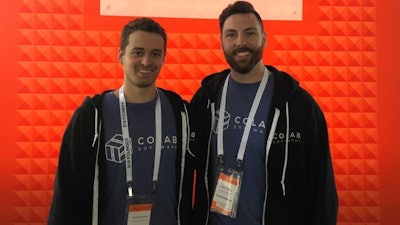
Engineers love to solve problems. That’s what makes them engineers. But you can’t fix something if you don’t know it’s broken.
That’s why the inspiration to create CoLab, a collaborative software for engineers, didn’t come from experts with decades of experience. It came from two millennial mechanical engineers who were seeing the engineering industry from an entirely fresh perspective.
The most innovative teams stuck with the least innovative tools
The year was 2016 and Jeremy Andrews had just begun a mechanical engineering internship at Tesla. He was working with some of the most innovative engineers in the world. But he quickly discovered that the tools available to the industry at the time weren’t on the same level.
Andrews was tasked with designing plastic injection molded parts for Tesla’s Model 3 Battery pack. As he started going through the Design for Manufacturing (DFM) process with a supplier, he was surprised to find that design reviews relied on collaboration tools that weren’t purpose-built for engineering and manufacturing work — even at an innovative, industry-leading company like Tesla.
The designs, created in CAD/CAM software programs, could not be easily shared with suppliers. PowerPoint and email were used to communicate issues and changes. “Essentially we had to constantly update and share the same PowerPoint deck back and forth,” recalls Andrews.
This led to versioning problems, and details that got lost in translation. Andrews — a millennial who had grown up with modern collaboration tools like Google Drive, Slack, and Asana — was shocked to realize that this was the design review standard across the industry.
“I didn’t have the historical context to think, ‘This is just how it’s done.’ And I couldn’t accept that mechanical engineers didn’t have a better way to collaborate,” he says.
Defining the industry-wide problem holding engineers back
Andrews began to consider the number of teams involved with design work on the Model 3. There were several parts (and thus several PowerPoints) he was responsible for, himself — multiplied by several more people on his team, then multiplied again by dozens of teams in the program as a whole.
With all those checkpoints, versions, and teams of people involved in the process, the opportunity for error seemed to grow exponentially. At the heart of the problem seemed to be three significant shortcomings of the modern toolset for mechanical engineers:
- Low-tech processes (emails, slide decks, spreadsheets)
- Slow review cycles
- Poor visibility for all involved
Andrews quickly discovered he was not alone. He reached out to fellow engineer Adam Keating, who was going through the same frustrations in his own experiences. And the more the pair looked at the industry as a whole, the more they encountered the same problem.
When the going gets tough, engineers start innovating
Engineers love to solve problems. So Andrews and Keating were stunned that fellow mechanical engineers were fine with this ongoing issue.
But instead of falling in line, the two decided to create a solution. They began with a CAD plugin, which would allow two people to edit an assembly file at the same time. That was great, but what really got fellow engineers excited was another idea they had — for something they first called a “design review portal.”
This portal idea would allow teammates, suppliers, customers, and other collaborators to review and comment on design files. It was the collaborative tool the industry had been sorely lacking.
The two knew they were on to something, and began to build on their initial successes. They created the company CoLab in 2017 and continuously iterated on the software as they spoke to more and more engineers about the problem. With each version, they built new features into the product based on recommendations from working professionals in the industry, such as a dashboard, reporting tools, and 3D presentation capabilities.
Not trying to “do it all” like the competition
CoLab launched version 3.0 of their software in March 2021 and, in doing so, the company finally felt like they had brought collaboration into the 21st century for mechanical engineers, designers, and manufacturing teams.
“The industry is dominated by giant players with complex, all-in-one solutions who aren’t really focused on the collaboration problem,” explains Keating. “CoLab is purpose-built for engineers, but it’s designed to be easy to use for anyone engaged in design.”
CoLab’s goal is not to replace CAD. They actually integrate directly with major CAD and PLM tools and support more than 60 different file formats. They view CoLab as a central hub where your CAD files can live side-by-side with design feedback.
The goal is really to reinvent the design review process, making it more agile and cutting out lengthy meetings, inefficient methods of file sharing, manual issue tracking, and other admin work. “The entire industry is 20 years behind software when it comes to collaborative productivity tools,” says Keating. “We are here to fix that.”
CoLab 3.0.CoLab
Growing fast and generating real-world solutions
The word is out about CoLab, and it’s coming from the types of heavy hitters that Andrews and Keating once worked for. “We’ve got some very interesting logos on our roster,” says the team’s head of business development, Taylor Young. “It’s very exciting to see the companies that are stepping up.”
One beneficiary of the improved workflow is Johnson Controls, which has already implemented CoLab for its Chillers team. In 2018, CoLab completed training with 8 users at Johnson Controls. Today, over 180 JCI engineers across 5 locations globally have used CoLab. (Here’s the case study.)
“With CoLab we have the ability to have various functional groups around the world all reviewing and commenting live or around the clock on the same exact model,” said Mike Zamalis, VP Global Chiller Product Engineering with Johnson Controls.
Success like this is the reason why CoLab’s team has doubled from 20 to 40 people in the last six months — and, considering this is an industry-wide problem, the potential for growth is enormous.
Ironic that the solution to an industry-wide problem should come from two mechanical engineers at the start of their careers versus seasoned industry veterans. But it’s also a lesson to all innovators: you might be trained in solving problems, but sometimes the most valuable skill is spotting the problem in the first place.
Learn more about CoLab, and read Jeremy Andrews’ first-hand account of the company’s creation.
This profile is a part of an ongoing series to expand awareness of the manufacturing industry from Winbound, a manufacturing marketing agency.