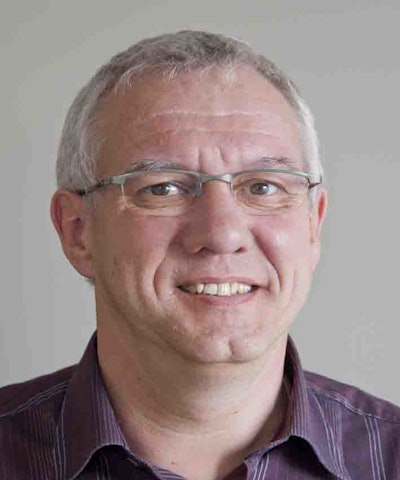
Developing new compounds and transferring them to production requires us to understand the chemical route, process and parameters—the sooner, the better. When applied in the chemistry laboratory, established calorimetry technology provides critical information to develop safe and scalable processes on a milliliter scale. Reaction calorimetry is helping researchers adapt, giving them an ability to meet their goal of safer scale-up at the speed of modern manufacturing.
As nearly any researcher or engineer can tell you, when working to bring synthetic reactions to production scale, a thorough understanding of the properties of reactants and reaction mass is essential. Synthesis workstations are playing a growing role in gaining this critical information in many manufacturing scenarios. Good workstation designs tend to be compact, easy-to-use, and capable of providing reaction specifics such as start and end point as well as events such as induction, indication of power of the reaction and accumulation of reagents, precipitation and crystallization.
From these basics, a number of conclusions are typically drawn to identify and eliminate certain scalability risks. Broadly speaking, a given process can be determined “not critical,” “potentially critical,” and “highly critical” so Go/NoGo decisions can be made earlier. This saves time, eliminates reagent waste (as well as attendant disposal costs), and avoids detours in later process stages that can eat project budgets and keep products off the market longer than expected.
However, engineers involved in transferring processes from lab to plant also understand the importance of determining thermal risk. This includes delving into the hazardous potential of a chemical process more precisely, adequately evaluating it for: heat or mass transfer limitations; heat release patterns that don’t match heat removal capabilities; sub-optimal processing temperatures; dosing profiles that result in reactant accumulation; or issues such as spontaneous precipitation, fouling or viscosity changes.
This additional level of investigation can go a long way towards helping researchers and plant managers save money by allowing these issues to be solved during development rather than forcing the company to bear the costs of reworking an at-scale process—or worse yet, an accident. This is where reaction calorimetry comes in.
What is reaction calorimetry?
Reaction calorimetry helps researchers evaluate the chemical process and gain reliable information about non-scalable conditions and potential risks. It does so in a quantitative manner and can more accurately characterize chemical process criticality. Researchers gain important opportunities to make the reaction safer at scale.
Using a specially-designed workstation, researchers measure the heat released from a chemical reaction or physical process under process-like conditions, providing the reaction’s thermochemistry and kinetics fundamentals. From a single experiment, crucial information such as heat transfer, heat capacity and release rates as well as enthalpy and conversion can be derived. Subsequently, details such as accumulation of energy, adiabatic temperature increase (ΔTad)and maximum temperature of the synthesis reaction (MSTR) can be calculated.
Most importantly, this information can then be used to create a “Runaway and Criticality Graph” (Figures 1 and 2. This data essentially lets researcher see the accumulated energy related to a chemical reaction’s hazardous potential and describe the maximum reaction mass temperature increase in the event of cooling failure. Action can be taken to change the reaction or ensure that there are sufficient safety precautions in place to contain possible undesired secondary reactions. Combining the information about the desired reaction with the data of the undesired reaction allows creating the so-called criticality graph presenting the risks of a chemical process graphically.
The importance of reaction calorimetry
In the face of recent plant accidents in several countries with significant manufacturing bases, the importance of obtaining the type of information offered by reaction calorimetry cannot be underestimated. If a process is potentially subject to unreacted reagent accumulation, for example, reaction control may be lost in the event of a cooling failure. Of course, this worst-case scenario can lead to runaway—with dire consequences for the plant and even surrounding communities.
Reaction calorimetry provides the ability to determine the heat flow rate as a function of the reagent addition rate, which in turn allows determination of whether the reaction is controlled by the feed (Figure 3) or if significant reaction accumulation occurs (Figure 4). Assuming accumulation is detected in a reaction that takes place in solution, reaction kinetics may simply be slow. Changes such as temperature increase, concentration shifts, different solvents/catalysts, etc., may increase reaction speed and reduce accumulation.
If the reaction mass is heterogeneous, on the other hand, the reaction may be mass-transfer limited. In this case, perhaps the stirring speed should be altered. In either case, reaction calorimetry can provide critical process-safety information before scale-up, allowing scientists and engineers to make appropriate decisions and create a robust process that ensures products are processed according to plant capabilities.
Determining true heat release
From an aspect of scalability, there is one more layer of informative data that can help ensure safety is maintained. Ideally, researchers need to know not just how much heat is released, but how it is actually released. To better understand this evolution, reaction calorimetry can also be used to analyze the reaction-mass temperature change caused by heat accumulation.
By converting the ΔT trend into heat flow heat removal as a function of time (orange trend) is obtained. Compensating for the heat of dosing (energy consumed by heating the added reactant) and integrating the curve between the start and end of the reaction provides us with the reaction enthalpy (ΔHr = -123.1 kJ/mol). Figure 5 shows the way the energy was flowing across the reactor wall with a maximum of over 400 W. Following the heat flow trend (orange) it also becomes clear that the reaction has a significant induction time and a huge accumulation (figure 5)
The basic fact is that when heat production is dominant over heat removal, temperature rises. (red trend in figure 5) However, once heat removal becomes larger than heat production, accumulation diminishes and stored energy is released into the calorimeter jacket to become zero again. (heat accumulation behavior is shown in figure 6)
Combining heat flow and heat accumulation information provides a window into a reaction’s true heat release patterns. For example, Figure 7 shows a reaction with:
1. large induction
2. Over 87% reagent accumulation
3. True heat release based on the reaction profile
As can be seen from the figures, the maximum heat release rate of the example reaction is not 400 W as suggested by the heat removal graph, but more than three times that amount at 1300 W. This is the type of information that can prevent dangerous runaway scenarios and is a telling demonstration of how reaction calorimetry can help identify reaction effects that would not normally be seen using standard synthesis workstations.
Safer, more cost-effective processes
Of course, the way to control a reaction depends on its scale and type. Generally, batch reactions are more issue-prone; a change to semi-batch or continuous flow may be desirable. Precipitation, adding solids or heterogenous systems in general can raise mixing issues. Changing temperature to reduce accumulation, reducing maximum heat output by altering the addition time, improving mixing or making changes to batch time can be identified as targets to improve an at-scale process.
Regardless of the ultimate fix, calorimetric information can help make sure reaction transfer from lab to plant is safe. Along with a chemical development workflow, it lets researchers reliably evaluate process risk by uncovering heat and mass transfer issues and allowing correct temperature, stirring rate, or dosing profile determination. It can also uncover unexpected events such as fouling or precipitation to further quantify scalability issues, leading to faster, more cost-effective research and safer at-scale production.