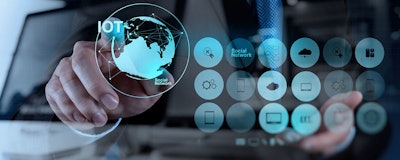
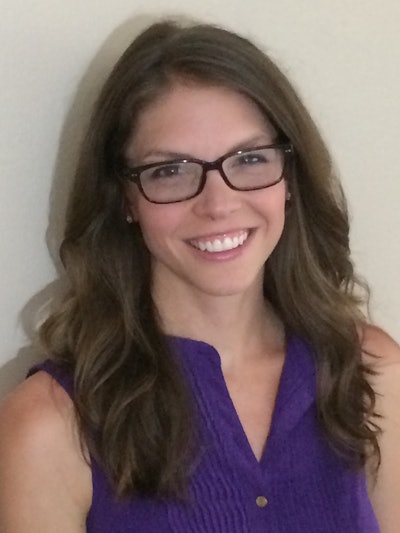
The Internet of Things (IoT) promises to be the most disruptive technological advance since…well…the Internet. Devices and equipment will be connected with sensors through which they can communicate and send alerts machine-to-machine without human involvement.
John Ragsdale of TSIA highlights the IoT as one of the top five areas impacting field teams: “Today’s increasingly connected technology creates opportunities for remote access, improving productivity and reducing onsite visits.”
The ability to put sensors in all of your tools and equipment can yield huge amounts of data, which can mean a total service operation redesign. Connected equipment and the influx in data will be especially transformative when it comes to how companies manage their preventive maintenance and customer loyalty programs.
For equipment manufacturers, dealers, and service providers, quality product support is fast becoming one of the most important after-market success drivers. With ever more sophisticated technologies, like IoT, service executives can take advantage of valuable data from smart, connected equipment and unlock the quality service programs today’s customers demand.
From Reactive to Proactive: How Connected Equipment Will Guide Preventive Maintenance Programs
Research has shown that manufacturers that maintain preventive maintenance (PM) programs out-earn those that don’t. Regularly renewable service contracts give service departments steady revenue they can count on, not to mention the customer loyalty these regular interactions with customers build.
By using IoT data, service organizations can shift their business model from reactive responders to proactive trusted advisors. In the past, if a machine broke, a technician would come and fix it, but there would be downtime. Now, sensors built into the equipment indicate when a repair is needed so it can be serviced before the machine goes down.
5 Practical Ways Equipment Manufacturers can Automate Service with IoT
IoT will impact how equipment manufacturers work in a number of ways. Here are a few examples to get ready for:
No. 1: Repair Equipment Before Problems Occur
IoT sensors in equipment signal when repairs are needed before problems escalate into more expensive issues. For example, rather than scheduling PM assignments in regularly scheduled intervals, service orgs can set parameters in equipment that activate a work order automatically. As the work order is generated, the system orders parts and schedules a preliminary service call. When the parts arrive, a service truck is dispatched to the site to perform the PM.
No. 2: Analyze Big Data
One of the biggest challenges of having access to smart, connected equipment is making sense of all the data coming from machines. The emergence of the cloud and IoT products built into machines make collecting and analyzing data easier and less expensive.
With the ability not only to collect machine intelligence, but also make sense of it, service organizations can offer customers advanced service packages that eliminate downtime. The best part? Every decision is backed by concrete data so manufacturers don’t waste time focusing on areas that don’t work or selling service contracts customers don’t need.
No. 3: Auto-Inspect Equipment
Self-diagnostics and reporting sensors make late or forgotten inspections a thing of the past. Instead of sending technicians into the field to conduct manual equipment inspections, techs can simply log into the equipment’s portal to inspect its performance levels remotely. According to the Zebra 2015 FSM Vision Study, 50 percent of companies now connect directly to equipment to service and diagnose it.
No. 4: Improve Scheduling Accuracy
With IoT sensors built into each part, schedulers can see who has which parts and use that information to make informed scheduling decisions so techs don’t waste time returning to the warehouse to get the parts they need.
Also, because schedulers now have real-time access to technician location and availability, they can optimize routing efficiency to get the right tech on the jobsite at the right time.
No. 5: Track Vehicle Fleets
By connecting your fleet of vehicles, you can collect information about how well a vehicle is functioning, which parts need replacing, and measure fuel efficiency and how aggressively techs are driving. Having access to this information allows you to instate company-wide driving codes, which not only improve technician safety and decrease the risk of accidents, but also cut down on the wear and tear of driving too aggressively.
Conclusion: Preparing for a Future Informed by IoT
While there are certainly challenges to IoT adoption and reasons to be cautious, we’ll soon begin to see (if you haven’t already) the benefits the industrial IoT brings to manufacturers.
If you can add effective service and maintenance programs to your manufacturing business strategy in addition to new equipment sales, you’ll soon realize the long-term benefits of building a satisfied and loyal customer base.
As equipment sensors and data intelligence become more sophisticated, insights and alerts from connected equipment and devices through the IoT will become the next standard in service. Will you have the tools and data intelligence necessary to meet that standard?
Joanna Rotter is the content marketing manager at MSI Data.