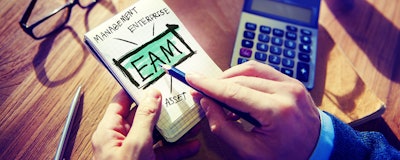
Many asset-intensive companies employ inefficient maintenance practices that cause increased downtime, reduced profitability, and added expenses. These methods can also lead to unreliable data that can lead to inaccurate forecasting and ineffective work planning, which directly affects operating costs.
Best-in-class organizations do not view maintenance as an overhead burden to be strictly controlled, but see the value that the tool brings to their company. Industry research has cited the following key performance indicators for best-in-class companies:
- +16 percent operating margin versus corporate plan
- 4.6 percent unscheduled downtime
- 12 percent decrease in year-over-year maintenance costs
- +14 percent ROA versus corporate plan.
Without the proper technology in place to monitor your assets, your company could be losing significant dollars. Best-in-class firms have been able to maximize equipment uptime and should failure occur, these companies are better equipped to solve the issue compared to their peers. These advantages are due to the implementation of an Enterprise Asset Management (EAM) solution. Realizing that maintenance can contribute to the company’s financial success is the first step towards elevating your company towards best-in-class status.
For some companies, the status quo is acceptable. Profits are good, equipment is running, and employees are working. These three areas are where an EAM has the most impact, and here are three reasons why your company may not need to invest in this solution.
Reason No. 1 to NOT Invest: Profits are Good
One of the main features of an EAM solution is the ability for it to control maintenance costs and improve overall operational efficiency. Being able to plan, estimate, schedule and complete maintenance work on-time is the main component that keeps cost under control
According to industry research, profitability is top of mind for almost all companies and as a result businesses are also looking for ways to reduce their spending. An EAM solution would be able to schedule preventative maintenance that can prevent costly issues from developing, thus money that would be spent on repairs can then be allocated to different areas within the firm.
If overtime costs and downtime interruptions are manageable, and your operations and maintenance costs are within tolerance, an EAM may not be the right investment for your organization. However, in business there is always room to improve, and an EAM solution may be the upgrade that your company needs to make.
Reason No. 2 to NOT Invest: Equipment is Running
An additional benefit to investing in an EAM is the security of knowing your equipment is well monitored and correctly maintained so that you can get the most out of an asset. According to an Aberdeen research survey, the need to maximize Return on Asset (ROA) is the second highest pressure, and the issue of aging assets is not far behind. The failure of critical assets was also a major pain-point for many respondents.
Companies operating on a reactive maintenance strategy typically see 70 percent efficiency. Many best in class organizations have shifted to the predictive maintenance approach, and as result their efficiency range is 90-95 percent. As assets age, maintenance need change. The plans that were in place years ago may no longer work quickly enough for downtime to be avoided, and can lead to your company having significant costs.
If your company is certain that assets will last, and in the event of an emergency, maintenance technicians have the right parts, in the right quantity, at the right time for needed repairs, then an EAM solution may not be appropriate for your organization.
Reason No. 3 to NOT Invest: Employees are Working
Every company needs qualified employees are to ensure that production runs efficiently. Due to the shortage of skilled tradesmen, concern over the attrition in the workforce has increased over 200 percent in recent years. As more and more senior personnel retire the “tribal knowledge” that they possess about an asset is lost. An EAM solution organizes and stores that valuable information of personnel who have been in the industry for decades.
By implementing an EAM solution, best practices will be standardized and documented for new employees coming into the organization. With the wealth of knowledge available through the EAM, safety risks are minimized and costs of downtime or production errors are significantly reduced. With an estimated 10 million baby boomers retiring by 2020, best-in-class companies are addressing the talent gap and taking advantage of the assistance that technology can provide.
Conclusion
Although an EAM solution may not seem like a necessary investment, the benefits this technology can greatly impact the profits, equipment, and employees of your company. Many best-in-class companies have already invested in an EAM and are now looking for new ways to improve their systems. By not investing in this valuable tool, your organization runs the risk of falling behind the competition.
Richard Adams is Regional Account Director of Aptean TabWare EAM.