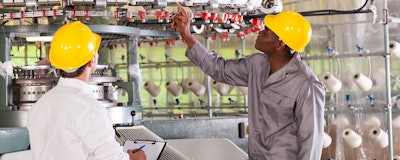
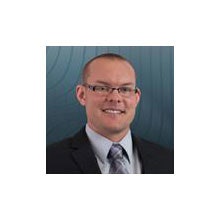
Preventive maintenance has been around for much longer than most people realize. Imagine a farmer 2,000 years ago taking his product to the market to be sold. Through trial and error he has learned that his cart can make the trip nine times before the left wheel falls off so he decides to “fix” it every seventh trip just in case. That is the pure definition of preventive maintenance driven by data, except this farmer only had one variable to deal with (how many trips to the market he had made), while today we could potentially have thousands or millions of data points. We have data collected across many industries that can be utilized at specific sites to help make better decisions about the care and maintenance of important assets. It is possible for a repetitive machine failure in the automotive industry to help drive asset care for a particular machine component in the consumer package goods industry. This is the beauty of big data, but it is only useful if we know what to do with it.
What is Big Data?
Unsurprisingly, the term “big data” has become somewhat of a buzzword within many industries as more advanced products for data collection enter the market. Strictly in the realm of maintenance, this takes the form of predictive maintenance tools such as oil analysis, thermography, motor current testing vibration, and sonics/ultrasonics, as well as computerized maintenance management systems (CMMS) that include failure coding and help with investigations. These systems and tools are generating data at an incredible rate; however, managing this wealth of data is quite the task, as mainstream maintenance is still in the early adoption phase. This new serge of data and learning how to leverage it across companies, fleets, and industries is starting to invoke major changes in how modern maintenance is being scheduled and carried out.
While managing and analyzing the data effectively is proven to be highly beneficial to companies, it is still a relatively new world, and most maintenance organizations have a certain resistance to change built into their DNA. Change becomes a cultural issue. Maintenance personnel are a loyal and trust-driven bunch, and convincing them to change practices based solely on data derived from a white-collar desk dweller is tough. Over time as that trust is earned, we are seeing massive benefits to the cost and efficiency of maintenance.
The Challenges of Big Data
Who wouldn’t want more data to help drive a decision? When first asked, most decision makers would reply, “Of course, I want any and all data that helps me make the right decision!” But this isn’t always the best case. Modern psychology suggests that the more we learn about any subject, the harder it is to make a decision about that subject. Even worse, we might actually make poorer decisions when we have more information at hand because that information might not even be important to the decision. But in our own minds, it sways us. One way to alleviate this issue is to set the criteria for the decision up front and consciously only utilize data that is relevant to the decision. Often easier said than done, another solution is to build smarter systems and programs that make the decisions very binary. Setting limits for PdM technologies that have very specific actions associated with them is one example of this. More specifically, if X, then Y, where X is a vibration reading and Y is a corrective action after the threshold is met, then the decision is already made. All we need to do is abide by the rules of the program.
Another hurdle is that extra resources may be required to number crunch the data and analyze how to apply it to existing practices, which may require upfront investment from a company before the cost-saving benefits really come into play. In today’s competitive market, it is hard for most companies to find the time, money, and energy to invest in this future state.
In a recent report developed from the airline industry (usually a leader in maintenance technologies and philosophies), it is stated “many operators report modest big data programs, reflecting limited readiness for these new challenges. Fifty-nine percent of airline respondents plan to restrict asset health management use to small subsets of data, either directly or through a third party, rather than pursuing a broad or comprehensive approach. For those using predictive maintenance, 83 percent focus on narrow subsets, while only 20 percent expect to apply predictive techniques to all available data.” Thus, it seems that airlines are pulling the highest impact but most manageable reports or, as previously discussed, they simply don’t have the resources available to manage all the data on-hand.
Certainly, organizations need to think about how they can manage the information and identify what is most relevant to their business and customers. This can then be used to improve internal processes, from production schedules to predictive maintenance. As the amount of data increases, companies with legacy IT systems could struggle, which is why more advanced IT systems are attractive solutions to many companies; they provide end-users with a comprehensive tool that can streamline and manage key company information and aid the transfer of data more easily.
How Big Data and Analytics Can Reduce Maintenance Costs
It is understood that we can utilize PdM technology to drive real time, condition based care for our machines, but Big Data focuses on the bigger picture. By taking that data and warehousing it with other data points from other industries or facilities we can start to formulate better strategies for critical machine care.
One example of this is a simple gearbox oil change out. At most facilities when asked why is that particular gearbox changed out on a yearly interval, the most common reply is “that’s the way it has always been done.” What if we could use big data to tell us that out of thousands of gearboxes of like make, model, environmental, and operational severity, that the lubricant will last 36 months based on oil analysis health reports? This would mean a reduction in downtime, manpower, lubricant purchases, fault inducing events, and much more. This is just one example out of thousands that rely on big data.
Through big data, a facility has the ability to carry out predictive analytics, which can make way for prognostic maintenance work rather than diagnostic, thus improving reliability and saving money — once again by moving the maintenance needle closer to proactive work rather than reactive work. As more companies understand the true value of big data and how it can modernize their business processes and compliment asset modernization, it will become a staple of world-class companies and those that choose not to change will slowly fall behind and wither. Nearly every industry will benefit from improved, more streamlined maintenance processes, and big data is a subject matter at the top of the list to drive companies in that direction.
Jeremy Wright, CMRP, CRL, PE, is Director of Product Management at Advanced Technology Services, Inc.