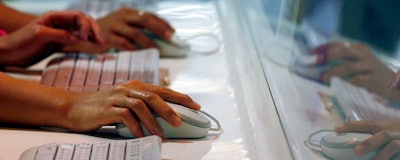
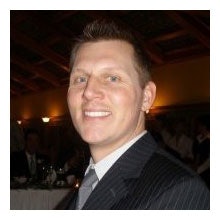
Modern manufacturing is an increasingly sophisticated interplay of human and material resources required to manufacture often complex products with tighter margins and shorter delivery schedules. As a result, manufacturing planning, control and scheduling have become more important than ever as a variety of materials and labor need to be seamlessly coordinated to meet customer requirements and evolving market demands.
Depending on the industry and product in question, there are a variety of production planning and scheduling mistakes that can befall manufacturers, starting with trying to plan production from a desk. Today’s sophisticated ERP software and powerful computer systems can lull production planners into a false sense of highly efficient production planning and scheduling security. Software flexibility and customization make it easy for planners to sit at a desk and think, “if I look at this screen long enough and make a few adjustments, our production schedule is going to work perfectly.” Nothing could be further from the truth.
To avoid production planning mistakes that can’t be seen on a computer screen, it’s important for production planners and schedulers to get out on the shop floor and interact with production personnel. An active presence on the shop floor enables planners to personally see what’s happening and double-check ERP calculations against the physical reality of actual manufacturing operations.
Following closely behind desktop production planning is not properly establishing capacity. Capacity is at the very heart of the manufacturing operation. If capacity is not accurately established at the beginning of the manufacturing process, all calculations are going to be wrong. To make it even more problematic, capacity is dynamic — machines go down, workers get sick, overtime needs to be figured in. All these things affect capacity and need to be taken into account to accurately establish it.
All production runs rely on routings, which are essentially the steps used to manufacture a product and their operation times. If routings are over- or under-estimated and run times are wrong the incorrect routings will adversely affect output. Unless accurate routings are established and implemented at the very beginning of production, inefficiencies will be an ongoing problem.
Many manufacturers, especially small-to-medium-businesses (SMBs), attempt to do production planning and scheduling with legacy systems or data manipulation tools poorly equipped for the task. For example, Excel is good for exporting reports and providing some data analytics, but it makes a poor production planning engine.
Any modern, integrated ERP system is able to process data, lay out a production schedule, and then provide a set of reports that will indicate any problems that need to be addressed. Good ERP systems that are fed the proper data will do all the math and produce an appropriate production schedule. It’s important for production planners to let the ERP system manipulate the data and provide scheduling answers so they can use their time to focus on solving problems. Attempting to do tomorrow’s planning with yesterday’s tools is doomed to be a lesson in frustration and failure.
Complex discrete manufacturing has a lot of moving parts, including high-performance machines that need considerable maintenance and fine-tuning. Ignoring equipment maintenance downtime for production is a common mistake made by manufacturers. While delayed maintenance may not cause immediate problems, sooner or later, left unaddressed, lack of maintenance will have a definite and negative impact on equipment performance and production.
If machines are out of calibration and not performing at full potential, production slows as workers struggle with inefficient or unreliable machinery, scrap and rework increase, and overall product quality suffers, all of which can adversely affect company growth and reputation.
In manufacturing there has always been conflict between production and maintenance and it’s easy to see why. Production traditionally wants to keep machines running while maintenance wants to take machines off-line for service so they can continue to operate at capacity.
Quality and efficiency are the cornerstones of profitable manufacturing and preventive maintenance is critical for enabling machines to operate at peak efficiency. If manufacturers want to improve performance and optimize productivity, it’s crucial to focus on preventive maintenance and find a balance between that and production.
Avoiding Pitfalls: Utilizing Effective Planning and Business Process Improvement
Efficient, effective production planning involves the intricate choreography of all manufacturing elements so that they come together in a cohesive, timely fashion to speed the production process along to a successful, profitable conclusion. For any manufacturing operation to reach its full potential, effective production planning most be at its core.
Production planning process improvement starts with three fundamental tasks:
- Providing production planners with adequate production-planning education
- Utilizing a “closed loop” manufacturing process that provides measurable results
- Implementing root cause analysis to help correct deficiencies
As a strategic planning methodology, business process improvement (BPI) enables manufacturers to streamline operational processes, improve access to information across departments and eliminate waste in all its forms. Done correctly, BPI also improves decision-making, as well as the management and utilization of assets and resources. It does all of this by identifying the business operations and employee skills that can be improved to make procedures smoother and workflows more efficient, driving business growth and profitability.
Incorporating best practices and regularly analyzing ERP data against a set of specific and appropriate metrics will go a long way in aligning production planning and scheduling, as well as generally streamlining manufacturing operations. However, by itself, the data generated by all the processes controlled and monitored by your ERP system is just information, not knowledge. Digitization and automation are helpful tools for gaining operational efficiencies, but human involvement is vital for turning information into insight and input into improvement.
To avoid the common production planning and scheduling mistakes we’ve discussed here requires proper planner training, engaged and motivated employees, appropriate ERP technology and the willingness and ability to undertake business process improvement.
Scott Jessup is a senior level consultant for Visual Business Solutions.