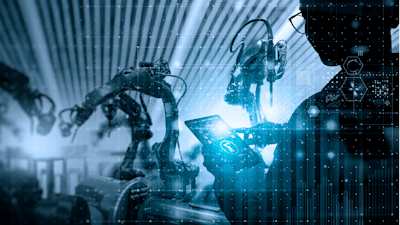
For manufacturing businesses, the pressure to do more with less has never been greater. As they look to technology for answers, where do they begin? We sat down with Amit Patel at Emerson for some insight on the company’s “Floor to Cloud” approach – a technology stack designed to enable the factory of the future.
Patel has been with Emerson since 2017 and is a Director for Digital Transformation (DX). He focuses on driving the marketing direction and executing intelligent hardware and software solutions across the Discrete Automation business. Amit earned his Bachelor of Science degree in Electrical Engineering from The New Jersey Institute of Technology and holds a Six Sigma Belt for Process Improvement using statistical methodologies.
IEN: Would you please describe what a Floor to Cloud approach is? What are its key elements and/or steps?
Amit Patel: Floor to Cloud leverages Emerson’s technology stack of sensors, automation hardware, edge and industrial software. Combined with our application expertise across discrete manufacturing, Emerson enables the factory of the future by giving manufacturers real-time visibility, insights and control over their operations. It starts on the factory floor where sensors unlock trapped machine and process data across devices, machines, production lines and plants. Then hardware and industrial software, such as edge analytics and SCADA software, translate data into valuable insights that scale in the cloud. Manufacturers can use those insights to overcome challenges and capture value at scale to achieve their goals.
By looking for areas of opportunity to improve overall equipment effectiveness (OEE) and save energy, manufacturers can deploy intelligent solutions that let them clearly see what is happening with their machines and processes in real time. With this visibility, they can see inefficiencies and potential issues and quickly make decisions and take actions to address them. By continually engaging in this process of optimization, manufacturers can increase machine availability, reduce waste, improve safety and reach new levels of performance that set them apart from their competition.
IEN: What makes a Floor to Cloud approach different from other approaches to factory automation and digital transformation? What benefits are unique to this approach?
Patel: There’s a vast range of digital maturity and expertise across manufacturers and industries. Manufacturers are often burdened to figure out where to start or are aware of a known problem but don’t know how to leverage the right technology and justify the investments. In comparison, a Floor to Cloud approach starts by considering a manufacturer’s known challenges and goals as well as its existing capabilities. Using this level of understanding, manufacturers can develop and deploy a comprehensive, scalable solution that can solve multiple challenges at once, continuously optimize operations and deliver quick return on investment (ROI).
A Floor to Cloud approach demonstrates in its name the range of expertise and technology it offers a manufacturer – under one roof. Only a diverse team of experts with a comprehensive portfolio of technologies, from sensors and devices to software, can create a tailored solution that addresses a manufacturer’s multiple challenges and goals regardless of where they are in their digital journey.
IEN: Is this a one-size-fits-all approach, or can it scale according to a company’s needs, size and stage of digital transformation? Is it only suitable for new installations, or can it be applied to existing facilities?
Patel: The range and reach of the technology stack from a Floor to Cloud approach and its consideration of a manufacturer’s existing equipment and capabilities makes it ideal for companies of any size or stage of digital transformation as well as facilities new and old. Floor to Cloud solutions are modular and deployment is flexible within a manufacturer’s existing environment and automation layers. This allows for a scale and level of customization that makes projects more manageable and reduces the intimidation that some can feel when making digital investments. In fact, at Emerson, we tell the manufacturers that we work with to start small, prove ROI, scale fast and maximize value.
IEN: Are there specific industrial applications that a Floor to Cloud approach is particularly beneficial for?
Patel: The value of digital transformation and a Floor to Cloud approach is that they can impact a variety of areas within a plant, from improving machines and reducing utility use to streamlining processes and empowering staff – all at the same time. For instance, as labor shortages and stretched workforces continue, real-time, remote monitoring and alerts can replace manual tasks, and detailed insights and guidance from software can address skills gaps. As personnel quickly address potential issues, they optimize equipment and processes. Smarter, optimized equipment and processes improve productivity (OEE), which can increase availability performance and improve product quality.
