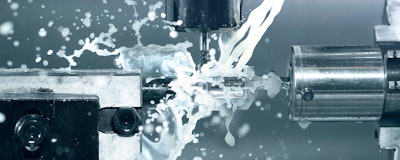
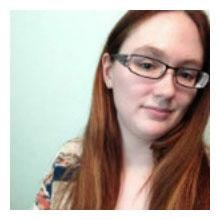
You already know just how powerful and useful CNC machining can be. But did you know automation can take it to new heights? If you’re wondering how the introduction of new technology can make even your small business vastly more productive and profitable, read on for a quick crash course in how to roll out an automated software and hardware solution for your CNC machine shop.
Create the Right Conditions for Automation
Any endeavor in CNC requires equipment with a strong pedigree and which has been designed with your application in mind. But the environment in which your machinery operates is just as important — and much easier to overlook.
Since the purpose of automated machining is to have as few human hands on the workpiece as possible, and to minimize the labor and setup time required to get started with your work, ensuring work proceeds without disruption requires some effort on your part.
But it goes beyond productivity. Automating some of the processes you’re already familiar with will enable you to create new products you weren’t able to before. That includes developing more elaborate designs, as well as harnessing new manufacturing techniques, such as additive manufacturing.
But to do all this, you need a way to monitor, in real time, these and other factors:
- The level of equipment wear and the likelihood of breakage
- The thermal expansion of your machinery
- The position of the spindle in relation to all three axes of movement
Why these three factors specifically? Because a lot of the thermal expansion algorithms you’ll find out there for automated CNC purposes don’t take environmental conditions into account. How could they? Your facility is unique to the point where even opening and closing windows and doors can throw off machining algorithms if they weren’t written with your purposes, and your environment, in mind.
Of course, monitoring wear and environmental conditions also includes how close to breakage your machine and its more delicate components are at a given moment. To do that, your automation needs to include a mechanism to shut down production if it detects a breakage.
Solution for Automated Machining Rephrase
Obtaining and reacting to the information and conditions described above doesn’t happen organically. It requires a harmonious balance of hardware and software. On the hardware side, laser-based measuring tools ensure accuracy, while software compensates in real time for thermal variations and changes in the environment.
Getting this right can be a big job, but the payoff is huge. Like any other industry that has seen its productivity enhanced manifold by the addition of computers, CNC machining requires many thousands of lines of code. And yes — those lines of code mean you get to, and have to, take your hands off the tiller and let the machines do what they were built for. The result is nearly uninterrupted production without human intervention, and with a significantly lower likelihood of error.
But after you have achieved automation, what does the endgame look like? Your solution isn’t complete without one. What’s the upper limit of your production capacity after your machines can run day and night and monitor their own maintenance needs?
As it turns out, the only real bottleneck for production after automation is how many workpieces you physically have positions for and how many tools your machine can switch between without manual intervention. As an example, a 60-position machine could run for 50 hours or so, whether the job is one large workpiece or lots of small parts.
A Breakdown of What the Right Software and Hardware Can Do for You
It would be perfectly understandable if you were reluctant about the idea of introducing higher technologies into a manufacturing process you already know well. But the fact is that CNC machining can’t really reach its full potential without the benefits technology provides. Here’s a quick breakdown.
• CAD software: You have your choice of CAD programs for feeding raw design information into your computer-aided machines. This means compatibility with your existing workflows and third parties.
• Tool selection software: Based on the CAD data you provide, an automated CNC machining solution can determine the number and type of tools necessary to machine each constituent part of your workpiece.
• Real-time maintenance software: Your automated software will monitor the conditions within your machine and workspace, in real time, which contribute most directly to wear and tear on your equipment and the quality of your output. The control algorithms can slow or stop production in response to changing conditions, and keep you apprised of maintenance needs before they stop your project altogether.
• Automatic tool measurement software: Accuracy is paramount in this field. Consequently, it makes sense to rely on laser-accurate and automatic measuring to match your toolset with the demands of your product. You can also have your software remove tools with incompatible tolerances, further reducing the likelihood of error in your project.
• Automatic tool change hardware: Your tool changer can repeatedly make new selections as production commences. As described above, productivity is limited in part by the number of positions in your tool changer.
Safety and a Final Word
The commingling of delicate and/or dangerous machinery with high-tech software has obvious advantages, but it doesn’t come without caveats. Industry experts recommend, for example, choosing just one person or a small team to oversee standardization and to determine the parameters within which your automatic machines will operate.
Allowing your operators to make changes on their own isn’t just potentially dangerous — it’s also not what automation is about. Properly deploying automation in your machine shop means having fewer "touches" on a workpiece, but more — and more accurate — checks on quality. Let the process work for you.
As you can see, all the familiar moving parts, so to speak, of CNC machining, are still there. The fundamentals haven’t changed. The difference is simply this: Automated CNC machines have “brains” that can observe and react to far more stimuli than even the most attentive machinist. There’s certainly a unique artisanal pleasure to be found in building something by hand and intuition — it’ll never go out of style, and might well be the superior choice for some of the work you do. Just note, you might never unlock upper reaches of capability and productivity if you ignore new technologies.
As with so many other industries, automation represents the future of CNC machining. Are you ready for it?
Megan Ray Nichols is a freelance science writer.