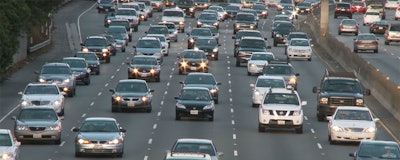
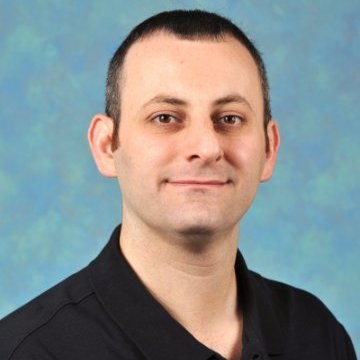
Our cars have become comfortable cocoons, seamlessly connecting us to our digital worlds, with the capability to stream our calls, data and text messages directly from our mobile phones. We are notified, in real-time, of traffic congestion and are offered guidance to alternative routes. Cars are being transformed into information centers, with their own operating systems and updatable software, through wireless connectivity to the Internet.
The primary driver of this technology is not simply luxury and information, but safety. This has resulted in IoT sensors within vehicles that monitor its own working parts, road conditions and even distance to objects around the vehicle. We have mechanical safety systems that auto-brake or engage the steering to help prevent collisions. And of course, we have the technology for a fully autonomous driving car. Today’s average high-end car has roughly seven times more code than a Boeing 787.
The Risk of Noise
But there are inherent risks to this “safe” technology. Inserting large amounts of electrical systems into the confined space of the vehicle compartment creates electromagnetic interference (EMI), or noise between each system. Noise has the potential to block safety-critical features from performing, which could result in risks for both drivers and their passengers. Noise is generated by simple user or vehicle actions things like flipping on a turn signal, and hearing a clicking sound on the radio, to adjusting the fan can cause a short-lived high-energy bust of noise. Noise is not always spiky in nature, it can also be as simple as increasing the entire vehicles noise floor when a device is turned on, when the internal combustion of the engine creates a repeating series of transient voltage events. When this combustion stops, the result is a complex, random pattern, involving many voltage spikes. And, simply activating the car’s horn creates widely spaced voltage peaks of extremely high amplitude. This increase in noise floor makes it harder for devices to differentiate between real signals and real noise.
Noise is far more common in today’s cars, primarily because of the switch to Ethernet, which gives engineers the faster speeds and bandwidth they need for the demands of IoT. Ethernet is replacing Media Oriented Systems Transport (MOST) and Controller Access Network (CAN), which were in favor over analog wiring in the 1980s, because of their lower costs, simpler implementation and faster speeds. However, CAN carries security limitations, and in the words of Tufts University computer science professor, Kathleen Fisher, is "hopelessly insecure" because of its inability to block unauthorized users and screen malware delivered over the Internet.
With the usage of more and more switching power supplies to power up devices used in vehicles to power electronic control units (ECU) that illuminate dashboards, in-vehicle infotainment (IVI) systems and powertrain components of today’s connected cars. The power supply circuits themselves are sources of noise in a vehicle. So the shift has also added fuel to an already noisy environment.
Accepting that noise is a reality, automotive network component and equipment manufacturers can take proactive steps to ensure electromagnetic compatibility (EMC) by testing for noise early in the design process. In addition to ensuring compliance with SAE and ISO, testing can help to pinpoint the source of noise and introduce systems to mitigate its impact and take corrective action early in development, before changes become too costly to implement. Take into account IEEE802.1CB — Frame Replication and Elimination for Reliability, currently there are no 802.x solutions to address fault tolerance without failover. This specification is first of its kind to address a seam-less redundancy for fail operational safety critical networks.
Noise can be fickle, often creating random errors that are difficult to isolate and even harder to pinpoint. Manufacturers who recognize this will approach noise testing with a protocol that uncovers the answers to these critical questions:
- Is noise present?
- When does the amplitude reach a level that impairs Ethernet signals?
- How long can the noise continue before impairment becomes unacceptable?
- How does the Ethernet system perform in the presence of multiple noise sources simultaneously?
- Is the system immune to the noise emitted by other systems?
- How well does the network recover?
- To answer these questions, these are the specific tests that can be performed to test the presence of noise levels: Link Quality Testing
- Noise Profiling Testing
- Packet Loss Testing
- Forced Error Testing
- Golden Sample Testing
- Redundancy Testing
- Arbitrary Waveform Testing
These tests are typically performed through the use of three types of tests, typically used to determine the causes and effects of electromagnetic interference: Drive, Chambers and Noise Generator.
Drive test. Placing the automobile under the precise operating conditions where it will be used can undoubtedly establish the safety and reliability of the automobile. However, when testing the systems and components of the Ethernet network’s response to noise, drive tests have a few limitations:
- Difficult to Isolate. Because it is impossible to precisely control the type, severity and duration of noise events in drive tests, making it difficult to pinpoint which noise event caused network malfunction or failure.
- Not repeatable. Without the ability to duplicate these conditions exactly, there is limited opportunity to correct the performance issue through repeated testing and measuring.
EMC Chambers. Commonly used for component and system testing, an EMC chamber has the advantage of providing a highly controlled environment. But there are two limitations to this method:
- Complex test set-up. EMC Chambers can only test the effect of radiated or induced noise, requiring a complicated test set-up. Measurements must be taken on all testing components to determine the level of noise generated for each event.
- High Cost. The high hourly rate of EMC Chambers makes it impractical for developers to use them for the extended time required to extensively evaluate, refine and test their prototypes.
Dedicated Noise Impairment Generator. Generators provide the ability to test under various noise conditions that are known, repeatable and reproducible. Test processes can be configured, modified and viewed via the generator’s PC-hosted GUI. Engineers can measure the performance of Ethernet networks at both the development and production stages, allowing them to pinpoint the timing and causes of problems. For manufacturers, there are several distinct advantages to this test method:
- Quick test set- ups, easy modifications
- Control: Real-world noise can be captured and injected into the Ethernet network in a controlled fashion.
- Repeat, Repeat, Repeat: Without additional set-up time and cost, network problems or failures caused by noise can be repeated and analyzed as the root cause is being identified and analyzed.
- Severity and Duration: Noise can be injected electrically, through reference cables and connectors, allowing precise control, as engineers gradually amplify the noise until they find the point at which the network fails.
- Aging and Normal Wear and Tear: Cars face intense temperature swings, contamination, vibration and shock, which can significantly impact the operating characteristics of vehicle components over time. A sophisticated noise generator will enable the test engineer to model the changing profile of devices’ noise output over time.
Customization: Users can extend the test and set benchmarks for the intended performance of the network.
While IoT advancements in vehicles have the potential to make the driving experience more enjoyable, these innovations, come with intricate electronic demands, making our vehicles far noisier. In many cases, this noise can hamper the safety and performance of the vehicle. The ultimate success of our connected vehicles is heavily dependent upon the manufacturer’s ability to manage and mitigate this noise. A Dedicated Noise Impairment Generator allows testing for precise, repetitive scenarios, designed to imitate real-world use can greatly benefit manufacturers. This insight can help discover the precise location of noise, mitigate its impact and make a correction to meet compliance before the vehicles roll down the assembly line.
Jeff Warra is Sr. Business Development Engineer at Spirent Communications.