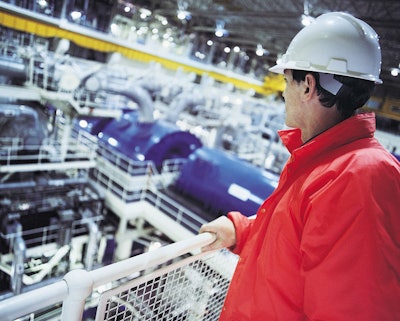
Outsiders tend to generalize the manufacturing industry as a monotonous, labor-intensive profession. While this may be true in some cases, specialty niches, such as medical device manufacturing, call for more precision and accuracy as opposed to sheer brute strength. Those equipped with the right skills for the industry will also be more aware of the potential pitfalls therein.
Here are a few of the most widespread medical manufacturing maintenance problems and how you can combat them and stay abreast of current regulations to help your company function more smoothly.
Medical Manufacturing Pitfall No. 1: Poor Documentation
Failure to document common processes and procedures is one of the most common pitfalls in the industry. Compounding this problem further, some manufacturers don't follow their established protocol in the first place, which renders their documentation moot.
Maintaining control over internal protocol ensures the quality and consistency of products as well as the safety of your workers. For best results, update and review your written procedures on a regular basis. Inform your staff of any recent additions or revisions by updating their training requirements or holding group meetings.
Medical Manufacturing Pitfall No. 2: Lack of Corrective Action
A lack of appropriate or timely corrective action is also a frequent problem. Instead of causing even more delays and potential issues, manufacturers should proactively work with hospitals, laboratories and institutions to implement upgrades and address problems as soon as possible. Many hospitals maintain their own preventative or corrective maintenance procedures, but their in-house capabilities are typically quite limited.
Make sure to explain the steps you've taken to address any known issues. Not only does this give the institution a better idea of the changes you've implemented, but it can also provide a heads up on any long-term or ongoing actions.
Medical Manufacturing Pitfall No. 3: Poor Sterilization
Some pitfalls, such as sterilization, are unique to the medical device manufacturing sector. Although we don't necessarily think of sterile manufacturing environments, this kind of cleanliness is required when working with certain medical equipment.
To achieve a level of sterilization in tandem with FDA regulations, look at both your materials and your tools. Certain technology, such as RF sealing, can be used with IV bags and similar products to minimize contact with external, unsterilized hardware. Investing in such tools can save money down the line by protecting your product.
Medical Manufacturing Pitfall No. 4: Insufficient Supplier Controls
Although we can't have a direct effect on the actions of our suppliers, we can implement internal controls to guarantee the quality and consistency of incoming parts and materials. For example, next-gen supply chain management software can:
- Track inspection data
- Maintain detailed supplier records
- Ensure organization throughout the entire chain
Medical Manufacturing Pitfall No. 5: Incomplete Training Procedures
As a medical device manufacturer, you must train your entire staff. The FDA says every manufacturer should have procedures in place to identify and offer training. It also mandates documentation of such training programs and initiatives.
The level of training varies depending on the role of individual workers. Every single employee should receive training in accordance with your standard operating procedures, but some, including those who participate in soldering or welding, require additional certification. Those placed in roles of quality control should be instructed and trained to look for common defects or issues with production.
In some cases, employee retraining might be necessary. This usually stems from a recommended corrective action as issued by the FDA.
Medical Manufacturing Pitfall No. 6: Laboratory Monitoring And Calibration
This category encompasses environmental monitoring, calibration of mechanical tools and even internal process controls. Effective asset management, equipment reporting and documentation can ease some of this burden.
Small hospitals and institutions have begun using equipment maintenance management programs, or EMMPs. Typically available as an external service, these programs provide them with the technical expertise needed to calibrate tools and perform the necessary upgrades. Your company can capitalize on this trend to increase your own profitability and achieve a greater level of connectedness with the facilities you serve.
Maintaining Productivity In The Face Of Evolving Guidelines
When it comes to manufacturing, few professions are more stringent than the medical device sector. It's all for good reason. Someone's life may very well depend on the equipment you put on the market. Considerations such as this, as well as ever-evolving guidelines from organizations like the FDA, make the industry a lucrative business for those who can avoid the pitfalls.
Megan Ray Nichols is a freelance science writer.