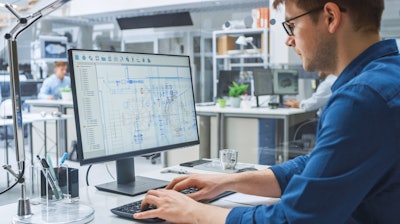
Manufacturing industries are steadily migrating away from traditional manual entry, siloed processes for managing design and production. Taking their place are highly automated, more end-to-end digital methods of collecting and sharing information. These increasingly holistic approaches largely center around using PLM to interlink digital design data with downstream activities such as ERP and MES and ideally back again to design.
While such major, independent systems are more interconnected than ever before, it is also clear that PLM, ERP and MES platforms suffer from their own silo issues as they strive to address the highest customer priorities first. Those priorities may focus on dedicated, central tasks of inventory and order tracking in ERP rather than fostering integrations between platforms where rich design data can inform a factory floor simulation or help with material substitutions or costing.
Today, it is imperative for businesses to close these gaps.
Call for greater reach and automation
The industrialized world has faced a severe supply chain crisis that is only easing now. One clear answer, aside from improving product transportation, is to make industrial supply chains faster and more efficient digitally.
Companies already have the data in their existing CAD, PDM, ERP and MES systems. Now, they must mine these systems, make that data readily available and seamlessly usable in other domains, such as CRM, and then apply this domain information in flexible, targeted ways to their specific product and business needs.
With human workplace productivity approaching its limits, the next productivity frontier is optimizing the enterprise. Specifically, the industry needs to cut product development and production cycle times at the organizational level and focus on implementing deeper and broader automation within existing automation platforms and related toolsets.
The goals? Automate out human error caused by manual data entry. Make platforms and their downstream and upstream integrations run hands-off. Cut process and wait times. Construct fast, decision-aiding software processes that allow various disciplines to see and learn from each other. And simply be able to work with greater concurrency and foresight.
How does this translate?
There is a need for more awareness on how to improve large- and mid-sized enterprise platforms. Large platforms, for instance, do not always work well with industry-specific, Best-of-Breed (BOB) outside software. The workarounds are slow and delay concurrency. Users of both systems often do not realize the localized benefits to connecting fully with the organization. Their job responsibility and rewards are departmental. The upstream or downstream connections are not fully automated and seem laborious.
Mid-sized companies may lack true operational oversight or enterprise-type managers. But if we see our organizations as mechanical transmissions with various tightly connecting gears—and they are when running at their best—then concurrency and visibility are the oil that keeps everything moving. Orders get facilitated, throughput meets demand, and quality improves. Engineers can be engineers instead of clerks and checkers. Personal productivity can improve. Ultimately, operations run more smoothly, quickly, and profitably. These are good reasons for buy-in.
There is a mistaken belief that large platforms do everything—or, respectively, that custom add-ons are too expensive and narrow to fill the gaps for smaller, highly focused companies. Inevitably, practitioners pick according to their prime needs: the best ERP or MES or CRM and fill in around those tools, perhaps with a suite of BOB software.
A main complaint heard is, “My enterprise system is not purpose-built. It’s not for my industry. It’s not doing the sort of things I want to do. PLM and PDM is a big enough piece of my business that I need something that fits to them.”
So, second and third systems for purchasing and production departments are added, and the need for more integration and automation becomes paramount.
Middleware solutions turn the gears
Rather than deploy experts in multiple systems to create dedicated yet narrow, separate connections, manufacturers can now turn to leading third-party integrators for broad, holistic solutions that improve speed and conformity. This uniformity is important when primary systems have upgrades. And it is critical for concurrency and smooth functionality across disciplines.
The gains from this kind of agnostic integration of major platforms can be eye-opening.
Now System A and System B and C talk cleanly in a hub-and-spoke manner. The hub, or middleware, understands the rules, priorities and standards needed across systems. It automates the exchange, is cooperative by nature, knows where data belongs, and extracts and delivers it in the right format, avoiding manual data entry and human error and reducing associated costs.
This diagram illustrates a hub-and-spoke data-integration model where the hub handles all the automated process task plans, with push-pull data handling to move data to the right system based on the automated task plan.Razorleaf
Different systems, be they ERP, MES or CRM, handle data in separate ways and use different application programming interfaces (API). They come with unique data entry limits and configurations. Here, stringed workarounds of code do not improve enterprise back-and-forth. Middleware, with its larger, neutral strategy for reliability, reach and automation, does.
From PLM to CRM
The middleware approach excels in cases where each department needs to know the progress of another before product stage-gate releases. With convenient transparency, downstream entities such as production and inspection can review evolving designs, provide feedback, and begin their own ramp-up for tooling purchases and line-inspection equipment. Production is better prepared for First-Article-Inspection (FAI) and follow-on preparations. Purchasing can price out materials and be aware of the in-progress Bill of Materials (BOM). There is more notice to head off bottlenecks and supply chain delays. Time is saved, and product goes to market faster.
Even further downstream, when Customer Relations Management systems receive a custom order, response is better focused. Can the product be reconfigured to the alternate spec? Are parts available, and how many? When can these be delivered, and at what cost? Engineering gets alerted to the added work, as do other departments. Any stakeholder can react, and the silo walls are lower because taking clear actions is easier.
In the same vein, a mature product may be at the end of its lifecycle. Folks in sales want to know what the parts stream can support in terms of shipped goods. What’s in stock? Are any reorders needed? What do the suppliers say? Can quantity deals be made at lower costs? What are the gaps if any before the new product is available? A tightly connected enterprise from PLM to CRM will have fast, accurate answers. An integrated middleware hub has avoided the downfalls and disparity between platforms by allowing each system to speak and share vital data.
The same portability is true for whole Technical Data Packages (TDP). Each supplier may have its own internal delivery standards and added requirements from the OEM. Hub-based programs help internal or other groups properly configure deliverables from the CAD, BOM, and quality programs to outside or downstream recipients, including regulators.
Advanced middleware integration platforms maintain task plans to handle data event triggers, like an item quantity update, and then executes those plans. Other task plans can include parts and BOM changes, ECO processes, issue tracking and more.Razorleaf
Knocking down digital walls
We need to be frank about productivity and the limitations of general-purpose platforms. There is too little incentive for team members to collaborate when clerical tasks are difficult, time-consuming, and only partially effective at that. As an industry, “throw it over the wall” is still in play. The walls may be lower and more digital, but they are walls nonetheless. And with less staff, more work, and greater time-to-market pressures, 2024 can feel a lot like the 1980s.
Here is where recognition of the problem and its opportunities will allow us to leap forward. Agnostic, third-party middleware can stand outside the fray, listen to users as they are best suited to do, and provide the functional automation that completes the promise of existing automated platforms such as PLM, ERP, MES and CRM.
Better integration is not only possible but already in action today. Our workplaces and supply chains will benefit from the deployment of these middleware pathways that tighten the digital and cultural gears that make up a smooth-running, responsive, and profitable organization.