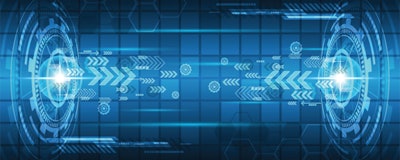
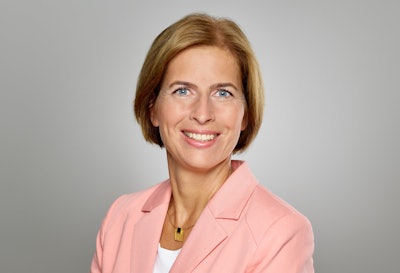
Gartner named the concept of a “digital twin” one of the top ten strategic technology trends of 2017, predicting that within three to five years, they will represent billions of physical assets, systems or processes.
At their cores, digital twins bridge the physical and digital worlds. They typically integrate artificial intelligence, machine learning and software with analytics to create living digital models. Pioneered by NASA, the concept has been around for nearly 15 years. Until recently, however, digital twins have been used primarily by design engineers. Now for the first time, they can be brought to life in an operational context. This is primarily due to the growth of the Internet of Things, which has made digital twins much more cost-effective and easier to implement.
Today, there are many scenarios in which digital twins can be effective change models for business operations. According to IDC, companies who invest in digital twin technology will see a 30 percent improvement in cycle times of critical processes by 2018. In addition to speed, digital twins have an enormous play in asset and performance optimization.
Asset Optimization: A Virtual Health Check
Digital twins enable real-time information feeds on how equipment is performing. As virtual representations of assets, digital twins obtain insights into how existing equipment, processes or products are performing over time, enabling companies to actively track the health of their assets. This can be especially helpful in business scenarios in remote and hard-to-reach places, as digital twins can monitor the health of an underwater drill, pinpoint areas of stress and make necessary adjustments — all without on-site attention.
For example, Artic Wind, Norway’s most northern wind farm, is leveraging digital twin technology to monitor the health of their wind turbines. These turbines require constant monitoring, but maintenance is extremely challenging because of low temperatures and extended periods of darkness. To combat the elements, they’ve installed sensors on their wind turbines. The sensor data is then transported over 1,000 miles away, where it can be analyzed in a more comfortable and accessible environment. That data feeds a digital twin in real-time, enabling employees to visualize any structural stresses as they happen. It also provides the company with future prognoses, which enables employees to run simulations of how the turbines will perform in an upcoming storm, for example, so they know whether to shut down operations or not.
Manufacturers and operators are now able to optimize the design and operations of a wide variety of industrial assets. This is key for the development of new prototypes. Previously, designers had few opportunities to change their prototypes during the process. Now this can be done at any point in the product’s lifecycle, leading to a faster time to market. Considering the value of design optimization in customer satisfaction, improved efficiency and cost-savings, this is of incredible value.
Performance Optimization and Predictive Maintenance
While there is no denying the importance prescriptive maintenance or physical inspections can have for improving the reliability, operational excellence and safety of machines and processes, they don’t always happen. However, digital twins can reduce the need for a physical inspection and replaces it with a “digital inspection.” Maintenance checks can be done regularly and efficiently, helping ensure that equipment is functioning at its highest quality with reduced maintenance costs, increased asset availability and improved customer satisfaction. This helps companies avoid any production downtime, decrease lag time and ultimately improve business continuity.
Practical use cases extend beyond the manufacturing and supply chain industries. Insurance companies, for example, are responsible for ensuring the proper operability and safety of machinery. Digital twins can help give companies peace of mind that equipment is being constantly monitored so adjustments can be made in real-time, improving the reliability of the assets.
Digital twins are quickly becoming a business imperative and have the capability of completely transforming and creating new business models. With the ability to integrate information pulled from sensors, digital twins are enabling more informed and strategic decisions. Prior to digital twin technology, data was hard to pull and analyze, prohibiting actionable insights from being achieved.
Now, the most talented minds have the opportunity to leverage unprecedented levels of data, while using progressive monitoring and predictive capabilities. When combined, the opportunities are endless.
If Industry 4.0 is to become a real success, the digitization process needs to permeate all stages. When digital twins are integrated into other systems such as order taking, resource planning, asset integrity management or product lifecycle management, manufacturers can completely revolutionize the way they work. One day, we could very well see entire virtual factories that mirror physical ones.
Tanja Rueckert is President of IoT and Digital Supply Chain at SAP.