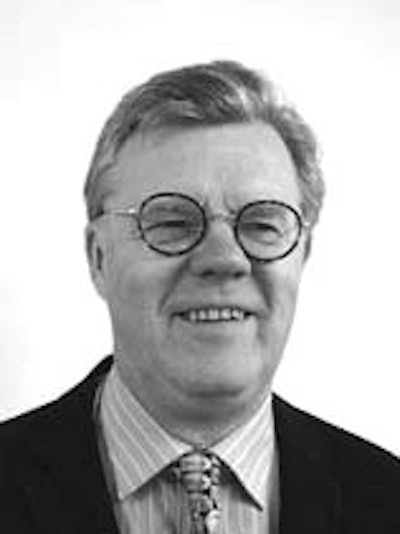
Establishing a truly maintenance-oriented culture is so often easier said than done. IMPO sat down with Jarmo Heinonen, Vice President Group Service Development Manager at Quant, to discuss how culture change can take effect in a manufacturing setting, and how the results can impact overall performance. Formerly ABB Full Service, Quant is considered a leader in the provision of professional industrial maintenance services with a global presence. Jarmo has almost 20 years of experience in industrial maintenance management. His areas of expertise include strategy development, implementation, and operational excellence for service sales and delivery. Jarmo holds a PhD in Industrial Economics.
IMPO: Can you explain how manufacturers can work to develop a truly maintenance-oriented culture within their facilities?
JH: In creating the maintenance culture, there are many factors. First the company must give enough attention to maintenance and the maintenance team and show the organization that maintenance is a key function where the professionals are truly respected. Secondly it’s very important to think about how we can involve our people, and how we can empower our people to make the right decisions while they are working. Finally, in order to make the right decisions we need to have a clear objective. The target of the maintenance team should always be the target of the production. Production is the customer for maintenance. When we set that objective, it’s really important to also be able to give feedback, recognize and/or reward, based on the objectives. I also want to address the importance of competence management. Maintenance people are proud about their skills. The important factor is that a company evaluates the skills (technical), together with the people and give opportunity for learning, not just classroom training but also opportunity to learn on the job with specialized people.
Working in a company that specializes in industrial maintenance, we communicate to the team that everyone is working on the core function of the company, we share the customer expectations with the whole maintenance team and pay special attention to the customer’s expectations, which then convert into team targets. It is the duty of every foreman to ensure that these targets are discussed with each individual, opportunities to reach these targets are identified and the development plan is then implemented. We focus in following up and communication. At every site, visual KPI boards are used as well as regular daily, weekly and monthly meetings. As a maintenance company we get closer to maintenance technicians, being able to set, communicate and translate our core values which are, Passionate, Proud and Professional.
IMPO: In your experience, what is the biggest barrier to this culture change? Is there resistance?
JH: One barrier is communication. If it is not clear where we are going, and why – we need to articulate the need for the change very well. Very often in old maintenance cultures, that is difficult for the team or individuals to understand. Because it’s typical that the maintenance person has long been in the same position, in the same environment, and has been doing things in the same, traditional way. So he then does not recognize the need to change, so the people need to be able to get the point across. Another thing is that people fear change. For many, the fear is related to job security.
IMPO: Have you encountered this challenge within your own company?
For Quant, the biggest change happened when the ownership of the company changed. Our site managers ensured that we continued working and servicing the customer and regularly updated employees about progress of the acquisition. We increased communication by addressing that we are a global maintenance company with a clear focus. When we officially became Quant we upgraded the site facilities onto a level where it feels good to come to work. Small things make a huge difference and implementation of things like new working clothes, company signs and coffee mugs was done. Values were then communicated and discussed with every regional team. In the discussion, we have found that people really want to live our values. Passionate, proud, passionate are really what our maintenance people want to be. When we walk the talk we remove any resistance to change.
IMPO: Can you discuss a few of the greatest benefits derived from having a maintenance-oriented culture within your facility?
JH: There are several benefits – not only for the people, but also for the organization itself. In a good, open maintenance culture where people are really trusted, and their target is very clear, they are enabled to do a better job and yield better results. That is very important for the individual themselves, so the job satisfaction increases. We have to also remember that in a good culture, the bottom line of the production can be improved. It means fewer failures, and good reaction to the failures if they happen. It can really make a big change in the productivity of the manufacturer. From the perspective of our company, a maintenance service provider, a good maintenance culture means that the people are more independent. They need less guidance and traditional supervision, so when they do their job they do it properly, and that leads to increased competence levels and a competitive advantage.
We have also realized that when people are empowered to take on a more responsible role in what they are doing, they are more passionate in their communication to the team. We constantly address that our very basic value, at all levels, is job safety. That said, we express to our team that safety is everyone’s responsibility – not just the manager’s. We start to see a trend: when people conduct the safety risk assessment before starting the job, everyone is paying attention to their surroundings and how they can make their work environment safer.
For more information, visit www.quantservice.com, email [email protected], or subscribe to Quant’s magazine, Quant plus.