a result, accessing real-time production information is often done with a simple click on a smartphone rather than a complex series of manual data entries. It is that simple.
Yet in many cases, manufacturers rely on Old School business processes. They house information in Microsoft Excel spreadsheets, and in some cases, bounce from station to station to collect performance information. Why? Such processes are woefully inefficient and hurt the business.
Now is the time to change. Embracing digital technology streamlines the manufacturing process and provides companies with real-time insights into production runs. With that data, corporations make necessary adjustments and reduce costs while improving productivity, quality, and yields, goals at the top of their priority lists. Deploying the technology to revamp legacy processes is straightforward, and the results are dramatic.
Why wait?
Greg McHale is the Founder and CTO of Datanomix.