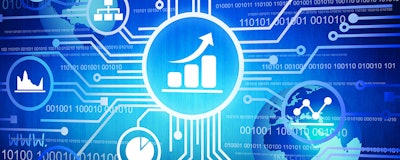
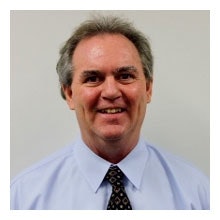
2017 may be remembered as the year we finally figured it out. For years, manufacturers have been investing in transformative industrial technology — and these past twelve months have been no exception. 2017, however, wasn’t about finding anything new, so much as learning how to apply what we have.
Machine sensors, for example, have been around for nearly thirty years. Yet due to a dramatic drop in sensor cost, the proliferation of these devices is finally empowering factories to use the accumulated data in all sorts of ways: MRP systems, work orders, parts management, business intelligence and much more.
As costs continue to drop — sensors once priced at $1,000 can now be had for as little as $10 — a critical mass of data is here. Even more, it’s estimated that by 2020, the amount of information available will increase as much as fifty-fold. At these levels, capabilities ranging from advanced predictive analytics to Artificial Intelligence (AI) will transform industrial production.
Beginning in 2018, we should begin to see a payoff in accelerated manufacturing efficiency. Companies are setting their sights on increased uptime, lower cost of goods, and higher profitability. Federal Reserve figures show that over the past 25 years, U.S. manufacturing productivity has grown 49 percent — and there is still significant room for growth.
As widely expected, the Industrial Internet of Things (IIoT) will lead the list of these enabling technologies. IIoT is only now beginning to bear fruit; IDC reports that globally, manufacturers invested $178 billion in IIoT technology in 2016 alone, with a compounded annual growth rate of 15.6 percent predicted through 2020. All that investment is about to pay off big.
The automotive industry is a bellwether for the benefits of IoT. Automakers have been experiencing both inward-directed (system optimization and cost control) and outward-facing (improved customer experience) improvements, and in 2018, many other industry verticals will be doing the same. Smart factories — facilities in which employees mainly operate systems and monitor activity — are expanding in number worldwide, thanks to IIoT.
The continued expansion of this revolutionary technology, however, will depend on use cases and business strategy. A new generation of technical workers will help, especially since universities are training business analysts who understand how to combine, understand, and leverage all the data that’s being collected. Still, without insights into opportunities for factory growth, many companies will remain cautious.
IIoT is not the only technology ready for prime time. Artificial Intelligence (AI) is beginning to make its mark in factory equipment. AI technologies are becoming simpler to connect, more reliable, and more acceptable. In particular, MRO (Maintenance, Repair, and Operations) is a discipline that will benefit from machine learning, ensuring that the right processes are in place for scheduled maintenance and that completed tasks are properly tracked and reported.
Overall Equipment Effectiveness (OEE) also increases with AI. As the number of sensors that measure machine performance and anticipate failures continue to appear, the opportunities will expand for AI to independently govern production.
Robotics, a third enabling technology, is nothing new — but its impact is mushrooming. In many places, robots are working hand-in-hand in the same cells as humans, thanks to new classes of robots that offer both dexterity and lifting capacity. In other industries — electronics is a prime example — products are often untouched by human hands until the end-user opens the box.
Some may consider this an unwelcome development. Yet this new era in robotics is helping offset the skills gap that continues to plague manufacturing. By filling a need at both ends of the spectrum, for tasks that are either tedious or highly complex, robots are adding even more value. Furthermore, in dangerous environments, autonomous vehicles and equipment — simply another form of robotics — have the ability to reduce injuries and even save lives.
Perhaps surprisingly, 3D printing does not make the A-list of manufacturing technologies. 2017 was good to 3D printing, and as costs continue to go down and new supporting technologies emerge, things may change. But as of now, 3D printing is likely to remain limited to product development and custom manufacturing, or as a means to resurrect obsolete repair parts.
As the world eases into 2018, many factors will support the continued investment in industrial technology including corporate cash reserves, solid consumer demand, and changing tax laws that allow for immediate write-offs of big-ticket purchases. A big caveat for all manufacturers, however, is to not spend blindly on technology. All too often, companies make tech purchases only to find, months or years later, that these “showcase” investments are, in effect, sitting on the shelf.
It’s critical to have a strong business case in place for any technology investment. Manufacturers need to establish accountability, assemble the necessary supporting technology, and plan for change. Most important is the need to instill a culture that accepts, appreciates, and leverages new systems. Technology, in and of itself, does not drive change — it only facilitates it. Without planning, the value of technology can diminish to nearly zero.
On the whole, however, 2018 holds real potential for technology ROI. Its ability to fill the skills gap, along with the maturation of supporting technologies, continued market demand, and newly-enacted tax incentives, all bode well for a huge step forward. With the right strategies and strong follow-through in place, 2018 should be the year in which technology takes its rightful place as the catalyst for a new era in industrial prosperity.
Mark Cox is Director of Advanced Systems for Advanced Technology Services, Inc.