As sustainability is a top priority, there is a significant push to reduce waste and inefficiencies by optimizing plant infrastructure, machines and lines to be more energy efficient. A Floor to Cloud approach allows manufacturers to monitor resource and energy use in real time, and quickly identify and address waste and inefficiencies. In this way, manufacturers can optimize utility consumption, including compressed air, water, gas and electricity. For example, compressed air monitoring can reduce compressed air use by 20-30%, saving energy and reducing carbon emissions.
IEN: How can companies begin or continue to digitally transform their facilities using a Floor to Cloud approach?
Patel: Manufacturers can start wherever they are, according to their goals and needs. They can identify one area of opportunity, like monitoring compressed air consumption of a specific machine, deploy the right sensors and local analytics, prove the value and use case and scale up. Or they can transform across an entire facility or enterprise all at once.
It’s important that companies have a vision around how information technology (IT) and organizational technology (OT) will connect. OT encompasses the physical and operational systems while IT encompasses the digital systems. Both need to align around the types of communication, networks and infrastructure needed to enable and scale digital transformation projects. Edge technology, for example, localizes insights and data on premises rather than sending it to a remote or off-site server. This localization allows for projects to start small and scale fast when needed.
IEN: To remain competitive, many companies today must achieve much more with less. How can applying a Floor to Cloud approach to factory automation and digital transformation affect a company’s productivity?
Patel: Using a Floor to Cloud approach, manufacturers can improve productivity by maximizing the equipment and personnel they already have. By continually optimizing machines and operational processes, manufacturers can minimize downtime, improve OEE and achieve ever-higher levels of productivity.
In addition to addressing issues, manufacturers can ensure that equipment is running as effectively as it can down to the device level. For example, intelligent compressed air monitoring can allow manufacturers to balance pneumatic devices, like actuators. Pneumatic devices have an optimal ratio of pressure to airflow. If that balance is off, processes can waste energy or result in product quality issues. When this ratio is balanced, processes run efficiently.
IEN: High turnover and an inexperienced workforce continue to affect operations at many companies. How can this approach address skills and labor challenges?
Patel: A Floor to Cloud approach can help ease labor and skill set challenges. By design, it puts the right knowledge in the hands of the right person at the right time, regardless of their experience and skill level. Since digital transformation requires collaboration between humans and technology to realize and capture value, this is a key opportunity.
Consider intelligent compressed air monitoring compared to manual testing for compressed air leaks. Manual tests are time-consuming and often require knowledge learned through experience, such as listening for leaks. In comparison, smart sensors measure pressure, temperature, humidity, moisture and more to help operators see what’s happening in their compressed air circuit in real time.
Once pneumatic sensors create data, an edge device aggregates the data streams and pushes it to software. The software then contextualizes and presents insights on a dashboard and sends personnel notifications a leak is detected. Operators receive detailed alerts that tell them what to check and do as well as view the dashboard to understand trends, diagnostics and statistics that can help them make informed decisions. Depending on where sensors have been placed, analysis can describe compressed air behavior for a given line, factory or an entire plant.
Aiming to digitize manual processes or create the right data on the factory floor to deliver actionable insights empowers a manufacturer’s workforce to make data-driven decisions. Easy-to-use, modular industrial software, such as PACEdge and Movicon from Emerson, allows operators to visualize and monitor a plant, factory floor and/or machine and make informed decisions that result in meaningful action.
IEN: Many companies are committing to net-zero emissions targets, and digital technologies are proving to be an effective part of corporate sustainability strategies. How can this approach help companies achieve sustainability goals?
Patel: A Floor to Cloud approach allows manufacturers to monitor real-time utility use as well as trends over time. Using this information, manufacturers have a clear picture of resource use and the information they need to develop strategies to reduce it. Since it is used in a wide range of factory types and applications, compressed air is a key area to begin and see immediate results.
On average, factories dedicate about 30% of their total energy use to generating compressed air. However, up to a third of it is wasted by leaks and process inefficiencies. By monitoring compressed air in real time, operators can quickly receive information that helps them detect and address leaks much earlier and significantly reduce energy use and related carbon emissions. Once they’ve optimized compressed consumption and proven ROI, manufacturers can scale to other forms of media, including water, gas, electricity and steam.