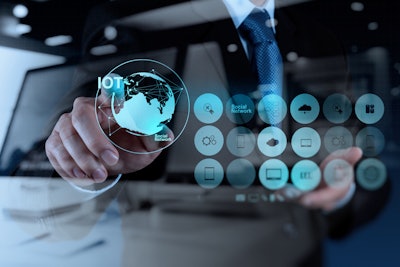
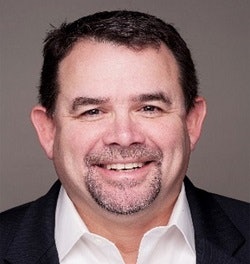
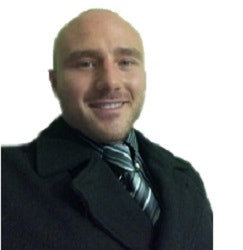
As we race through the final weeks of 2018, there is no doubt that the year ahead will bring both challenges and opportunities to discrete manufacturers. Uncertainty in the midst of volatile political, environmental and economic conditions can make it difficult to effectively plan until actual events or circumstances present themselves. However, there are macro-economic trends emerging, and manufacturers that take them into consideration will certainly benefit from preparedness.
As you look ahead to 2019, these five impactful trends should factor into your plans.
Trend 1: The Year of the Digital Transformation
While many manufacturers still rely on manual processes, spreadsheets, and legacy systems in at least some area, fully digitized operations are quickly becoming a “must” for those who wish to survive in today’s ultra-competitive, hyper-speed landscape. Manual processes and legacy data systems fail to offer real-time visibility into an increasingly complex global ecosystem of partners, suppliers and customers.
Consider these examples: in the case of a quality problem, it’s imperative that manufacturers are able to instantly trace compromised material, when it was used and in which products, and quickly communicate with all customers who received the impacted product. Or, when a piece of equipment is down, manufacturers can use technologies such as artificial intelligence (AI) and Internet of Things (IoT) to identify the specific point of failure in seconds, as opposed to hours. This level of automation is critical for operational efficiency and agility needed to meet the ever-changing demands of today’s marketplace. It also reduces costs by minimizing downtime, streamlining labor and reducing errors. If you have not started to plan a path to digital transformation, the time is now.
Trend 2: Shift to a Skilled Labor Force
The digital transformation of manufacturing coupled with an aging labor force is driving the shift from unskilled labor to technologically-savvy professionals. Highly effective, advanced robots will increasingly eliminate the need for lower level employees, a shift that requires a completely new approach to recruiting and retaining employees. Increasingly, manufacturers must be prepared to offer training and education programs that offer employees a career path, as well as perks and benefits competitive with companies in other industries. This will require an investment but will pay off in a manufacturer’s ability to leverage new technologies to reduce costs, improve processes and become data-driven decision-makers.
Trend 3: Optimization of the Partner Ecosystem
The days of “supplier, manufacturer, customer” are over, as supply chains are more akin to complex ecosystems of partners, suppliers, regional plants, logistics providers and customers. In a world of global trade, climate change, ever-changing regulations, natural disasters and fluctuating commodity prices, manufacturers must have multiple partners on-hand and working in harmony.
In 2019, manufacturers will return to reconsider and optimize their network of suppliers, distributors, and manufacturing facilities with a focus on service level. They will do so to gain market share and reap cost-saving benefits that can be realized with leveraged volume purchases, as well as to mitigate risk associated with volatility and unexpected supply chain interruptions. For example, identifying suppliers that can deliver scale with guaranteed service levels that have aligned values with the customer will be in high consideration to develop partnerships. These partnerships are driving higher value than suppliers who only offer lowest price paid.
Trend 4: Costs Will Rise
Commodity and raw material prices are rising in today’s strong economy. As the price of oil surges, so will operational and transportation costs. Manufacturers must be prepared to reap cost savings in other areas, including efficiency and labor savings. While inflation may allow some level of price increase, brutally competitive environments will force players to keep things lean. Efforts to lock in pricing, hedging or access multiple qualified suppliers and partners to offer competitive bids will be a worthy investment of time and procurement resources.
Trend 5: Increased Reliance on Operational Consulting Groups
As manufacturers deploy cutting-edge technologies, reshape their workforce and manage dozens of variables, they will seek the assistance of qualified third-party consulting partners for expertise and certainty. Given the scope and volume of change, internal continuous improvement teams simply won’t have the bandwidth to tackle every analysis, make every plan, develop expertise in every technology and implement the solutions. To help them sort through this overwhelming volume of critical decisions, manufacturers will look to the expertise of operational consulting groups to help identify and prioritize meaningful changes and investments, become data-driven, seek strategies and implement long-term sustainable operational transformation.
These trends are neither good nor bad, but simply represent the enormous and all-encompassing changes taking place in discrete manufacturing today and in the months to come. Start by assessing and prioritizing this list and determine if your operation has taken these factors into account.
John Pocock is a technical director and mining operations expert and Chris Gregory is principal and food and beverage/consumer packaged goods expert for Myrtle Consulting Group.