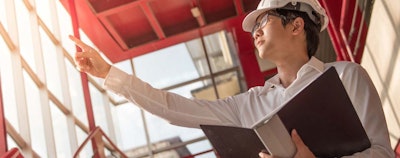
It’s a myth to think that you need expensive software-based solutions or pricey consultants to create your safety management system (SMS). For some businesses, the safety management system is as simple as a spreadsheet or paper-based tracking, while other companies use custom software. But the method you apply to ensure compliance and identify and correct hazards is your safety management system and it’s unique to your business.
Below are three real-life examples of various company SMS (names withheld):
Company X
Company X is a manufacturing firm and have been in business for twenty years in the plating industry. The Company employs 150 workers and experiences minimal employee turnover. Most of their employees have worked there a decade and are aware of hazards through regular training sessions and years of experience. It is a healthy company and a stable environment, with little change in processes. The Company EHS tracks compliance and training requirements through spreadsheets. She and the plant manager conduct incident investigations for each report, as well as safety audits and annual JSAs. Management is given a copy of the reports and follows-up to ensure corrections of any hazards are finalized.
Why does this SMS work? The safety management system at this company depends on reliable processes and experienced employees, along with a dedicated management staff who have been monitoring compliance for decades.
Company Y
Company Y is a new and growing business in the orthopedic device manufacturing industry. The Company owner is part of daily operations and steers the safety and health program with his management team. Eighty full-time workers are employed currently, but the Company anticipates a twenty-five percent growth rate in the next two years. A Company safety committee investigates incidents, as well as monitors new processes and equipment purchases to ensure hazards are identified and abated. The Company developed its own software to manage the safety and health program, which assists in applying training requirements to each new and existing worker, and aids in maintaining documentation of hazards and job assignments.
Why does this SMS work? Growth in the company could expose workers to novel hazards, but risks are well-managed by a team of safety committee members who examine each process and piece of equipment. Company-specific software allows for flexibility as the business matures.
Company Z
Company Z is a business engaged in aluminum recycling and have been operating for over a decade. They employ seventy-five workers and run shifts twenty-four hours a day, seven days a week. Supervisors meet weekly to discuss the plant operations and safety considerations with the management and EHS. All supervisors have the authority to immediately correct serious hazards, but must document the issue and the type of abatement. The Company EHS uses OSHA’s e-tools to assist in creating and modifying necessary written programs and a paper-based system for incident reports and tracking. Risk assessment and training are conducted by the Company workers’ compensation insurance agent. All hazard corrections are signed off by the EHS, as well as a member of management.
Why does this SMS work? Clear communication and defined roles in the safety program allow for a very straightforward SMS.
You’ve Already Got An SMS. Now Make It Work For You.
It’s likely you’ve already found a style to manage your compliance issues and have SMS that fits the needs of your business. The commitment your company applies toward managing health and safety is what defines SMS, not the cost of a product.
This article originally appeared on Grainger's The Safety Record website here.